Galvo-Resonant Scanners and Controllers
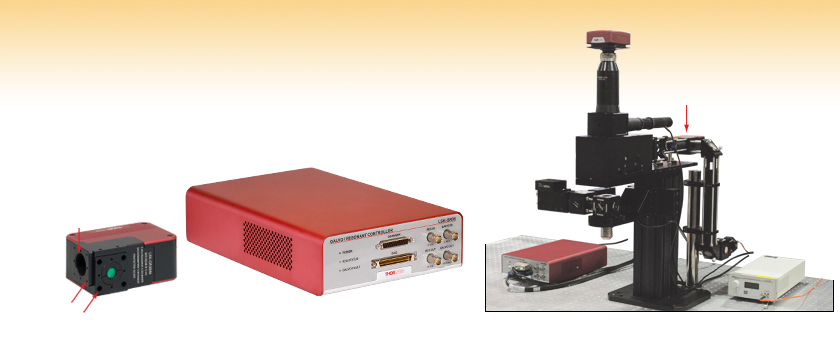
- 8 kHz or 12 kHz Resonant Frequency for High-Speed Scans
- Drive Using Software, BNC, and National Instruments Card
- Pre-Aligned, Wired, and Calibrated for Plug-and-Play Operation
SM1 Threading on Output Port
LSK-GR08
8 kHz Galvo-Resonant Scanner
Application Idea
LSK-GR12 Scanner and Controller integrated into a DIY laser scanning Cerna® microscope.
30 mm Cage Mounting Holes

Please Wait

Click for Details
Cutaway View of Galvo-Resonant Scan Head
The scan lens being used with the scan head needs to be positioned such that its focus is at the midpoint between the resonant mirror (X) and the galvo mirror (Y). The distance between the mirrors is indicated by the green line. For the input, that distance corresponds to 28.655 mm, while for the output, that corresponds to 28.965 mm. If a scan lens has a focal point that falls on the yellow or blue line and not in the middle of the green line, then the lens cannot perform as intended.
Features
- 8 kHz or 12 kHz Resonant Scanner Frequency for High-Speed XY Scans
- Accept Beams up to Ø5 mm
- Control using BNC Connectors for Position Control and Readout, 68-Pin National Instruments Cards and Breakout Boxes for Fine Galvo Positioning, and GUI for Resonant Mirror Tuning
- Compact Scan Head Housing is SM Threaded, 30 mm Cage System Compatible, and Post Mountable
Our Galvo-Resonant (GR) Scanners are available with 8 kHz or 12 kHz resonant scanner frequency. Each scanner contains one resonant scan mirror and one galvo scan mirror that deflect an incident laser beam in X and Y, respectively. The resonant frequency of the resonant scan mirror enables much higher-speed scans than a galvo-galvo system. The LSK-GR08(/M) 8 kHz and LSK-GR12(/M) 12 kHz GR scanners are used in our Bergamo® II multiphoton microscopes and complete Cerna®-based confocal systems. In our Bergamo system, the 8 kHz GR scanner can achieve 30 fps at 512 x 512 pixels image resolution, while the 12 kHz GR scanner can achieve 45 fps at 512 x 512 pixels image resolution.
The beam can be steered via two BNC connectors for simple uni-directional scans. For fine tuning and bi-directional scanning functionality, we provide a GUI for Windows® to adjust the scan range of the resonant scan mirror and the sync signal offset, as well as a National Instruments (NI) 68-pin connector to directly control and monitor the galvo scan mirror via an NI card or breakout box (not included). See the Control tab for additional information. The scanners are also compatible with Vidrio's ScanImage software.

Click for Details
Optical diagram of the LSK-GR12 Galvo-Resonant Scanner in a DIY Cerna® laser scanning microscopy setup. Please note the distances are not to scale.
Each scan mirror has a protected silver coating that provides high reflectance in the visible and NIR; see the Specs tab for details. Since the coating is metallic, the performance varies minimally over the scan range of the mirror. The scan head input port also features a removable NIR window that, when combined with a scan lens on the output port, greatly reduces the audible noise from the system.
Mounting
Each scan head is equipped with internal SM1 threads on the output face. Internal SM05 (0.535"-40) and internal SM1 (1.035"-40) threads can also be accessed by removing the NIR window installed on the input face using a SPW801 spanner wrench. There are four Ø6 mm bores on the input face and four 4-40 taps on the output face, making the scan head compatible with our 30 mm cage system. Four 1/4"-20 (M6) tapped holes are located on the bottom for post mounting with our Ø1" posts.
Item # | LSK-GR08(/M) | LSK-GR12(/M) | |
---|---|---|---|
Scan Head | |||
Galvo Scan Range | ±7.5° Mechanical (±15° Optical) | ||
Resonant Scan Range | ±5° Mechanical (±10° Optical) |
±2.5° Mechanical (±5° Optical) |
|
Beam Diameter | 5 mm (Max) | ||
Galvo Motor and Position Sensor | |||
Scan Axis | Y Direction | ||
Repeatability | 8 µrada | ||
Small Angle Step Response | 260 μs (Typical) | ||
Maximum Angle Step Responseb |
1.6 ms (Sine) 2.0 ms (Sawtooth) |
||
Linearity | 99.9% (Typical) 99.5% (Min) |
||
Scale Drift | 50 ppm/°C (Max) | ||
Zero Drift | 15 μrad/°C (Max) | ||
Average Current |
2.4 A | ||
Peak Current | 8.0 A | ||
Resonant Scanner | |||
Scanning Frequency | 7910 ± 15 Hz | 12000 ± 15 Hz | |
Sync Signal Frequency | 8 kHz | 12 kHz | |
Scan Axis | X Direction | ||
Input / Output | |||
Galvo BNC | Bandwidth | 0 - 500 Hzc | |
Input Voltage | ±10 V | ||
Input Impedance | 1 kΩ | ||
Output Voltage | -4 to 4 V | ||
Output Impedence | 100 kΩ | ||
Signal Type | DC, Sine, or Sawtooth Wave | ||
Input Scale Factor | 1.33 V per Mechanical Degree | ||
Output Scale Factor | 0.533 V per Mechanical Degree | ||
Resonant BNC | Input Voltage | 0 to 5 V | |
Input Impedance | 5 kΩ | ||
Signal Type | DC | ||
Sync Signal Voltage | 0 to 6 V (TTL)d | ||
Sync Signal Impedance | 50 Ω | ||
Sync Signal Pulse Width | 50% Duty Cycle | ||
Resonant Scanner Computer Control | USB 2.0e | ||
Controller Voltage Input | 90 - 264 VAC, 50 - 60 Hz | ||
Power Consumption | 120 VA (Max) | ||
Physical | |||
Scan Head Dimensions | 4.60" x 3.45" x 2.00" (116.8 mm x 87.7 mm x 50.8 mm) |
||
Controller Dimensions | 12.30" x 7.87" x 3.12" (312.4 mm x 199.8 mm x 79.2 mm) |
||
SM Threading | Internal SM05 (0.535"-40) Internal SM1 (1.035"-40) |
||
Cage Compatibility | 30 mm Cage (4-40 Tap, 4 Places; Ø6 mm Bore, 4 Places) |
||
Post Mounting | 1/4"-20 (M6) Tap, 4 Places | ||
Operating Temperature Range | 0 to 50 °C |
Item # | LSK-GR08(/M) | LSK-GR12(/M) | |
---|---|---|---|
Scanning Mirrors | |||
Coating | Protected Silver | ||
Reflectance (Average) | 350 - 450 nm, >70% | ||
450 - 550 nm, >90% | |||
550 - 650 nm, >92.5% | |||
650 - 1080 nm, >95% | |||
1080 - 7000 nm, >97% | |||
Front Surface Flatness |
λ/4 (at 633 nm) | ||
Front Surface Quality | 60-40 Scratch-Dig | ||
Galvo Scanning Mirror | |||
Substrate | Silicona | ||
Clear Aperture | Within 0.020" of Any Edge or Rail | ||
Scan Range | ±7.5° Mechanical (±15° Optical) | ||
Resonant Scanning Mirror | |||
Substrate | Optical Grade Beryllium | ||
Clear Aperture | Ellipse 7.2 mm Major Axis 5.0 mm Minor Axis |
||
Scan Range | ±5° Mechanical (±10° Optical) | ±2.5° Mechanical (±5° Optical) | |
NIR Windowb | |||
Substrate | UV Fused Silicaa | ||
Thickness | 3 mm | ||
AR Coating Reflectance | Ravg < 0.75% from 660 to 1420 nm |

Click to Enlarge
Typical Reflectance of One Galvanometric Mirror at 45° AOI
Please note that lot-to-lot variations will occur in the reflectance.

Click to Enlarge
Click for Raw Data
Typical Reflectance of the NIR Window at 6° AOI

Click to Enlarge
Click for Raw Data
The substrate used for the NIR window is UV fused silica. For reference, we provide the transmission of a 10 mm thick window of uncoated UV fused silica. The AR coating on both sides of the window will decrease the reflectance at each interface, improving the transmission over the AR coating range.

Click to Enlarge
Cutaway View of Galvo-Resonant Scan Head
The scan lens being used with the scan head needs to be positioned such that its focus is at the midpoint between the resonant mirror (X) and the galvo mirror (Y). The distance between the mirrors is indicated by the green line. For the input, that distance corresponds to 28.655 mm, while for the output, that corresponds to 28.965 mm. If a scan lens has a focal point that falls on the yellow or blue line and not in the middle of the green line, then the lens cannot perform as intended.
Click to Enlarge
The front of each controller has a DB25 connector for the scan head, as well as BNC connectors and an NI 68-pin connector for position control and readout. The LSK-GR08 controller is shown.
Click to Enlarge
The back of each controller has a USB port to control the resonant scanner of the scan head, as well as a fuse holder, power switch, and grounding pin connector. The LSK-GR08 controller is shown.
RES IN and GALVO IN
BNC Female

RES IN and GALVO IN | ||
---|---|---|
Resonant In | Signal Type | DC |
Voltage Range | 0 to 5 V | |
Impedance | 5 kΩ | |
Galvo In | Signal Types | DC, Sine, or Sawtooth Wave |
Voltage Range | ±10 V | |
Impedance | 1 kΩ | |
Scale Factor |
1.33 V per Mechanical Degree | |
Bandwidth | 0-500 Hz (Max)a |
X OUT and Y OUT
BNC Female

RES OUT and GALVO OUT | ||
---|---|---|
Resonant Out | Voltage Range |
0 to 6 V (TTL) |
Impedance | 50 Ω | |
Pulse Width | 50% Duty Cycle | |
Galvo Out | Voltage Range | ±4 V |
Impedance | 100 kΩ | |
Scale Factor | 0.533 V per Mechanical Degree |
Computer Connection USB 2.0 Type B

USB Type B to Type A Cable Included
DAQ
NI 68-Pin Connector

DAQ | ||
---|---|---|
Pin | Name | Description |
21 | Galvo Position In | ±10 V Input 100 kΩ Impedance |
33 | Galvo Current | Output Voltage Proportional to Motor Current 1 kΩ Impedance |
63 | Galvo Position Out | ±4 V Output 1 kΩ Impedance |
65 | Error | Difference Between Command Input and Position Output 1 kΩ Impedance |
66 | Galvo Velocity | Output Voltage Proportional to Scanner Velocity 1 kΩ Impedance |
Below is a link to the latest version of the software for our galvo-resonant scanners. This software controls the resonant scan range (field size); control the galvo scan axis using either the BNC input or the National Instruments (NI) 68-pin connector on the controller. The software download package also includes the latest firmware as well as a LabVIEW software development kit (SDK) and support documentation to allow the resonant scan mirror of the scan head to be controlled using custom imaging software. See the manual by clicking on the Docs icon below ( ) for installation instructions and use.

LSK-GR08(/M) Controller Software for the Resonant Scanning Axis

LSK-GR12(/M) Controller Software for the Resonant Scanning Axis
Scanner Control I/O Methods | |
---|---|
Resonant Scan Mirror | |
Scan Range |
BNC In (DC) USB Control (GUI or SDK) |
TTL Sync Signal Out | BNC Out |
TTL Sync Signal Offset |
USB Control (GUI or SDK) |
Galvo Scan Mirror | |
Galvo Position In |
BNC In (DC or Sine) NI Connector (DC or Sine) |
Galvo Position Out | BNC Out NI Connector |
Galvo Velocity | NI Connector |
Galvo Current | NI Connector |
Galvo Error | NI Connector |
Galvo-Resonant Scanner Control
The galvo-resonant scanner has three control I/O methods - BNC, USB, and NI connection - and, depending upon your imaging needs, utilizing different control methods may be necessary. See the table to the right for the different I/O ports for galvo-resonant control, and the Pin Diagrams and Software tabs for specifics.
Uni-Directional Scanning
The resonant scan mirror continuously swivels the mirror at a fixed frequency. Only the maximum scan angle is adjustable, which will adjust the width of the scan field. The galvo positioning signal will need to be synchronized with the TTL signal output from the resonant scan mirror in order to map the field of view in X and Y. As the resonant scan mirror scans in the X direction, we recommend a sawtooth signal to adjust the scan angle in Y, creating a zig-zag motion through the scan field. Uni-directional scans do not require tuning the TTL sync signal offset, nor the galvo velocity, current, or error, but can be used to maximize the usable image field size and minimize image distortions.
Bi-Directional Scanning
To utilize both the forward and backward lines of the resonant mirror scan, the TTL signal output from the resonant scan mirror needs to be tuned such that the rising edge of the TTL signal is synchronized to the beginning of the acquired forward scan line (see left image below).
Please note for the LSK-GR12(/M), the TTL clock is pre-tuned and does not require adjustment. For the LSK-GR08(/M), the timing can be tuned manually using the GUI or through the SDK. If the TTL signal is not tuned correctly, the forward scan line will be offset with respect to the return scan line, resulting in a jagged scan pattern (see right image below). Bi-directional scans do not require the galvo velocity, current, or error outputs, but can be used to maximize the frame rate.

Click to Enlarge
Resonant Scanner TTL Clock Compared to Scan Angle

Click to Enlarge
Bi-Directional Scan Lines With Synced and Unsynced TTL Offset
Shipping List
Each Galvo-Resonant Scanner Includes the Following:
- Scan Head
- Controller
- DB-25 Scan Head Control Cable
- Region-Specific Power Cord
- USB Cable (A to B)
- Galvo/Resonant Scanner Software CD
- Manual (Not Shown)
Note because the galvo-resonant scanner can be steered using multiple input signals depending upon scanner functionality, neither BNC cables nor an NI 68-pin cable are included.

Click to Enlarge
Item # Shown: LSK-GR08

Click to Enlarge
Item # Shown: LSK-GR12
Scanning Methodologies | |
---|---|
Galvanometer-Based Scanning | Advantage: Flexible Scan Positioning Disadvantage: Slow |
Resonant Scanning |
Advantage: Scan Speed Disadvantage: Unable to Adjust Center of Resonant Scan Area; Nonlinear Dwell Time |
Galvo Versus Resonant Scanning
Galvo and resonant scanning provide orthogonal advantages due to their respective scanning mechanisms. As a result, it is important to choose the scanning methodology that is ideal for the intended application. For instance, galvo-galvo scanning is optimal for user-defined scanning paths and shapes, while galvo-resonant scanning is optimal for high-speed scans.
Galvanometer-based scanning uses a galvanometric mirror steered by an assembly system of a servo-controlled motor and a positioning actuator. The angle of the mirror is tightly controlled in the system and can be controlled via an external signal for accurate positioning and scanning, providing the flexibility for user-defined scan lines and areas. Due to inertia, the velocity of a galvo scanner has a low upper limit.
While resonant scanning also utilizes a galvanometric mirror, the scanning method differs significantly. In a manner similar to that of a tuning fork, the mirror assembly is driven at its resonant frequency in order to reach over 10X faster scan speeds than that of galvo scanning. The speed of the resonant galvanometric mirror varies sinusoidally with the scanning angle in order to maintain smooth motion over the course of the scan, which results in longer dwell times at the edges of the FOV and shorter dwell times at the center of the scan. The combination of this effect and the fixed center position and frequency of the resonant scanner results in an inability to scan complex patterns or adjust the scanning speed. The only user-variable parameter of the resonant scan mirror is the maximum scan angle.
Posted Comments: | |
Kevan Bell
 (posted 2020-11-26 11:13:46.817) Would you be able to offer this with a UV-enhanced coating on the mirror? YLohia
 (posted 2020-12-01 10:30:41.0) Thank you for contacting Thorlabs. Custom versions of these can be requested by emailing techsupport@thorlabs.com. We will discuss the possibility of offering this customization directly. user
 (posted 2018-06-21 03:52:26.613) Hello. I want to know whether the resonant mirror's scanning velocity is variable or not. YLohia
 (posted 2018-06-26 10:12:42.0) The scan velocity is variable from 0-500 Hz for non-resonant mode. The resonant mode, however, is 7910 ± 15 Hz. |

- 8 kHz Resonant Scanner Frequency for High-Speed XY Scans
- Max Scan Range for a Square Scan: 10° Mechanical Peak-to-Peak (20° Optical Peak-to-Peak)
- Protected Silver Coating for High Reflectance in Visible and NIR (350 nm to 7 µm Wavelength Range)
- NIR Window AR Coated for 660 nm - 1420 nm Reduces System Noise
- SM-Threaded, 30 mm Cage System Compatible, and Post-Mountable Scan Head
Thorlabs' LSK-GR08(/M) 8 kHz Galvo-Resonant Scanner and Controller is ideal for high-speed imaging. This scanner offers a large scan field with a galvo optical scan range of ±15° (±7.5° mechanical scan range) and a resonant optical scan range of ±10° (±5° mechanical scan range). Intended for plug-and-play operation, the scan head connects to the controller using the included DB25 cable. See the Shipping List tab for additional accessories.
The galvo mirror can be controlled using a BNC cable for simple uni-directional scans or a National Instruments (NI) 68-pin connector for fine positioning. The resonant mirror can also be controlled via a BNC cable for simple uni-directional scans, or with the included control software package for bi-directional scanning; see the Software and Control tabs for more information. Each scan mirror has a protected silver coating that provides high reflectance in the visible and NIR, see the Specs tab for details.
The input face of the scan head has four Ø6 mm bores spaced for our 30 mm cage system. By removing the NIR window installed on the input face using a SPW801 spanner wrench, internal SM05 (0.535"-40) and internal SM1 (1.035"-40) threads become accessible. The output face is equipped with internal SM1 threads and four 4-40 taps for our 30 mm cage system. The scan head is also post mountable with four 1/4"-20 (M6) tapped holes located on the bottom. It weighs 0.76 kg, so it may be useful to support it directly using a Ø1" post.
Please Note: The scan lens needs to be positioned such that the scanning distance is at the midpoint between the galvo and resonant mirrors. The distance from the input face to the midpoint is 28.655 mm, while the distance from the output face to the midpoint is 28.965 mm; see the image in the Overview tab. To mount an SL50-CLS2, SL50-2P2, or SL50-3P scan lens at the correct distance from the scanner a special adapter is available by contacting Tech Support. For the CLS-SL scan lens, an LCP02(/M) cage system size adapter can be used to convert the 30 mm cage system to a 60 mm cage system to mount and position this scan lens at the correct distance using a LCP8S cage plate.

- 12 kHz Resonant Scanner Frequency for High-Speed XY Scans
- Max Scan Range for a Square Scan: 5° Mechanical Peak-to-Peak (10° Optical Peak-to-Peak)
- Protected Silver Coating for High Reflectance in Visible and NIR (350 nm to 7 µm Wavelength Range)
- NIR Window AR Coated for 660 nm - 1420 nm Reduces System Noise
- SM-Threaded, 30 mm Cage System Compatible, and Post-Mountable Scan Head
Thorlabs' LSK-GR12(/M) 12 kHz Galvo-Resonant Scanner and Controller is ideal for high-speed imaging. This scanner offers a large scan field with a galvo optical scan range of ±15° (±7.5° mechanical scan range) and a resonant optical scan range of ±5° (±2.5° mechanical scan range). Intended for plug-and-play operation, the scan head connects to the controller using the included DB25 cable. See the Shipping List tab for additional accessories.
The galvo mirror can be controlled using a BNC cable for simple uni-directional scans or a National Instruments (NI) 68-pin connector for fine positioning. The resonant mirror can also be controlled via a BNC cable for simple uni-directional scans, or with the included control software package for bi-directional scanning; see the Software and Control tabs for more information. Each scan mirror has a protected silver coating that provides high reflectance in the visible and NIR, see the Specs tab for details.
The input face of the scan head has four Ø6 mm bores spaced for our 30 mm cage system. By removing the NIR window installed on the input face using a SPW801 spanner wrench, internal SM05 (0.535"-40) and internal SM1 (1.035"-40) threads become accessible. The output face is equipped with internal SM1 threads and four 4-40 taps for our 30 mm cage system. The scan head is also post mountable with four 1/4"-20 (M6) tapped holes located on the bottom. It weighs 0.76 kg, so it may be useful to support it directly using a Ø1" post.
Please Note: The scan lens needs to be positioned such that the scanning distance is at the midpoint between the galvo and resonant mirrors. The distance from the input face to the midpoint is 28.655 mm, while the distance from the output face to the midpoint is 28.965 mm; see the image in the Overview tab. To mount an SL50-CLS2, SL50-2P2, or SL50-3P scan lens at the correct distance from the scanner a special adapter is available by contacting Tech Support. For the CLS-SL scan lens, an LCP02(/M) cage system size adapter can be used to convert the 30 mm cage system to a 60 mm cage system to mount and position this scan lens at the correct distance using a LCP8S cage plate.