Vytran® Automated Glass Processors with Integrated Cleaver
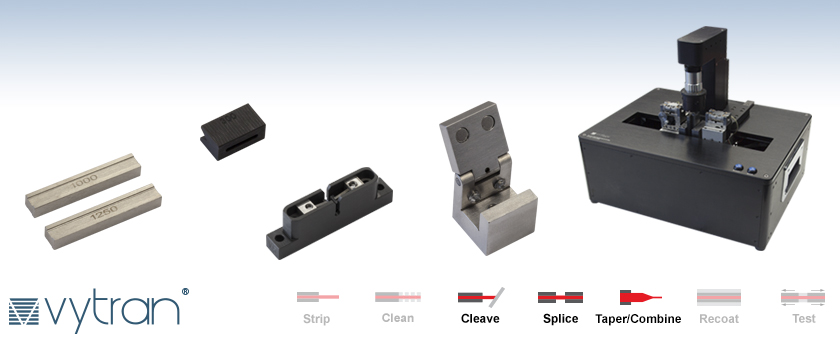
- Fabricate Fiber Splices, Tapers, Terminations, Couplers, and Combiners
- Built-In Fiber Cleaver and Real-Time Fusion Imaging
- Automated XY and Rotational Alignment
- Two Models for Optical Fiber Claddings up to Ø1.25 mm or Ø1.7 mm
VHT1
Transfer Clamp
GPX3850
Glass Processor with Built-In Cleaver
VHA10
Fiber Holder Top Insert
VHG300
Graphite V-Groove
FTAV5
Graphite Filament Assembly
Glass Processor Workstations, Filaments, Inserts, and Accessories All Sold Separately

Please Wait
Features
- Fabricate Splices, Tapers, Terminations, Couplers, and Combiners
- Automated XY and Rotation Alignment
- Diamond Cleave Blade Integrated into Splice Head
- Real Time Hot Imaging of Fibers During Splicing or Tapering
- Compatible with Single Mode, Multimode, Polarization-Maintaining, and Specialty Fibers
(See Applications Tab for Examples) - Create Low-Loss (~0.02 dB) Splices in Standard Glass Fibers (See Specs Tab for Details)
- Measure Fiber Circularity, Centroid, and Core Eccentricity Using End-View Imaging
- Software with Process Development GUI and Splice Process Library (See Software Tab for Details)
Build Your System
- Glass Processor Workstation for Fibers with Claddings up to Ø1.25 mm (GPX3800) or
up to Ø1.7 mm (GPX3850) - Choose from Six Graphite and Three Iridium Filament Assemblies (One FTAV4 Graphite Filament Pre-Installed in System)
- Choose Top and Bottom Inserts (Two Top Inserts and Two Bottom Inserts Required; See Fiber Holder Inserts Tab for More Information)
- Optional Multi-Fiber Holder Bottom Inserts for Making Couplers or Combiners
- Optional Fluorine-Doped Capillary Tubes (For Making Specialty Couplers or Combiners)
- Optional Liquid Cooling System for Tapering Applications (One Included with the GPX3850)
- Optional Fiber Taper Software and Handling Fixtures
- Optional Fiber Combiner Loading Fixture
- Optional Ultrasonic Cleaner for Preparing Fibers Prior to Splicing
- Optional Mountable Gooseneck Light

Click to Enlarge
An illustration of the tension-and-scribe method as used by the GPX3800 and GPX3850 to produce a flat cleave. Tension is applied along the optical axis of the fiber prior to cleaving. A diamond blade then scribes the fiber, and the tension causes the scribe to propagate across the fiber in a plane that is orthogonal to the direction of the tension.

Click to Enlarge
False Color Temperature Overlay During Taper Draw Process
Thorlabs' Vytran® Optical Fiber Glass Processors are versatile platforms designed for fabricating splices, tapers, couplers, terminations, and combiners using optical fibers. The glass processors sold on this page feature a patented precision cleaver integrated into the splice head (US Patent: 9,977,189) and real-time process monitoring via the hot imaging camera, as well as automated pre-splice alignment for the XY position of the fiber edge and rotational orientation of the fiber core. This combination of features allows users to cleave and splice polarization-maintaining fibers and specialty fibers with microstructured cores on a single station, while maintaining the capability to fabricate fiber tapers and terminations in a wide variety of fiber types. The GPX3800 glass processor is compatible with fibers up to Ø1.25 mm cladding while the higher power GPX3850 can process fibers up to Ø1.7 mm cladding.
These glass processors incorporate a filament-based furnace assembly that provides a uniform and precisely controlled, high-temperature heat source. Because filament material and size can be interchanged easily (9 different filament options are available below), a wide range of fiber cladding diameters and specialty fiber types can be accommodated using the same system. Precise control over fiber position and orientation enables a number of advanced fiber processing applications from low-loss splicing in dissimilar fibers to the creation of adiabatic fiber tapers, fiber terminations, or fused fiber couplers (please see the Applications tab for examples).
The fiber cleaver integrated into the splice head uses the same "tension-and-scribe" process as the LDC401 Series Fiber Cleavers and is compatible with fiber cladding diameters up to 400 µm. As seen in the image to the right, tension is applied along the length of the fiber followed by an automatic scribing process utilizing a diamond cleave blade. After the blade scribes the fiber, tension is maintained, causing the scribe to propagate across the fiber width and complete the cleave.
True Core Imaging® and Hot Image Camera
These fiber processing systems employ True Core Imaging technology to provide high-resolution images for fiber measurement and alignment. A digital CCD camera and mirror tower are integrated into the fiber processing workstation to allow for clear side-view and end-view images of the fiber core and cladding. This imaging feature allows for automated measurement of fiber properties (core/cladding diameters, cleave angle, etc.), provides feedback for the automated alignment system, and enables calculation of an accurate splice loss for splices with similar or dissimilar fiber types. The VHB00 or VHB05 top insert (sold below) is required in order to use automated end-view alignment.
Through ND filters integrated into the camera system, users can obtain real-time images of fibers during the splicing/tapering process (see the images to the right). This advanced imaging feature provides instant feedback on splice/taper quality, allowing users to quickly develop processes and optimize parameters for their application.
Options and Accessories
A complete glass processor requires the purchase of a glass processor workstation (choose one below), two top inserts (sold separately below), two bottom inserts (sold separately below), and a >99.999% purity argon gas tank (not available from Thorlabs). The Fiber Holder Inserts tab has information to aid in choosing pairs of fiber holder inserts, as well as insert installation instructions. An FTAV4 Graphite Filament (for Ø125 - Ø600 µm cladding) is included with each glass processor; additional filaments made from different materials or for other fiber cladding diameters are sold separately below. See the Tutorial Videos tab above for videos on how to install filaments and perform filament maintenance. An ultrasonic cleaner for preparing fibers for splicing can be purchased separately below.
Several optional add-ons are available for these systems to enable specialized applications. The GPXWCS Liquid Cooling System helps cool the furnace assembly when the filaments are used for extended heating times and is recommended for customers interested in creating long fiber tapers. It comes included with the high-power GPX3850 and can be purchased as an add-on for the GPX3800. Multi-fiber holder bottom inserts are used when fabricating couplers or combiners and are designed to hold two or three fibers in close proximity during heating. Thorlabs also offers a Fiber Taper Software Add-On and Taper Handling Fixtures (sold below), which include software application files and fixture upgrades that enable high repeatability when fabricating and handling microtapers, nanotapers, fused fiber couplers, or wavelength division multiplexers. The software add-on and fixtures can be purchased separately or together as a kit. We also offer the GPXCFXL Fixture that supports the positioning of fiber bundles during combiner fabrication. The GPXL1 Gooseneck Light is available for end-view illumination of the fiber or for general lighting during alignment. It can be mounted to the left or right side of the workstation.
Replacement blades for the fiber cleavers in the glass processing workstations are also available below.
Compatible Vytran Fiber Processing Systems | |||||||
---|---|---|---|---|---|---|---|
Fiber Preparation Station (Strip and Clean) |
Large-Diameter Fiber Cleavers | Portable Large-Diameter Fiber Cleaver | Large-Diameter Fiber Splicer | CO2 Laser Glass Processing System (Splice and Taper) |
Automated Glass Processing Systems with Integrated Cleaver (Cleave, Splice, and Taper) |
Automated Glass Processing Systems (Splice and Taper) |
Recoaters, Proof Testers, and Recoaters with Proof Testers |
Item # | GPX3800 | GPX3850 |
---|---|---|
Splicing Specifications | ||
Fiber Types (Non PM) | Single Mode, Multimode, Photonic Crystal, Large Mode Area, Non-Circulara | |
Fiber Types (PM) | Panda, Elliptical, Bow-Tiea | |
Fiber Cladding Diameter | Up to 1.25 mm (Max) | Up to 1.7 mm (Max) |
Fusion Method | Filament Fusion | |
Filament Temperature Range | Room Temperature to 3000 °C | |
Splice Loss | 0.02 dB (Typical)b | |
Splice Loss Estimation | True Core Imaging® Technology | |
Splice Strength | >250 kpsi (Typical)c | |
Strength Enhancement | Fire Polish | |
Polarization Cross Talk | Panda: >35 dB Other Fiber Types: >30 dB |
|
Fiber Inspection | ||
Fiber Side Viewing | True Core Imaging Technology | |
Fiber End Viewing | Facet Inspection and PM Core Alignment (VHB00 or VHB05 Top Insert Required) |
|
Core / Cladding / Fiber Diameter | Automated Measurement | |
End Face Inspection | Inspection via GUI Display | |
Cleave Angle | Automated Measurement | |
Fiber and End Face Alignment | ||
Fiber Z-Axis Movement | 180 mm (Max) | |
Z-Axis Movement Resolution | 0.25 µm via Stepper Motor | |
XY Axis Fiber Positioning Resolution | 0.02 µm via Stepper Motor | |
Rotation Alignment | Fully Automated End-View Alignment for Panda, Bow Tie, Elliptical-Core Fibers External Extinction Ratio Feedback for Automatic Alignment of PM Fiber Types |
|
Rotation Drive Resolution | 0.02° | |
Rotation Travel | 200° | |
Tapering | ||
Tapering Length | ~2 mmd (Min); Up to 150 mmd (Max) | |
Tapering Ratio (Max) | Adiabatic Tapers up to 1:10 (Ratios Up to 1:100 Possible) | |
Tapering Speed | 1 mm/s (Typical)e | |
Adiabatic Tapering Loss | <0.01 dB (Typical) | |
Computer and Software | ||
PC Computer | Included | |
Splice Files | Built-In Library for Common Fibers and Processes | |
Physical | ||
Size | 16.0" x 12.5" x 6.3" (410 mm x 320 mm x 160 mm) | |
Weight | 45 lbs (20 kg) | |
External Power Supply | Universal Input: 96 - 260 VAC, 47 - 63 Hz, Single Phase Glass Processor Input: 12 V and 48 V DC, 10 A PC Input: 115 or 230 VAC, 47 - 63 Hz, Single Phase |
|
Gas Supply | Argon, >99.999% Purity at 12 psig (Not Included) | |
Environmental | ||
Operating Temperature | 15 to 40 °C | |
Altitude Range | 0 to 2000 m Above Sea Level | |
Operating Humidity | 0 to 75% Relative Humidity (Non-Condensing) | |
Storage Temperature | -20 to 60 °C | |
Storage Humidity | 0 to 90% Relative Humidity (Non-Condensing) |
Fiber Holder Inserts Selection Guide (Top Inserts and Standard or Transfer Bottom Inserts)
Introduction
Fiber Holder Inserts, which are designed to hold various sized fibers within the glass processors, must be purchased separately. Standard and transfer bottom inserts have V-grooves to hold the fiber, while the top inserts each feature a recessed, flat surface that clamps the fiber against the V-groove in the bottom insert. Each top and bottom insert is sold individually, as the fiber outer diameter clamped by the left and right holding blocks may not be the same. At least two top inserts and two bottom inserts are required to operate the glass processor. For multi-fiber inserts, which are used to make fused couplers or combiners, the recommended top inserts are listed in the multi-fiber insert table.
The table below indicates the maximum and minimum outer diameters that can be accommodated by different combinations of top and bottom inserts. It also indicates how far offset the fiber will be for recommended combinations of top and bottom inserts. Note that this outer diameter may be the fiber cladding, jacket, or buffer. If one side of the fiber is being discarded, it is preferable to clamp onto the cladding of this section except in special cases (such as non-circular fiber) where the coating or buffer may be preferable. Sections of fiber that are not being discarded should always be clamped on the coating or buffer in order to avoid damaging the glass. This may require different sets of fiber holder inserts to be used in the left and right holding blocks. In this case, it is important to minimize the difference in the offsets introduced by the left and right sets of inserts when attempting to produce high-quality splices.

Each V-groove can accommodate a range of fiber sizes.
Legend | ||
---|---|---|
|
Best Fit | |
|
Second Best Fit: Try these options if the best fit does not incorporate your fiber sizes. | |
|
Third Best Fit: Try these options if the other two categories do not incorporate your fiber sizes. |
Fiber Holder Insert Selection Chart
- First, select the bottom insert that matches your fiber size most closely.
Example: For a Ø800 µm fiber, the VHF750 insert is the closest match, since it is only 50 µm smaller. - On the chart below, look to the right of your chosen bottom insert. Select a compatible top insert based on the accepted diameter size range shown in each cell.
Example: For the Ø800 µm example fiber from step 1, the green cell is in the 750 µm groove column for the VHA05 top insert, which has two grooves. The numbers listed in the green cell indicate that this combination of inserts is good for fibers from 728 to 963 µm in diameter. Our Ø800 µm fiber is within this range, so this is a good choice. There are several other options as well that will accommodate a Ø800 µm fiber as well, but the green shading in the chart indicates that the 750 µm groove in the VHA05 provides the best fit. - The second line of numbers in each cell shows the range of offsets that can be expected for any given combination of top and bottom inserts. When selecting inserts for the right and left fiber holding blocks, try to minimize the offsets between the pairs of inserts on each side.
Example: If we choose a VHF750 bottom insert and the Ø750 µm groove in the VHA05 top insert, we can use fiber as small as 728 µm, in which case the center of the fiber would sit 23 µm below the surface of the bottom insert. We could also clamp a fiber as large as 963 µm, in which case the center of the fiber would sit 213 µm above the surface of the bottom insert. We could interpolate to find the offset experienced by our hypothetical 800 µm fiber, but it turns out that in a 60° V-groove, the offset is equal to the outer diameter difference. So in our example, that means that the center of our fiber is going to sit 50 µm above the bottom insert surface, since it is 50 µm larger than the fiber that the bottom insert was designed for (800 - 750 = 50). - Holding blocks designed for fibers less than Ø1000 µm have vacuum holes, designed to aid in aligning small fiber within the groove, while bottom inserts for fibers of Ø1000 µm or larger do not have these holes. The glass processors have a vacuum pump that provides a small holding force via these holes, keeping small fibers in place as the clamps are lowered. Inserts with vacuum holes are indicated by a superscript "d" in the table below.
Top Insert Item # | VHA00a VHB00b |
VHA00a | VHA05c VHB05b |
VHA10c | VHA15c | VHA20c | VHA25 | VHA30 | |||||
---|---|---|---|---|---|---|---|---|---|---|---|---|---|
Accepted Diameter (Nominal) | ≤320 µm | 400 µm | 500 µm | 750 µm | 1000 µm | 1250 µm | 1500 µm | 1750 µm | 2000 µm | 2250 µm | 2500 µm | 3000 µm | |
Bottom Insert Item # |
Accepted Diameter (Nominal) |
Min / Max Accepted Diameter (µm) Min / Max Fiber Offset (µm) |
|||||||||||
VHF160d,e | 160 µm | 112 / 208 -49 / 48 |
- | - | - | - | - | - | - | - | - | - | - |
VHF250d,e |
250 µm | 177 / 320 -73 / 69 |
275 / 323 23 / 74 |
- | - | - | - | - | - | - | - | - | - |
VHF400d,e |
400 µm | 279 / 519 -122 / 119 |
377 / 517 -23 / 117 |
410 / 519 -9 / 119 |
- | - | - | - | - | - | - | - | - |
VHF500d,e |
500 µm | 346 / 592 -153 / 93 |
447 / 647 -53 / 147 |
476 / 711 -24 / 211 |
560 / 795 61 / 296 |
- | - | - | - | - | - | - | - |
VHF750d,e |
750 µm | 516 / 759 -234 / 9 |
617 / 970 -132 / 221 |
643 / 878 -107 / 128 |
728 / 963 -23 / 213 |
812 / 1047 62 / 297 |
- | - | - | - | - | - | - |
VHE10c | 1000 µm | - | - | 773 / 1008 -172 / 63 |
858 / 1093 -88 / 147 |
943 / 1178 -3 / 232 |
1036 / 1271 90 / 325 |
- | - | - | - | - | - |
1250 µm | - | - | - | 1034 / 1269 -176 / 59 |
1119 / 1354 -91 / 144 |
1212 / 1447 2 / 237 |
1288 / 1523 78 / 313 |
- | - | - | - | - | |
VHE15c | 1500 µm | - | - | - | - | 1280 / 1515 -172 / 63 |
1373 / 1608 -79 / 156 |
1449 / 1684 -2 / 233 |
1534 / 1769 82 / 314 |
- | - | - | - |
1750 µm | - | - | - | - | - | 1534 / 1770 -159 / 76 |
1611 / 1846 -83 / 152 |
1695 / 1930 2 / 237 |
1772 / 2007 78 / 313 |
- | - | - | |
VHE20c | 2000 µm | - | - | - | - | - | - | 1787 / 2022 -171 / 64 |
1871 / 2106 -86 / 149 |
1947 / 2183 -10 / 225 |
2032 / 2267 74 / 309 |
- | - |
2250 µm | - | - | - | - | - | - | - | 2033 / 2268 -167 / 68 |
2109 / 2344 -91 / 144 |
2193 / 2429 -6 / 229 |
2278 / 2513 78 / 313 |
- | |
VHE25 | 2500 µm | - | - | - | - | - | - | - | - | 2270 / 2505 -172 / 64 |
2355 / 2590 -87 / 148 |
2439 / 2675 -2 / 233 |
2609 / 2844 167 / 402 |
VHE30 | 3000 µm | - | - | - | - | - | - | - | - | - | 2692 / 2944 -256 / -4 |
2777 / 3029 -171 / 81 |
2946 / 3198 -2 / 250 |
Fiber Holder Insert Assembly and Installation
After you select the correct fiber inserts for your nominal fiber diameter, the fiber inserts need to be installed into the fiber holding blocks, as shown in the video below to the left. Standard fiber inserts are meant to remain installed in a system when processing fibers of the same size, while fiber transfer inserts are used to move a fiber from one compatible Vytran machine to another between processing steps. Transfer inserts consist of a fiber holder bottom insert, fiber transfer clamp, and graphite V-groove that require assembly as shown in the video below to the right.
An Overview of the FFS3 Software Main Toolbar
Each glass processor and splicer is shipped with a monitor and a PC pre-installed with our FFS3 software, which is used to operate each system. This software package allows users to control all parameters of the set-up, fusion, and tapering. Each step can be initiated by the user through the graphical user interface (GUI) or through one-button splice process files that run automated routines.
Common splicing and tapering routines, including those listed below, come preinstalled on the system. The GUI and splice library software enable users to create their own splice files for new processes or to customize existing files as necessary. Additionally, an add-on software package is available that includes application files for specialized applications that can be purchased separately below. Please contact Tech Support for inquiries regarding your specific application.
The video to the right highlights some of the main features of the software and the sections below describe some of the fiber splicing and tapering parameters that can be programmed through the software GUI.
Included Splice Files
- FTAV2 (V2) Filament Burn-In and Normalization
- Ø125 µm Single Mode Fiber Splice
- Ø125 µm Polarization-Maintaining Fiber Splice
- FTAV4 (V4) Filament Burn-In and Normalization
- Ø400 µm Fiber Splice
- Ø400 µm to Ø200 µm Taper

Click to Enlarge
Figure 4. Multi-Stage Splicing Configuration

Click to Enlarge
Figure 5. Active X-Y Alignment Scan Properties
Multi-Stage Splicing
For special applications, the software can run several splice steps in a sequence. Users can independently set the splice parameters for each step, as shown in Figure 4. Alternatively, multiple independent splice files from the user's library can be executed in order. The system will then perform a complex splicing function according to the sequence of the selected splice files.
Active Alignment
The active alignment method is typically used for fiber that has a high core eccentricity. In this case, standard imaging methods cannot always ensure proper alignment of the fiber cores. Instead, the cores are aligned using the output from an optical power meter as feedback to maximize the power transmission between the two fibers. This is done by scanning one fiber across the other with a given scan step size and taking a power meter reading at each position. At the end of the scan, the fiber is moved back to the position at which the optical power was either maximized or minimized. Parameters for this scan, such as step size and fiber offset position, can be set within the software to ensure accurate alignment, as shown in Figure 5.
Thorlabs' Vytran® Optical Fiber Glass Processors are versatile, fully integrated glass processing and fiber splicing platforms for fabricating splices, tapers, and custom terminations with high precision and low loss. Featuring a comprehensive applications library, these processes can be performed for many different fiber sizes and types. Examples of a few fiber splicing/processing applications are listed in the sections below and highlighted in the video to the right.

Click to Enlarge
Two fibers with dissimilar cores before and after splicing. The dissimilar cores are clearly visible before the cores are thermally expanded.
Filament Fusion
Fusion Splicing is a process of joining two optical fibers end-to-end using heat. The goal is to fuse the two fibers together in such a way that light passing through the fibers is not scattered or reflected by the splice while ensuring that the splice and the region surrounding it should be almost as strong as the original fiber. The glass processors use a resistive graphite or iridium filament shaped like an upside-down omega to provide the heat necessary for fusion.
Once the two fibers to be spliced are aligned, the splice head is repositioned so that the filament is centered under the fiber ends. Power is then applied to the filament to raise its temperature to a level hot enough to fuse the fibers together, typically about 3000 °C. Because the filament would oxidize if it were brought to such a high temperature in air, high-purity argon gas is used to purge the splicing chamber of oxygen during the filament fusion process. In order to keep the fibers clean and improve splice strength, the purging gas (not available from Thorlabs) is set to flow over the fibers at a high rate during the fusion process.
Mode Adapters and NA Converters
In many applications, large-mode-area gain fibers may need to be coupled to fibers with a non-matching mode field diameter or NA. Glass processors can help optimize coupling between dissimilar fibers by altering the mode field diameter or NA of one fiber to match the other. This is accomplished by applying heat prior to splicing and/or to physically taper the fibers to change the core diameter. In the example shown to the right, two fibers (single mode fiber and Ø20 µm large-mode-area fiber) have dissimilar core sizes. In the lower image, the small cored fiber has been thermally expanded by diffusing the core dopants and then spliced together.
Fiber Processing Applications

Click to Enlarge
Ø20 µm core, Ø400 µm cladding large-mode-area (LMA) fiber tapered to Ø125 µm cladding.
Tapering and Drawing
All Vytran glass processor configurations are capable of tapering (altering the cross-sectional diameter) or drawing out (increasing the length) of a fiber. This is accomplished by using the filament furnace to heat the fiber to its softening point and then applying a tensile force to elongate the fiber, reducing the cross section of the fiber. The fiber holders provide up to 180 mm of z-axis travel, enabling the fabrication of long tapers up to 150 mm in length. This process can be programmed through the GUI by entering the physical characteristics of the desired taper into a taper interface menu (see the Software tab for details). The software GUI also includes a tension monitor and control function, which can accurately monitor drawing conditions during tapering.
Fiber Terminations
These glass processing systems, which have an integrated platform that combines precise fiber positioning, control over the filament fusion process, and long tapering/drawing lengths, are ideal for adding or fabricating complex terminations to the ends of bare fibers. Examples of developed terminations include ball lenses, fiber catheters, and fiber probes.
End caps are large-core-diameter, short-length fibers used to diffuse the beam intensity of high-power fibers to prevent damage to fiber end faces. Glass processors are well suited for fusing large-core-silica end caps to the ends of power beam delivery fibers. We recommend using an LDC401 or LDC401A Fiber Cleaver to fabricate end caps with precise lengths.
Couplers and Combiners
Glass processors can fuse fibers side-by-side or into bundle configurations; this process is critical for fabricating fused fiber couplers and pump or output combiners. Through precise control of heating and tapering conditions and using multi-fiber holding block inserts, the operator is able to develop application-specific coupler and combiner solutions that feature very low loss.

Click to Enlarge
Two single mode fibers tapered and fused together for 50/50 coupling in a glass processor. Spacing between the fiber cores is approximately 15 to 20 µm.
![]() Product DemonstrationsThorlabs has demonstration facilitates for the Vytran® fiber glass processing systems offered on this page within our Morganville, New Jersey and Shanghai, China offices. We invite you to schedule a visit to see these products in operation and to discuss the various options with a fiber processing specialist. Please schedule a demonstration at one of our locations below by contacting technical support. We welcome the opportunity for personal interaction during your visit! Thorlabs China
|
Tutorial Videos
To assist new or returning GPX users with operating their glass processors, we have created a series of tutorials aimed at teaching the basic skills needed to run this machine including filament maintenance and splicing fibers. In order to be able to read the text in the videos, we strongly recommend viewing these videos at full screen, 1080p resolution. If you require assistance performing other operations using your GPX glass processor or you have suggestions on future videos in the series, please contact us at techsupport@thorlabs.com.
Vytran® Optical Fiber Glass Processor Selection Guide | ||||||
---|---|---|---|---|---|---|
Item # | GPX3400 | GPX3600 | GPX3800 | GPX3850 | GPX4000LZ | |
Fiber Cladding Diameter | 80 µm to 1000 µm | ![]() |
![]() |
![]() |
![]() |
- |
Up to 1.25 mm | ![]() |
![]() |
![]() |
![]() |
- | |
Up to 1.7 mm | - | ![]() |
- | ![]() |
![]() |
|
250 µm to 2 mm | - | - | - | - | ![]() |
|
250 µm to 5 mm | - | - | - | - | ![]() |
|
Fiber Type | Multimode | ![]() |
![]() |
![]() |
![]() |
![]() |
Single Mode | ![]() |
![]() |
![]() |
![]() |
![]() |
|
Double Clad | ![]() |
![]() |
![]() |
![]() |
![]() |
|
Polarization Maintaining | ![]() |
![]() |
![]() |
![]() |
![]() |
|
Automated Measurement and Alignment | ![]() |
![]() |
![]() |
![]() |
![]() |
|
End-View Illumination and Imagingb | ![]() |
![]() |
![]() |
![]() |
![]() |
|
Tension Monitor and Control System | ![]() |
![]() |
![]() |
![]() |
![]() |
|
Integrated Fiber Cleaver | - | - | ![]() |
![]() |
- | |
Real-Time Hot Image Monitoring | - | - | ![]() |
![]() |
![]() |
|
Liquid Cooling System | Optional Add-On | ![]() |
Optional Add-On | ![]() |
Optional Add-On | |
Fused Taper Software Enhancement and Handling Fixtures | Optional Add-On | - | ||||
Fiber Combiner Loading Fixture | Optional Add-On | - |
Posted Comments: | |
christophe.pierre
 (posted 2019-02-22 08:19:06.53) Hello,
He have issues with FRAV1 filament.
The normalisation programs are pushing this filament to work at up to 15 or 20W. We put down this power down to 10W to be safe but we burn them. we try to work at 5W and increment the power up to 9W, and at 9W, the filaments burn.
We burn 2 filament this way. And even at 8W, we cannot use them to normalize or splice silica fibers.
We do not have issues with argon.
Can you repair/exchange this 2 filaments ?
Is that a normal behavior ?
Regards,
Christophe PIERRE nbayconich
 (posted 2019-02-27 02:25:04.0) Thank you for contacting Thorlabs. This is not normal behavior for these devices. Yes we can refurbish these filaments.
We will need to know more about the settings of your workstation. A techsupport representative will reach out to you directly to help troubleshoot the issue you are seeing. |

Components Included
- Glass Processor Workstation with Built-In Cleaver and Hot Image Camera System
- FTAV4 Graphite Filament Assembly (Ø125 µm - Ø600 µm Cladding) Pre-Installed (Additional Filaments Sold Below)
- Computer with Monitor, Keyboard, and Mouse
- Software Interface with Example Splice Files
- Vacuum Pump for Fiber Holder Bottom Inserts
- Power Supply (See Specs Tab for Details)
- Regulator for Argon Gas Tank with CGA-580 and DIN 477 Number 6 Connectors
- 1/8" PTFE Tube for Argon Gas
- 9-Pin D-Sub RS-232 Communication Cable
- 6-Pin IEEE-1394 Fire Wire Camera Cable
- Tool Kit with Hex Keys for Filament/Insert Replacement
- Liquid Cooling System (Included with GPX3850)
Required Purchases
- Fiber Holder Top Inserts (Two Required)
- Fiber Holder Bottom Inserts (Two Required for Single Fiber Processing)
- Transfer Clamp and Graphite V-Grooves (Required for Transfer Inserts)
- Multi-Fiber Holder Bottom Inserts (Two Required for Making Couplers or Combiners)
- >99.999% Purity Argon Gas Tank (Not Available from Thorlabs)
Optional Purchases
- Fluorine-Doped Capillary Tubes (For Making Specialty Couplers or Combiners)
- Additional Filament Assemblies
- Liquid Cooling System (Optional Add-On for GPX3800)
- Fiber Taper Software Add-On and Handling Fixtures
- Fiber Combiner Loading Fixture
- Ultrasonic Cleaner
- Mountable Gooseneck Light
- Replacement SS2SN013 Setscrews for Fiber Holding Blocks
- Glass Processor Workstation and Computer with Control Software
- Splice/Taper Optical Fibers Up to Ø1.25 mm (GPX3800) or Ø1.7 mm (GPX3850)
- Diamond Cleave Blade Integrated into Splice Head
- Integrated ND Filters in Camera System for Real-Time Splice/Taper Imaging
- Automatic XY and Rotational Alignment
- Ideal for Single Mode, Multimode, Polarization-Maintaining, and Specialty Fibers
- Fiber Z-Axis Travel of 180 mm
These Vytran Glass Processor Workstations feature automatic XY and rotational alignment of the fiber and a diamond cleave blade that is integrated into the splice head. This combined functionality enables users to perform multiple operations on the same fiber without realigning the position and rotation of the fiber after each process step. Additionally, the camera system is equipped with ND filters that allow the user to view the fiber edges in real time while the filament is hot, providing fast feedback on splice/taper quality. The GPX3800 and GPX3850 can splice or taper fibers with outer diameters up to 1.25 mm or 1.7 mm, respectively.
The precision fiber handlers can position a fiber in XY with a resolution of 0.25 µm and rotate a fiber up to 200° with a resolution of 0.02°. Cleaving, splicing, and tapering processes are controlled automatically through the included software GUI. The included fiber holders can translate up to 180 mm along the fiber axis, allowing the filament to heat large portions of the input fiber(s). This extended heating range is ideal for many applications including thermally diffusing core dopants to achieve low-loss splices between highly dissimilar fibers or for fabricating long adiabatic fiber tapers. The fiber holding blocks can also pull vacuum through fiber holder inserts with vacuum holes to help secure the fiber within the insert.
The workstation includes the fiber holders, furnace assembly, CCD camera with ND filters for hot imaging, PC and monitor pre-installed with the control software, and mirror tower for side- and end-view imaging. Each processor workstation is fitted with a high-purity PTFE gas line and a gas regulator equipped with a CGA-580 output port; a DIN 477 Number 6 output port connector is also included. An FTAV4 Graphite Filament Assembly (for Ø125 µm - Ø600 µm Cladding) comes pre-installed in the system; additional graphite or iridum filaments are sold separately below. Top and bottom inserts for the fiber holders, both of which are required to operate the glass processor workstation, can also be purchased separately below. Nylon-tipped setscrews are used to secure the inserts in the fiber holding blocks; replacement 2-56, 1/8" long SS2SN013 setscrews are available in packs of 10.
Installation and training by one of our application engineers is recommended for this system; please contact Tech Support for more details.

Item # | Filament Material |
Cladding Diameter (Min/Max) |
Applicationa | LFS4100 Compatible |
---|---|---|---|---|
FTAV2 | Graphite | 80 µm / 250 µm | Splice | Yes |
FTAV4 | 125 µm / 600 µm | |||
FTAV5 | 250 µm / 1000 µm | |||
FTAV6 | 400 µm / 1300 µm | |||
FTAT3 | 250 µm / 1500 µm | Taper | No | |
FTAT4 | 400 µm / 1800 µm | |||
FRAV1 | Iridium | ≤200 µm | Splice | Yes |
FRAV3 | ≤400 µm | |||
FRAV5 | 250 µm / 1050 µm |
- Graphite and Iridium Filament Assemblies for Automated Glass Processors
- Assembly Includes Filament Element and Protective Shroud
- Optimized for Splicing or Tapering Applications (See Table to the Right for Details)
- Splicing Filaments Compatible with LFS4100 Splicing System
Filament Assemblies contain a graphite or iridium omega-shaped resistive heater element encased within a protective shroud. The filaments sold here are compatible with the automated glass processors; those indicated in the table to the right as splice filaments are also compatible with the LFS4100 Splicing System.
A selection of six graphite and three iridium filament assemblies for fibers with claddings up to Ø1800 µm are available. Graphite filaments are capable of achieving the high temperatures necessary for splicing or tapering large-diameter fibers while outgassing less than filaments made from other metals. Alternatively, iridium filaments heat fibers at slightly lower temperatures than graphite filaments, making these ideal for working with soft glass fibers. Although the heating time of a filament is approximately 40 minutes, this can vary depending on a number of factors including argon quality, splice/taper duration, and fiber glass quality.
Filaments are optimized for splicing or tapering applications; this is not restrictive, however, as splice filaments can be used for tapering. Splice filaments have an opening in the top of the assembly body, while tapering filaments are closed off at the top to minimize exposure to contaminants. Different filament bodies are distinguished by the version number (e.g., V4, V6, T3) engraved on the assembly body.
Before a new filament can be used in a system, it must be burned in. During the burn-in process, the filament is cycled between its operating temperature and room temperature several times. This stabilizes the thermal properties of the filament so that it produces a more consistent power output and heating performance when current is passed through it. This procedure only needs to be performed once, after which the filament will only need regular normalization. Visit the Tutorial Videos tab above to see videos on how to perform filament maintenance and simple splices. If filament performance begins to degrade, filament refurbishments can be ordered by contacting Tech Support.

Item # | Side 1 Accepted Diameter (Min/Max) |
Side 2 Accepted Diameter (Min/Max) |
---|---|---|
VHB00a | 57 µm / 759 µmb | N/A |
VHB05a | 410 µm / 1008 µm | 560 µm / 1269 µm |
VHA00 | 57 µm / 759 µmb | 275 µm / 970 µm |
VHA05 | 410 µm / 1008 µm | 560 µm / 1269 µm |
VHA10 | 812 µm / 1515 µm | 1036 µm / 1770 µm |
VHA15 | 1288 µm / 2022 µm | 1534 µm / 2268 µm |
VHA20 | 1772 µm / 2505 µm | 2032 µm / 2944 µm |
VHA25 | 2278 µm / 3029 µm | N/A |
VHA30 | 2609 µm / 3198 µm | N/A |
- Top Inserts for Fiber Holding Blocks
- Accepts Fiber Outer Diameter (Cladding/Coating) from 57 µm to 3.198 mm (See the Fiber Holder Inserts Tab for Information on Choosing Inserts)
- Single-Sided and Dual-Sided Inserts Available (See Table to the Right for Details)
- VHBxx End-View Illumination Insert Available for Automated Glass Processors and Splicing Systems
- Compatible with Automated Glass Processors, LDC401 Series Fiber Cleavers, FPS300 Stripping and Cleaning Station, and LFS4100 Splicing System
Fiber Holder Inserts, which consist of one top insert and either a bottom or transfer insert, are placed in the fiber holding blocks of the optical glass processor to secure the fiber during splicing or tapering. The inserts clamp the cladding, buffer, or coating of the fiber and can accommodate outer diameters of up to 3.198 mm. The Fiber Holder Inserts tab above includes information to aid in selecting and installing the correct combinations of top and bottom inserts to accommodate different fiber diameters.
Two types of top inserts are compatible with the automated glass processors. The VHA standard top inserts come in single-sided and dual-sided versions. These standard inserts can also be used in the LDC401 Series of Fiber Cleavers, FPS300 Stripping and Cleaning Station, and LFS4100 Splicing System. The VHB00 and VHB05 top inserts (shown to the left) feature an indent for LED illumination from the automated glass processor workstations and are necessary for end-view imaging and alignment of the cores of polarization-maintaining and microstructured specialty fibers.

Standard and Transfer Inserts | ||||
---|---|---|---|---|
Item # | Type | Side 1 Accepted Diameter (Min/Max) |
Side 2 Accepted Diameter (Min/Max) |
Vacuum Holes |
VHF160 | Transfer | 112 µm / 208 µm | N/A | Yes |
VHF250 | Transfer | 177 µm / 320 µm | N/A | Yes |
VHF400 | Transfer | 279 µm / 519 µm | N/A | Yes |
VHF500 | Transfer | 346 µm / 795 µm | N/A | Yes |
VHF750 | Transfer | 516 µm / 1047 µm | N/A | Yes |
VHE10 | Standard | 773 µm / 1271 µm | 1034 µm / 1523 µm | No |
VHE15 | Standard | 1280 µm / 1769 µm | 1534 µm / 2007 µm | No |
VHE20 | Standard | 1787 µm / 2267 µm | 2033 µm / 2513 µm | No |
VHE25 | Standard | 2270 µm / 2844 µm | N/A | No |
VHE30 | Standard | 2692 µm / 3198 µm | N/A | No |
- Bottom Fiber Inserts with V-Grooves for Fiber Holding Blocks
- Compatible with Cladding/Coating Diameters from 112 µm to 3.198 mm (See the Fiber Holder Inserts Tab for Information on Choosing Standard or Transfer Inserts)
- Transfer Inserts for Moving Fiber Between Vytran Systems
- Inserts with Vacuum Holes for Aligning Smaller Fibers (<Ø1047 µm) in V-Groove
Fiber Holder Inserts, which consist of one top insert and a bottom insert, are placed in the fiber holding blocks of the optical glass processor to secure the fiber during splicing or tapering. Bottom inserts are magnetically held within the fiber holding blocks of the glass processors and other compatible systems. The V-groove machined into the bottom inserts ensures the fiber is centered within the fiber holder; inserts with different V-groove sizes are available. Vacuum holes at the bottom of the transfer inserts are used for holding and aligning small fibers within the V-groove. The Fiber Holder Inserts tab above includes information to aid in selecting and installing the correct combinations of top and bottom inserts to accommodate different fiber diameters.
Three types of bottom inserts are compatible with the glass processors: transfer bottom inserts, standard bottom inserts, and multi-fiber bottom inserts (sold further below). Transfer bottom inserts (indicated with item #s starting with VHF) allow for a single fiber to be transferred between the LDC401 Series of Fiber Cleavers, FPS300 Stripping and Cleaning Station, and LFS4100 Splicing System with minimal loss of alignment. For example, a fiber can be placed in a transfer insert and cleaved using the LDC401 cleaver, then the entire transfer insert can be placed in the LFS4100 Splicing System for splicing. This process works because the transfer inserts are precisely located within each Vytran system, and the VHT1 Magnetic Lid (sold directly below) prevents axial movement of the fiber during transport. Transfer inserts are equipped with vacuum holes that provide a small suction force to hold the fiber in place. All of these transfer inserts require the VHT1 Transfer Clamp (sold below); transfer inserts for fiber outer diameters ≤550 µm also require a Graphite V-Groove (sold below).
Standard Fiber Holder Bottom Inserts (indicated by item #s starting with VHE) can be used with large-diameter fibers. These inserts come in single-sided and dual-sided versions. The standard bottom inserts can also be used in the LDC401 Series of Fiber Cleavers, FPS300 Stripping and Cleaning Station, and LFS4100 Splicing System. Unlike transfer inserts, alignment of the fibers will not be maintained when these inserts are transferred between systems.

Graphite V-Grooves | ||
---|---|---|
Item # | Accepted Diameter (Min / Max) |
Groove Length |
VHG125 | 80 µm / 125 µm | 0.313" |
VHG125L | 80 µm / 125 µm | 0.594" |
VHG200 | 150 µm / 200 µm | 0.313" |
VHG250 | 200 µm / 250 µm | 0.313" |
VHG300 | 250 µm / 300 µm | 0.313" |
VHG350 | 300 µm / 350 µm | 0.313" |
VHG400 | 350 µm / 400 µm | 0.313" |
VHG450 | 400 µm / 450 µm | 0.313" |
VHG500 | 450 µm / 500 µm | 0.313" |
VHG550 | 500 µm / 550 µm | 0.313" |
- Clamp and Graphite V-Grooves Used with Transfer Bottom Inserts to Move Fiber Between Vytran Systems
- One VHT1 Transfer Clamp Required with Transfer Bottom Inserts
- Graphite V-Groove for Supporting Smaller Fibers from Ø125 µm to Ø550 µm During Splicing
- Transfer Clamps are Compatible with GPX Fiber Processors, LDC401 Series of Fiber Cleavers, FPS300 Stripping and Cleaning Station, and LFS4100 Splicing System
These Transfer Clamps and V-Grooves are used with the VHF Transfer Bottom Inserts sold directly above to move a single fiber between various Vytran systems with minimal loss of alignment. For example, a fiber can be placed in a transfer insert and cleaved using the LDC401 Fiber Cleaver. Then, the entire transfer insert and fiber can be moved to a glass processor for splicing.
The VHT1 clamp is equipped with a magnetic lid that secures transfer inserts and prevents axial movement of the fiber. It can also be used to hold the insert during transport without touching the fiber itself. For fibers with diameters ≤550 µm, a graphite V-groove must be purchased to support the fiber when splicing (please see the size table to the right for more information). The graphite V-grooves are secured by tightening the two setscrews in the transfer insert. For information on how to assemble transfer inserts, see the Fiber Holder Inserts tab.

Multi-Fiber Inserts | |||
---|---|---|---|
Item # | Type (Click for Drawing) |
Accepted Diameters | Recommended Top Inserta |
VHD125S | Side-by-Side | 125 µm / 125 µm | VHA00 |
VHD250S | Side-by-Side | 250 µm / 250 µm | |
VHD320S | Side-by-Side | 320 µm / 320 µm | |
VHD250V | Double-V Slot | 250 µm / 250 µm | |
VHD320V | Double-V Slot | 320 µm / 320 µm | |
VHD320P | Double-V Slot w/ Pins | 320 µm / 320 µm | |
VHS250250 | Triple-V Slot | 250 µm / 250 µm / 250 µm | |
VHS250400 | Triple-V Slot | 250 µm / 400 µm / 250 µm | |
VHS250500 | Triple-V Slot | 250 µm / 500 µm / 250 µm | |
VHS300350 | Triple-V Slot | 300 µm / 350 µm / 300 µm | |
VHS320400 | Triple-V Slot | 300 µm / 400 µm / 300 µm | |
VHS320550 | Triple-V Slot | 320 µm / 550 µm / 320 µm | VHA05 |

Click to Enlarge
The VHD320P features adjustment pins that are used to bring two fibers into very close proximity for splicing.
- Bottom Inserts with Grooves for Holding Multiple Fibers
- Used When Creating Fused Couplers or Combiners
- Vacuum Holes for Aligning Fibers in V-Grooves or Slots
- Multiple Insert Types Available (See Table for Options)
Multi-Fiber Inserts are designed for applications requiring two or three fibers to be tapered and fused together, such as when making wavelength division multiplexers, fused fiber couplers, or power combiners.
Side-by-side inserts have a U-shaped groove for holding two fibers tightly together in parallel. Double-V-slot inserts feature two parallel V-grooves on the same side of the insert that each hold a single fiber. The VHD320P insert additionally features offset adjustment pins that are used to bring the two fibers in close contact during splicing (see photo to the left). Triple-V-slot inserts have a V-groove in the middle and two V-grooves adjacent on both sides that alllow a signal fiber to be fused with two pump fibers.
These bottom inserts are magnetically held within the fiber holding blocks of the glass processors and other compatible systems. The grooves machined into the inserts ensure the fiber is centered within the fiber holder. Vacuum holes at the bottom of the transfer inserts are used for holding and aligning small fibers within the V-groove. Recommended top inserts for each multi-fiber insert are indicated in the table to the right. Alignment of the fibers will not be maintained when these inserts are transferred between systems.

Compatible Systems
- CAC400 and CAC400A Fiber Cleavers
- LDC401 and LDC401A Fiber Cleavers
- LDC450B Portable Fiber Cleaver
- GPX3800 and GPX3850 Automated Glass Processors with Cleavers
- FFS2000 and FFS2000PT Fiber Preparation and Splicing Workstations
- FFS2000PM and FFS2000WS Fiber Preparation, Splicing,
and Proof Testing Workstations - Former Generation LDC-200 Fiber Cleaver
- Replacement Blade for Our Fiber Cleaving Systems (See List to the Right)
- 0.08" (2.0 mm) Long Diamond Blade
- User Installable

Click to Enlarge
The blade is shipped in a protective covering.
The ACL83 Diamond Cleave Blade is a replacement blade for the Vytran fiber processing systems listed to the right. Each system is shipped with a blade included.
When used with proper cleave parameters, a single location on the blade can provide up to 5,000 cleaves (dependent on the cladding properties of the fiber being cleaved). The blade can be positioned approximately 10 times before replacement (assuming proper cleave parameters and usage that does not cause unexpected damage to the blade). Blade replacement instructions for each system are provided in the user manuals.
Note: Severe damage to the blade can occur if conditions cause high stress perpendicular to the edge of the blade or if incorrect parameters are used to cleave the fiber.


Click to Enlarge
End-view image of 3:1 combiner made using a capillary tube.
Capillary Tube Dimensions | |||
---|---|---|---|
Item # | Inner Diameter | Outer Diameter | Length |
FTB02 | 750 ± 100 µm | 1500 ± 100 µm | 170.0 ± 3 mm |
FTB03 | 800 ± 40 µm | 1100 ± 55 µm | |
FTB01 | 1200 ± 60 µm | 1450 ± 75 µm |
- Capillary Tube for Manufacturing Fiber Combiners
- Three Diameter Combinations Available, 170 mm Long
- Compatible with GPX3400, GPX3600, GPX3800, and GPX3850 Processors
Fluorine-doped silica capillary tubes are ideal for the manufacture of high-power fiber laser combiners and other specialty applications. During this process, the fibers that will be joined are inserted into the capillary tube, then the tube is fused and tapered down into a solid glass element. With a core consisting of the fused fibers and a cladding formed by the low-index capillary tube, the tapered element acts as a multimode waveguide, with the capillary tube serving to contain the light in the combiner.
Please make sure to use gloves when handling these fluorine-doped tubes.

Liquid Cooling System Specifications | |
---|---|
Cooling Capacity | 590 Wa |
Coolant Pump Flow Rate | 10 Speed Levels up to 4 L/min |
Reservoir Capacity | 157 mL (5.3 fl oz) |
Radiator | Aluminum; 2 x 120 mm Fans |
Power Consumption | 20 W (Max) |
Power Supply | 12 VDC (via Molex Connector) 110/120 VAC with Power Adapter |
Weight | 8.00 lbs (3.63 kg) |
- Included with GPX3850 Glass Processor Workstation
- Optional Add-On for GPX3800 Glass Processor Workstation
- Liquid Cooling System for Vytran Glass Processors and Splicing Systems
- Prevents Furnace Overheating During Extended Heating Operation (e.g., Tapering)
- Includes 700 mL (24 fl oz) of High-Performance Liquid Coolant
The GPXWCS Liquid Cooling System is an optional add-on for our Vytran Glass Processors that helps keep the furnace assembly cooled during extended heating operations. It is highly recommended for customers interested in fiber tapering, mode adapter, or fiber termination applications. This cooling system is also compatible with the LFS4100 Splicing System but is not necessary for standard splicing processes.
The GPXWCS has a 157 mL reservoir to cycle high-performance liquid coolant (700 mL bottle of coolant included) at flow rates of up to 4 L/min with a cooling capacity of 590 W at 25 °C ambient temperature; click here for a MSDS safety sheet. Tubing and fittings for connecting to a Vytran Glass Processor are included. The cooling system can be powered either through a 12 VDC Molex Connector (via the included computer slot adapter) or externally using the included 110/120 VAC power adapter.

- Software Enhancement Enabling Active Fused Biconic Taper (FBT) Processing
- Fixture with Adjustable Fiber Gripper for Transporting Fiber Tapers and Couplers to a Packaging Station
- Fixture with Removable Fiber Holder for In Situ Packaging of Fiber Tapers and Couplers
These optional add-ons for the Vytran Glass Processors are designed to aid microtaper and fused fiber coupler processing. The software and fixture add-ons can be purchased separately or together in a kit. The GPXFBT-SFT software package enables finer control over heating and fiber pulling parameters during active FBT processes, resulting in improved yields and high repeatability between runs.
Two fixture add-ons are also available. The GPXFBT-FXTA Adjustable Taper Fiber Gripper fixture provides a stable base for your specific length component, allowing transfer to a packaging station. The fiber gripper can be adjusted to accommodate taper lengths from 0 - 3.15" (0 - 80 mm). The GPXFBT-FXTB Removable Taper Holder Fiber Fixture option acts as a pick-up and removal apparatus for the user to safely and securely transport the fabricated taper or coupler for secondary processing or in situ packaging. The stages included with these fixtures have an x-axis and y-axis travel of 1" (25.4 mm) and a roll and yaw adjustment of ±2.5° and ±5°, respectively. When using the fixture add-ons with the GPX3800 and GPX3850, the cleave head needs to be removed before the fixtures can be installed.

Combiner Fixture Specifications | |
---|---|
Degrees of Freedom | Five (X, Y, Z, Pitch, Yaw) |
Y-Axis Travel (Coarse) | 300 mm |
X-Axis Travela | 0.44" (11.2 mm) |
Z-Axis Travela | 0.20" (5.1 mm) |
Platform Flatness | ±0.005" |
Platform Thickness | 6 mm |
Platform Material | Mic-6 Aluminum |
Bottom Insert (One Required) |
VHS, VHD, VHE, or VHF Series |

Click to Enlarge
The fiber holding block assembly translates along a rail for Y-axis positioning.
- Supports the Positioning of Fiber Bundles for Combiner Fabrication
- Five Degrees of Freedom: X, Y, Z, Pitch, Yaw
- 300 mm Coarse Travel Along Fiber Feed Axis
- Working Platform Folds Up 90° for Fiber Bundle Grouping
- Required Bottom Insert Sold Separately
- Contact Tech Support for Right Side Mounting Variant
The GPXCFXL Fiber Combiner Loading Fixture is an optional add-on for our GPX3000 Series Glass Processors that provides support and five-axis positioning of fiber bundles during manufacture of fiber combiners. The multi-axis assembly enables direct insertion of fiber bundles into fragile tapered capillary tubes. This reduces the risk of tube breakage by allowing controlled bundle insertion while the capillary tube is still in the glass processing station.
The bundle is placed in the bottom insert (sold separately above), which is mounted in the assembly's fiber holding block. XZ translation is provided by the integrated T12XZ stage, while the support assembly is attached to a rail for travel in the fiber feed direction. To aid with bundle alignment, coarse pitch and yaw adjustments are achieved through a lockable ball pivot mechanism; note that this mechanism also allows off-axis roll that is coupled with translation. The stage's travel along the rail (Y-axis) is also lockable.
The fixture mounts to the left side of processors and supports a wide variety of inserts to suit individual needs. The working platform features a double hinge to ensure a gapless working surface and folds up 90° with an air spring support and a pin lock at the vertical and horizontal positions. Please contact Tech Support to request a variant for mounting on the right side of a processor.


Click to Enlarge
USC2 Ultrasonic Cleaner and USC2NVT Nest for Vytran Transfer Bottom Inserts

Click to Enlarge
The cleaning intensity and duration controls are located on the rear of the cleaner.
USC2 Ultrasonic Cleaner Specifications | |
---|---|
Supported Fiber Diametera | 125 - 600 µm |
Tank Capacity | 100 mL |
Tank Dimensions | Ø1.7" x 2.8" Deep (Ø43 mm x 71 mm Deep) |
Cleaning Duration (Max Setting) |
>1 Minute |
Peak Output Frequency | 75.2 - 76.4 kHz |
Transducer Power (Max) | 6 W |
Operating Power | 36 W |
Operating Current | 1.5 A |
Input Voltageb | 100 - 240 VAC @ 47 - 63 Hz |
Overall Dimensionsa |
6.95" x 4.78" x 4.13" (176.5 mm x 121.5 mm x 104.8 mm) |
Mass | 1.28 kg (2.82 lbs) |

Click for Details The USC2NVT Nest adds support for Vytran transfer bottom inserts.
- Easy-to-Adjust Immersion Depth, Cleaning Duration, and Power Level
- Bare Fiber Nest with Magnetic Clamp Included
- Nest for Vytran Transfer Bottom Inserts Sold Separately (Item # USC2NVT)
- Compatible Solvents: Acetone or Isopropanol (Isopropyl Alcohol)
- Spout for Easy Fluid Disposal; Slotted Shield for Reduced Solvent Evaporation
Thorlabs' Vytran® USC2 Ultrasonic Fiber Cleaner is designed for volume processing of bare fiber. Adjustment knobs for cleaning intensity and cleaning duration allow the user to easily set repeatable cleaning parameters. The dunking jig offers adjustable immersion depth and is compatible with interchangeable fiber holder nests (each sold separately). A red LED indicates when the cleaning cycle is active. The 100 mL solvent tank is only suitable for use with acetone or isopropyl alcohol.
Tilting the dunking jig submerges the fiber in the tank and initiates the ultrasonic cleaning process. The ultrasonic agitation ceases after the chosen cleaning duration. The height of the fiber holder above the solvent tank can be changed over a 0.5" (12.7 mm) range using the knurled adjuster on the side of the dunking jig, visible in the photo above.
The knurled adjuster can also be reversed to disengage the bare fiber nest and switch it out for another fiber holder nest. Each cleaner is shipped with a bare fiber nest installed in the dunking jig. The USC2NVT Nest (sold separately) is designed for use with Vytran transfer bottom inserts. Accessories are available for the Vytran fiber nest to support a wider range of usage scenarios, including a clamp for standard bottom inserts and spacers for recessing inserts farther from the solvent tank. We also offer nests for Fujikura® and Fitel® fiber holders (each sold separately). Please see the complete product presentation for more information.

GPXL1 Gooseneck Light Specifications | |
---|---|
Lamp Electrical Power | 1 W |
Color Rendering Index (CRI) | 80 |
Lamp Lifetime | 30 000 h |
Lamp Luminous Flux | 100 lm |
Lamp Luminous Efficiency | 80 lm/W |
Operating Temperature | -25 to 45 °C |
Light Color | Neutral White |
Input Voltage | 12 VDC |

Click to Enlarge
The GPXL1 can be attached on either the right or left side of the glass processor workstation
- Attaches to Either Side of Workstation
- Illuminate Fiber Ends or Light General Work Area
- 12 VDC Power Supply (Sold Separately) Includes Region-Specific Power Cord
The GPXL1 Gooseneck Light is a lamp that can be used to couple light into a fiber combiner for end-view illumination or for general lighting of the workstation during alignment. The lamp features an on/off switch and a dimmer knob to control brightness. The flexible neck allows the lamp head to be easily positioned near a fiber or furnace.
Mount the GPXL1 on either side of the workstation using the mounting holes on the workstation (as seen in the image to the right). Two 10-32 mounting screws and a 5/32" hex key are included.
Users must also purchase a GPXL1PS 12 VDC Power Supply along with the GPXL1. The power supply includes a region-specific power cord which must be used with an 85 - 265 VAC, 47 - 63 Hz power source.