Shortpass Dichroic Mirrors / Beamsplitters
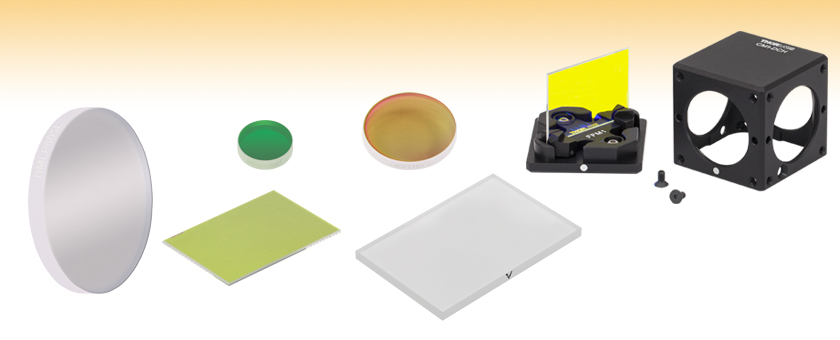
- Cutoff Wavelengths from 425 nm to 1800 nm
- Round and Rectangular Versions Available From Stock
- Durable Hard Coatings
DMSP1000R
25 mm x 36 mm
DMSP805L
Ø2"
DMSP1180
Ø1"
DMSP1500T
Ø1/2"
Application Idea
Dichroic Cage Cube Holding
a Rectangular Dichroic Mirror
DMBP740B
35 mm x 52 mm

Please Wait
Shortpass Dichroic Mirror Selection Guide
(Click Cutoff Wavelengths or Bands for Details)
Dichroic Mirrors Selection Guide |
---|
Shortpass |
Longpass |
Multi-Band |

Features
- Dichroic Filters Function as Shortpass Filters with Minimal Absorption Losses
- Multi-Band Dichroic Filter with Two Transmission Bands and One Reflection Band
- Five Sizes Available: Ø1/2", Ø1", Ø2", 25 mm x 36 mm, or 35 mm x 52 mm
- Hard Coating Allows Easy Handling and Cleaning
- Resistant to Damage from UV Light and Chemicals
Thorlabs' Dichroic Mirrors/Beamsplitters spectrally separate light by transmitting and reflecting light as a function of wavelength. Shortpass dichroic mirrors have a transmission and reflection band that are divided by a cutoff wavelength. This type of dichroic is highly transmissive below the cutoff wavelength and highly reflective above it. We also offer a multi-band dichroic mirror that can be used as a shortpass mirror. This dichroic has two transmission bands and one reflection band that are separated by a cutoff and cut-on wavelength. It is highly transmissive below the cutoff wavelength and above the cut-on wavelength, while highly reflective between the cutoff and cut-on.
Our shortpass dichroic mirrors are offered in several different cutoff wavelengths ranging from 425 to 1800 nm, which are listed in the selection guide graphic to the right. These mirrors are designed for use at a 45° angle of incidence and are available in five sizes: Ø1/2", Ø1", Ø2", 25 mm x 36 mm, and 35 mm x 52 mm. Please see below for transmission and reflection plots of each mirror.
These optics feature a dichroic coating on one surface and an antireflection (AR) coating on the opposing surface. We recommend orienting the optic as illustrated in the diagram to the upper right. On round optics, an engraved arrow points toward the surface with the AR coating; on the 25 mm x 36 mm rectangular optics, the side with the engraving has the dichroic coating. The 35 mm x 52 mm dichroic mirrors feature a caret on the side that points towards the AR-coated surface.
For thermally sensitive applications, Thorlabs offers hot and cold mirrors. We also offer longpass dichroic mirrors, which are highly transmissive above the cut-on wavelength and highly reflective below it.
Applications
As shown in the Applications tab, these optics can be used to combine a beam that has a wavelength (or wavelength range) shorter than the cutoff wavelength with a beam that has a wavelength (or wavelength range) longer than the cutoff wavelength. They are also commonly used to split spatially overlapping beams of different colors.
Surface Quality and Durability
Thorlabs' Dichroic Mirrors/Beamsplitters consist of a hard, ion-beam-sputtered coating deposited on a UV fused silica substrate, providing virtually zero autofluorescence and a low coefficient of thermal expansion, making them an ideal choice for applications from the UV to the near IR. The hard coatings themselves have a 40-20 scratch-dig surface quality and allow the optics to be cleaned and handled like typical glass. As opposed to soft coatings, they have improved resistance to humidity and can withstand high optical irradiation intensities with no noticeable degradation or burns, even under prolonged exposure to ultraviolet light. Please see the Damage Thresholds tab for detailed information on the damage thresholds of these filters.
Mounting Options
For customers who wish to use the round and 25 mm x 36 mm dichroic mirrors/beamsplitters in microscopy applications, Thorlabs manufactures a family of filter cubes and mounts. The Cerna® Breadboard Top with Two-Position Slider can be used to mount the 35 mm x 52 mm dichroics for DIY microscopy.

Click to Enlarge
Round Versions: Engraved Arrow Denotes Side with AR Coating
General Specifications | ||||||||
---|---|---|---|---|---|---|---|---|
Size | Ø1/2" | Ø1" | Ø2" | 25.0 mm x 36.0 mm | 35.0 mm x 52.0 mm | |||
Clear Aperture | >Ø11.43 mm | >Ø22.86 mm | >Ø45.72 mm | >22.5 mm x 32.4 mm | ≥85%, Elliptical | |||
Thickness | 3.2 mma | 3.2 mma | 5.0 mm | 1.0 mm | 3.0 mm | |||
Incident Angle | 45° | |||||||
Surface Quality | 40-20 Scratch-Dig | |||||||
Transmitted Wavefront Error | <λ/4 @ 633 nm Over Clear Aperture | ≤λ/4 @ 632.8 nm Over Clear Aperture | ||||||
Substrate Material | UV Fused Silicab | |||||||
Operating Temperature | -50 to 80 °C | - |
Wavelength Specifications | |||||||||
---|---|---|---|---|---|---|---|---|---|
Item # Prefix | Cutoff Wavelength |
Transmission Band |
Absolute Transmission | Average Transmission | Reflection Band |
Absolute Reflectance | Average Reflectance |
AR Coating Rangea | Damage Threshold |
DMSP425 | 425 nm | 380 - 410 nm | >85% | >90% | 440 - 800 nm | >90% | >95% | 380 - 410 nm | - |
DMSP490 | 490 nm | 380 - 475 nm | >85% | >90% | 505 - 800 nm | >90% | >95% | 380 - 475 nm | - |
DMSP505 | 505 nm | 390 - 490 nm | >85% | >90% | 520 - 800 nm | >90% | >95% | 390 - 490 nm | - |
DMSP550 | 550 nm | 390 - 533 nm | >85% | >90% | 565 - 800 nm | >90% | >95% | 390 - 533 nm | - |
DMSP567 | 567 nm | 390 - 550 nm | >85% | >90% | 584 - 800 nm | >90% | >95% | 390 - 550 nm | - |
DMSP605 | 605 nm | 470 - 590 nm | >85% | >90% | 620 - 800 nm | >90% | >95% | 470 - 590 nm | - |
DMSP638 | 638 nm | 580 - 621 nm | >85% | >90% | 655 - 800 nm | >90% | >95% | 580 - 621 nm | - |
DMSP650 | 650 nm | 410 - 633 nm | >85% | >90% | 685 - 1600 nm | >90% | >95% | 400 - 633 nm | 2.0 J/cm2 (532 nm, 10 Hz, 10 ns, Ø320 µm) |
DMSP680 | 680 nm | 400 - 660 nm | - | >95% | 705 - 1080 nm | - | >95% | 400 - 660 nm | - |
DMBP740b | 740 nm | 400 - 725 nm, 980 - 1700 nm |
- | >93% | 753 - 935 nm | - | >97% | 400 - 1700 nm | - |
DMSP750 | 750 nm | 400 - 730 nm | - | >93% | 770 - 1100 nm | - | >96% | - | - |
DMSP805 | 805 nm | 400 - 788 nm | >85% | >90% | 823 - 1300 nm | >90% | >95% | 400 - 800 nm | 1.00 J/cm2 (532 nm, 10 Hz, 10 ns, Ø250 µm) 7.00 J/cm2 (1064 nm, 10 Hz, 12 ns, Ø250 µm) |
DMSP900 | 900 nm | 400 - 872 nm | >85% | >90% | 932 - 1300 nm | >90% | >95% | 400 - 872 nm | - |
DMSP926 | 926 nm | 400 - 910 nm | - | >92% | 940 - 1700 nm | - | >95% | 400 - 1000 nm | - |
DMSP950 | 950 nm | 420 - 900 nm | >85% | >90% | 990 - 1600 nm | >90% | >95% | 420 - 900 nm | - |
DMSP1000 | 1000 nm | 520 - 985 nm | >85% | >90% | 1020 - 1550 nm | >90% | >95% | 520 - 985 nm | 1.00 J/cm2 (532 nm, 10 Hz, 10 ns, Ø250 µm) 9.50 J/cm2 (1064 nm, 10 Hz, 12 ns, Ø250 µm) |
DMSP1020 | 1020 nm | 650 - 1010 nm | - | >95% | 1030 - 1340 nm | - | >95% | 600 - 1100 nm | - |
DMSP1180 | 1180 nm | 750 - 1100 nm | >85% | >90% | 1260 - 1700 nm | >90% | >95% | 750 - 1100 nm | 3.0 J/cm2 (1064 nm, 10 Hz, 10 ns, Ø1.00 mm) |
DMSP1200 | 1200 nm | 1000 - 1175 nm | - | >93% | 1250 - 1400 nm | - | >99% | 1000 - 1175 nm | - |
DMSP1500 | 1500 nm | >85% | >90% | >90% | >95% | 932 - 1700 nm | |||
DMSP1800 | 1800 nm | >85% | >90% | >90% | >95% | 1500 - 1750 nm | - |
Typical Applications for Dichroic Mirrors/Beamsplitters
- Fluorescence Microscopy
- Splitting or Combining Two Beams of Different Wavelengths
- Filtering of Spectral Components
Ray Diagram Illustration
Figure 1 depicts a dichroic mirror/beamsplitter being used to combine a transmitted beam (blue) with a reflected beam (red). The transmitted beam has a wavelength in the transmission band of the optic, and the reflected beam has a wavelength in the reflection band of the optic. If the direction of propagation is reversed, the optic becomes a beamsplitter, as shown in Figure 2.
In both cases, the combined, polychromatic beam is on the dichroic coated side of the dichroic filter. To better direct the reflection, we recommend orienting them such that the wavelength being reflected does not pass through the substrate. Dichroic mirrors/beamsplitters differ from typical beamsplitters in that the beams can be combined or separated without a significant loss of intensity.

Figure 1. This figure depicts a dichroic mirror being used to combine two beams of different colors.

Figure 2. This figure depicts a dichroic mirror being used to split two beams of different colors.
Damage Threshold Specifications | |
---|---|
Coating Designation (Item # Prefix) |
Damage Threshold |
DMSP650 | 2.0 J/cm2 (532 nm, 10 Hz, 10 ns, Ø320 µm) |
DMSP805 | 1.00 J/cm2 (532 nm, 10 Hz, 10 ns, Ø250 µm) 7.00 J/cm2 (1064 nm, 10 Hz, 12 ns, Ø250 µm) |
DMSP1000 | 1.00 J/cm2 (532 nm, 10 Hz, 10 ns, Ø250 µm) 9.50 J/cm2 (1064 nm, 10 Hz, 12 ns, Ø250 µm) |
DMSP1180 | 3.0 J/cm2 (1064 nm, 10 Hz, 10 ns, Ø1.00 mm) |
DMSP1500 | 7.00 J/cm2 (1064 nm, 10 Hz, 12 ns, Ø250 µm) |
Damage Threshold Data for Thorlabs' Dichroic Mirrors/Beamsplitters
The specifications to the right are measured data for Thorlabs' dichroic mirrors/beamsplitters. Damage threshold specifications are constant for a given coating type, regardless of the size of the mirror.
Laser Induced Damage Threshold Tutorial
The following is a general overview of how laser induced damage thresholds are measured and how the values may be utilized in determining the appropriateness of an optic for a given application. When choosing optics, it is important to understand the Laser Induced Damage Threshold (LIDT) of the optics being used. The LIDT for an optic greatly depends on the type of laser you are using. Continuous wave (CW) lasers typically cause damage from thermal effects (absorption either in the coating or in the substrate). Pulsed lasers, on the other hand, often strip electrons from the lattice structure of an optic before causing thermal damage. Note that the guideline presented here assumes room temperature operation and optics in new condition (i.e., within scratch-dig spec, surface free of contamination, etc.). Because dust or other particles on the surface of an optic can cause damage at lower thresholds, we recommend keeping surfaces clean and free of debris. For more information on cleaning optics, please see our Optics Cleaning tutorial.
Testing Method
Thorlabs' LIDT testing is done in compliance with ISO/DIS 11254 and ISO 21254 specifications.
First, a low-power/energy beam is directed to the optic under test. The optic is exposed in 10 locations to this laser beam for 30 seconds (CW) or for a number of pulses (pulse repetition frequency specified). After exposure, the optic is examined by a microscope (~100X magnification) for any visible damage. The number of locations that are damaged at a particular power/energy level is recorded. Next, the power/energy is either increased or decreased and the optic is exposed at 10 new locations. This process is repeated until damage is observed. The damage threshold is then assigned to be the highest power/energy that the optic can withstand without causing damage. A histogram such as that below represents the testing of one BB1-E02 mirror.

The photograph above is a protected aluminum-coated mirror after LIDT testing. In this particular test, it handled 0.43 J/cm2 (1064 nm, 10 ns pulse, 10 Hz, Ø1.000 mm) before damage.

Example Test Data | |||
---|---|---|---|
Fluence | # of Tested Locations | Locations with Damage | Locations Without Damage |
1.50 J/cm2 | 10 | 0 | 10 |
1.75 J/cm2 | 10 | 0 | 10 |
2.00 J/cm2 | 10 | 0 | 10 |
2.25 J/cm2 | 10 | 1 | 9 |
3.00 J/cm2 | 10 | 1 | 9 |
5.00 J/cm2 | 10 | 9 | 1 |
According to the test, the damage threshold of the mirror was 2.00 J/cm2 (532 nm, 10 ns pulse, 10 Hz, Ø0.803 mm). Please keep in mind that these tests are performed on clean optics, as dirt and contamination can significantly lower the damage threshold of a component. While the test results are only representative of one coating run, Thorlabs specifies damage threshold values that account for coating variances.
Continuous Wave and Long-Pulse Lasers
When an optic is damaged by a continuous wave (CW) laser, it is usually due to the melting of the surface as a result of absorbing the laser's energy or damage to the optical coating (antireflection) [1]. Pulsed lasers with pulse lengths longer than 1 µs can be treated as CW lasers for LIDT discussions.
When pulse lengths are between 1 ns and 1 µs, laser-induced damage can occur either because of absorption or a dielectric breakdown (therefore, a user must check both CW and pulsed LIDT). Absorption is either due to an intrinsic property of the optic or due to surface irregularities; thus LIDT values are only valid for optics meeting or exceeding the surface quality specifications given by a manufacturer. While many optics can handle high power CW lasers, cemented (e.g., achromatic doublets) or highly absorptive (e.g., ND filters) optics tend to have lower CW damage thresholds. These lower thresholds are due to absorption or scattering in the cement or metal coating.
LIDT in linear power density vs. pulse length and spot size. For long pulses to CW, linear power density becomes a constant with spot size. This graph was obtained from [1].

Pulsed lasers with high pulse repetition frequencies (PRF) may behave similarly to CW beams. Unfortunately, this is highly dependent on factors such as absorption and thermal diffusivity, so there is no reliable method for determining when a high PRF laser will damage an optic due to thermal effects. For beams with a high PRF both the average and peak powers must be compared to the equivalent CW power. Additionally, for highly transparent materials, there is little to no drop in the LIDT with increasing PRF.
In order to use the specified CW damage threshold of an optic, it is necessary to know the following:
- Wavelength of your laser
- Beam diameter of your beam (1/e2)
- Approximate intensity profile of your beam (e.g., Gaussian)
- Linear power density of your beam (total power divided by 1/e2 beam diameter)
Thorlabs expresses LIDT for CW lasers as a linear power density measured in W/cm. In this regime, the LIDT given as a linear power density can be applied to any beam diameter; one does not need to compute an adjusted LIDT to adjust for changes in spot size, as demonstrated by the graph to the right. Average linear power density can be calculated using the equation below.
The calculation above assumes a uniform beam intensity profile. You must now consider hotspots in the beam or other non-uniform intensity profiles and roughly calculate a maximum power density. For reference, a Gaussian beam typically has a maximum power density that is twice that of the uniform beam (see lower right).
Now compare the maximum power density to that which is specified as the LIDT for the optic. If the optic was tested at a wavelength other than your operating wavelength, the damage threshold must be scaled appropriately. A good rule of thumb is that the damage threshold has a linear relationship with wavelength such that as you move to shorter wavelengths, the damage threshold decreases (i.e., a LIDT of 10 W/cm at 1310 nm scales to 5 W/cm at 655 nm):
While this rule of thumb provides a general trend, it is not a quantitative analysis of LIDT vs wavelength. In CW applications, for instance, damage scales more strongly with absorption in the coating and substrate, which does not necessarily scale well with wavelength. While the above procedure provides a good rule of thumb for LIDT values, please contact Tech Support if your wavelength is different from the specified LIDT wavelength. If your power density is less than the adjusted LIDT of the optic, then the optic should work for your application.
Please note that we have a buffer built in between the specified damage thresholds online and the tests which we have done, which accommodates variation between batches. Upon request, we can provide individual test information and a testing certificate. The damage analysis will be carried out on a similar optic (customer's optic will not be damaged). Testing may result in additional costs or lead times. Contact Tech Support for more information.
Pulsed Lasers
As previously stated, pulsed lasers typically induce a different type of damage to the optic than CW lasers. Pulsed lasers often do not heat the optic enough to damage it; instead, pulsed lasers produce strong electric fields capable of inducing dielectric breakdown in the material. Unfortunately, it can be very difficult to compare the LIDT specification of an optic to your laser. There are multiple regimes in which a pulsed laser can damage an optic and this is based on the laser's pulse length. The highlighted columns in the table below outline the relevant pulse lengths for our specified LIDT values.
Pulses shorter than 10-9 s cannot be compared to our specified LIDT values with much reliability. In this ultra-short-pulse regime various mechanics, such as multiphoton-avalanche ionization, take over as the predominate damage mechanism [2]. In contrast, pulses between 10-7 s and 10-4 s may cause damage to an optic either because of dielectric breakdown or thermal effects. This means that both CW and pulsed damage thresholds must be compared to the laser beam to determine whether the optic is suitable for your application.
Pulse Duration | t < 10-9 s | 10-9 < t < 10-7 s | 10-7 < t < 10-4 s | t > 10-4 s |
---|---|---|---|---|
Damage Mechanism | Avalanche Ionization | Dielectric Breakdown | Dielectric Breakdown or Thermal | Thermal |
Relevant Damage Specification | No Comparison (See Above) | Pulsed | Pulsed and CW | CW |
When comparing an LIDT specified for a pulsed laser to your laser, it is essential to know the following:
LIDT in energy density vs. pulse length and spot size. For short pulses, energy density becomes a constant with spot size. This graph was obtained from [1].
- Wavelength of your laser
- Energy density of your beam (total energy divided by 1/e2 area)
- Pulse length of your laser
- Pulse repetition frequency (prf) of your laser
- Beam diameter of your laser (1/e2 )
- Approximate intensity profile of your beam (e.g., Gaussian)
The energy density of your beam should be calculated in terms of J/cm2. The graph to the right shows why expressing the LIDT as an energy density provides the best metric for short pulse sources. In this regime, the LIDT given as an energy density can be applied to any beam diameter; one does not need to compute an adjusted LIDT to adjust for changes in spot size. This calculation assumes a uniform beam intensity profile. You must now adjust this energy density to account for hotspots or other nonuniform intensity profiles and roughly calculate a maximum energy density. For reference a Gaussian beam typically has a maximum energy density that is twice that of the 1/e2 beam.
Now compare the maximum energy density to that which is specified as the LIDT for the optic. If the optic was tested at a wavelength other than your operating wavelength, the damage threshold must be scaled appropriately [3]. A good rule of thumb is that the damage threshold has an inverse square root relationship with wavelength such that as you move to shorter wavelengths, the damage threshold decreases (i.e., a LIDT of 1 J/cm2 at 1064 nm scales to 0.7 J/cm2 at 532 nm):
You now have a wavelength-adjusted energy density, which you will use in the following step.
Beam diameter is also important to know when comparing damage thresholds. While the LIDT, when expressed in units of J/cm², scales independently of spot size; large beam sizes are more likely to illuminate a larger number of defects which can lead to greater variances in the LIDT [4]. For data presented here, a <1 mm beam size was used to measure the LIDT. For beams sizes greater than 5 mm, the LIDT (J/cm2) will not scale independently of beam diameter due to the larger size beam exposing more defects.
The pulse length must now be compensated for. The longer the pulse duration, the more energy the optic can handle. For pulse widths between 1 - 100 ns, an approximation is as follows:
Use this formula to calculate the Adjusted LIDT for an optic based on your pulse length. If your maximum energy density is less than this adjusted LIDT maximum energy density, then the optic should be suitable for your application. Keep in mind that this calculation is only used for pulses between 10-9 s and 10-7 s. For pulses between 10-7 s and 10-4 s, the CW LIDT must also be checked before deeming the optic appropriate for your application.
Please note that we have a buffer built in between the specified damage thresholds online and the tests which we have done, which accommodates variation between batches. Upon request, we can provide individual test information and a testing certificate. Contact Tech Support for more information.
[1] R. M. Wood, Optics and Laser Tech. 29, 517 (1998).
[2] Roger M. Wood, Laser-Induced Damage of Optical Materials (Institute of Physics Publishing, Philadelphia, PA, 2003).
[3] C. W. Carr et al., Phys. Rev. Lett. 91, 127402 (2003).
[4] N. Bloembergen, Appl. Opt. 12, 661 (1973).
In order to illustrate the process of determining whether a given laser system will damage an optic, a number of example calculations of laser induced damage threshold are given below. For assistance with performing similar calculations, we provide a spreadsheet calculator that can be downloaded by clicking the button to the right. To use the calculator, enter the specified LIDT value of the optic under consideration and the relevant parameters of your laser system in the green boxes. The spreadsheet will then calculate a linear power density for CW and pulsed systems, as well as an energy density value for pulsed systems. These values are used to calculate adjusted, scaled LIDT values for the optics based on accepted scaling laws. This calculator assumes a Gaussian beam profile, so a correction factor must be introduced for other beam shapes (uniform, etc.). The LIDT scaling laws are determined from empirical relationships; their accuracy is not guaranteed. Remember that absorption by optics or coatings can significantly reduce LIDT in some spectral regions. These LIDT values are not valid for ultrashort pulses less than one nanosecond in duration.

A Gaussian beam profile has about twice the maximum intensity of a uniform beam profile.
CW Laser Example
Suppose that a CW laser system at 1319 nm produces a 0.5 W Gaussian beam that has a 1/e2 diameter of 10 mm. A naive calculation of the average linear power density of this beam would yield a value of 0.5 W/cm, given by the total power divided by the beam diameter:
However, the maximum power density of a Gaussian beam is about twice the maximum power density of a uniform beam, as shown in the graph to the right. Therefore, a more accurate determination of the maximum linear power density of the system is 1 W/cm.
An AC127-030-C achromatic doublet lens has a specified CW LIDT of 350 W/cm, as tested at 1550 nm. CW damage threshold values typically scale directly with the wavelength of the laser source, so this yields an adjusted LIDT value:
The adjusted LIDT value of 350 W/cm x (1319 nm / 1550 nm) = 298 W/cm is significantly higher than the calculated maximum linear power density of the laser system, so it would be safe to use this doublet lens for this application.
Pulsed Nanosecond Laser Example: Scaling for Different Pulse Durations
Suppose that a pulsed Nd:YAG laser system is frequency tripled to produce a 10 Hz output, consisting of 2 ns output pulses at 355 nm, each with 1 J of energy, in a Gaussian beam with a 1.9 cm beam diameter (1/e2). The average energy density of each pulse is found by dividing the pulse energy by the beam area:
As described above, the maximum energy density of a Gaussian beam is about twice the average energy density. So, the maximum energy density of this beam is ~0.7 J/cm2.
The energy density of the beam can be compared to the LIDT values of 1 J/cm2 and 3.5 J/cm2 for a BB1-E01 broadband dielectric mirror and an NB1-K08 Nd:YAG laser line mirror, respectively. Both of these LIDT values, while measured at 355 nm, were determined with a 10 ns pulsed laser at 10 Hz. Therefore, an adjustment must be applied for the shorter pulse duration of the system under consideration. As described on the previous tab, LIDT values in the nanosecond pulse regime scale with the square root of the laser pulse duration:
This adjustment factor results in LIDT values of 0.45 J/cm2 for the BB1-E01 broadband mirror and 1.6 J/cm2 for the Nd:YAG laser line mirror, which are to be compared with the 0.7 J/cm2 maximum energy density of the beam. While the broadband mirror would likely be damaged by the laser, the more specialized laser line mirror is appropriate for use with this system.
Pulsed Nanosecond Laser Example: Scaling for Different Wavelengths
Suppose that a pulsed laser system emits 10 ns pulses at 2.5 Hz, each with 100 mJ of energy at 1064 nm in a 16 mm diameter beam (1/e2) that must be attenuated with a neutral density filter. For a Gaussian output, these specifications result in a maximum energy density of 0.1 J/cm2. The damage threshold of an NDUV10A Ø25 mm, OD 1.0, reflective neutral density filter is 0.05 J/cm2 for 10 ns pulses at 355 nm, while the damage threshold of the similar NE10A absorptive filter is 10 J/cm2 for 10 ns pulses at 532 nm. As described on the previous tab, the LIDT value of an optic scales with the square root of the wavelength in the nanosecond pulse regime:
This scaling gives adjusted LIDT values of 0.08 J/cm2 for the reflective filter and 14 J/cm2 for the absorptive filter. In this case, the absorptive filter is the best choice in order to avoid optical damage.
Pulsed Microsecond Laser Example
Consider a laser system that produces 1 µs pulses, each containing 150 µJ of energy at a repetition rate of 50 kHz, resulting in a relatively high duty cycle of 5%. This system falls somewhere between the regimes of CW and pulsed laser induced damage, and could potentially damage an optic by mechanisms associated with either regime. As a result, both CW and pulsed LIDT values must be compared to the properties of the laser system to ensure safe operation.
If this relatively long-pulse laser emits a Gaussian 12.7 mm diameter beam (1/e2) at 980 nm, then the resulting output has a linear power density of 5.9 W/cm and an energy density of 1.2 x 10-4 J/cm2 per pulse. This can be compared to the LIDT values for a WPQ10E-980 polymer zero-order quarter-wave plate, which are 5 W/cm for CW radiation at 810 nm and 5 J/cm2 for a 10 ns pulse at 810 nm. As before, the CW LIDT of the optic scales linearly with the laser wavelength, resulting in an adjusted CW value of 6 W/cm at 980 nm. On the other hand, the pulsed LIDT scales with the square root of the laser wavelength and the square root of the pulse duration, resulting in an adjusted value of 55 J/cm2 for a 1 µs pulse at 980 nm. The pulsed LIDT of the optic is significantly greater than the energy density of the laser pulse, so individual pulses will not damage the wave plate. However, the large average linear power density of the laser system may cause thermal damage to the optic, much like a high-power CW beam.
Posted Comments: | |
Xavier Attendu
 (posted 2020-12-06 04:58:37.94) Dear Sir/Madam,
I am wondering how water resistant the shortpass filters are. Specifically, we are considering cutting the DMSP950R to our own dimensions with a glasscutter, which requires making the component wet. Will this deteriorate the optical performances or the durability? Thanks in advance for your assistance. YLohia
 (posted 2020-12-09 03:38:43.0) Thank you for contacting Thorlabs. We dice these dichroic mirrors using a process that exposes them to water. As long as the parts are cleaned afterwards (with alcohol/acetone), we would not expect any issues. Zhang Yongqing
 (posted 2020-11-17 21:03:59.493) I wonder if your company has a 700SP dichroic mirror(36×24 mm),And the part of the band coated with anti-reflection film we hope is not only less than 700nm,but the whole band,such as 600nm-1500nm. Because I found that if the beam above 700nm could not be transmitted through the glass layer of the anti-reflection film, it would be reflected back to the light path of the long band of the dichroic mirror, but it was different from the original light path. It will lead to ghost Beam, which will have a huge impact on us. YLohia
 (posted 2020-12-01 10:31:15.0) Thank you for contacting Thorlabs. Unfortunately, we do not offer such a dichroic mirror at the moment. Syed Aljunid
 (posted 2020-10-20 03:31:59.483) Hello,
Can I know the transmissin/reflection specs for 0°- 15° AOI for DMSP950?
Thank you YLohia
 (posted 2020-10-20 04:28:57.0) Hello, thank you for contacting Thorlabs. I have reached out to you directly with some data. Gabriel MENNERAT
 (posted 2020-08-28 15:00:02.32) Hello,
What is the LIDT of DMSP650 for 532 nm, 6 ns, 10 Hz pulses ?
Thank you.
Best regards.
GM YLohia
 (posted 2020-08-28 04:41:51.0) Hello GM, thank you for contacting Thorlabs. The damage threshold for the DMSP650 is: 2 J/cm^2 for a 10 ns, 10 Hz, 0.32 mm spot. Jordan Teich
 (posted 2020-08-06 16:22:33.6) Hello,
What is the parallelism of the surfaces for the Dichroic shortpass beamsplitter, DMSP1180L?
Does this optic have a wedge in it? Or are the surfaces designed to be highly parallel? YLohia
 (posted 2020-08-07 02:01:11.0) Hello, thank you for contacting Thorlabs. The parallelism spec of <3 arcmin for this optic can be found on the engineering drawing: https://www.thorlabs.com/_sd.cfm?fileName=TTN028298-E0W.pdf&partNumber=DMSP1180L. These optics are not intentionally wedged by design. kevin hargrave
 (posted 2020-02-03 09:47:09.19) What are the mechanical diameter and thickness tolerances on DMSP1000T? YLohia
 (posted 2020-02-03 12:01:33.0) Thank you for contacting Thorlabs. The diameter tolerance is 12.7mm +0.0mm/-0.1mm and the thickness tolerance is 3.2mm +0.0mm/-0.1mm. Geo Davis
 (posted 2019-10-18 18:53:13.043) Hi,
I wish to purchase DMSP805. But I have a query.
I plan to use the DMSP805 with a pulsed laser (1064nm, 4ns Gaussian) with a maximum energy of 100 mJ. The diameter of the beam is ~4.5 mm at the aperture (but it's Gaussian).
Please let me know if the DMSP805 can withstand the power intensity of the laser. What is the damage threshold of DMSP805?
Thank you.
Regards,
Geo Davis YLohia
 (posted 2019-10-18 12:27:05.0) Hello Geo, we have the pulsed damage threshold specified for the DMSP805 in the "Damage Thresholds" tab on this page. It is 7.00 J/cm2 (1064 nm, 10 Hz, 12 ns, Ø250 µm). With your 4.5mm diameter, your 100 mJ beam will be under the spec. Hugh Wilson
 (posted 2019-03-28 21:09:04.22) Hello, I would like to ask what the reflected wavefront errors are (RWE) for the DMSP805 dichroics. In the pop-up information panel, I can only see a specification of the transmitted wavefront error. Thanks very much! YLohia
 (posted 2019-03-29 09:21:16.0) Hello, thank you for contacting Thorlabs. The RWE on these dichroics are around 2-3 waves for the round (thicker) optics. It is ~5 waves for the rectangular (thinner) optics. user
 (posted 2019-03-19 18:46:04.12) I am using one of these mirrors at 45deg in an Olympus microscope to separate visible imaging and 1550nm tuneable laser output. Unfortunately, I am getting 10dB ripples with a period of approx 0.8nm in the reflection from the mirror.
Similar problems are encountered at shorter wavelength (and absent if other optics is used)
Do I have a faulty component? nbayconich
 (posted 2019-04-05 08:23:43.0) Thank you for contacting Thorlabs. Small dips in power of the transmitted or reflected beam will be expected for these dichroics, would it be possible to provide the average power of your source? It would be best to know more about your setup and the additional optics used. Please verify if possible that the absolute transmitted & reflected power is above our guaranteed values under our wavelength specifications table.
You mentioned that the ripples are absent if other optics are used with your dichroic. What other optics do you have in the optical path when these ripples are present and what optics have you added which remove these ripples in the reflection?
A techsupport representative will reach out to you directly to help troubleshoot. pablo.dias
 (posted 2019-02-27 17:12:34.137) Hi, do you have any information about how the dicroic changes the polarization if the incidente beam isn't a s or p wave?
Thank you. nbayconich
 (posted 2019-03-01 03:27:00.0) Thank you for contacting Thorlabs. I will reach out to you directly to provide more information about the effects of this Dichroic on your S & P polarization states. edowd
 (posted 2019-01-09 16:11:58.057) Hello, How does the reflectance change with the angle of incidence? I am using the DMSP805L as a mirror for converging 1064nm light and have found that the DMSP805L introduces astigmatism at the focus (compared to when I use a mirror - BB2E03). I wonder if this is related to optics thickness (because it is thinner than a mirror, perhaps it is less flat) or the dielectric coating itself (no matter the thickness, one should expect this from a dielectric optic). Thanks much. YLohia
 (posted 2019-04-01 03:47:24.0) Hello, thank you for contacting Thorlabs. The astigmatism is expected due to the nature of dielectric coatings used in these dichroics. The thickness is usually a bigger factor in the degradation of reflected beam quality in our thinner dichroics (DMSP805R). ana.rodriguez
 (posted 2018-11-01 13:54:08.637) Hi, how does the curve looks like when the angle is not exactly 45º? Can I have some data? I am using the DMSP950R. I am working in spectral interferometry and see some distorsions in my signal but not sure if this is polarization- OR angle of incidence- related. thanks YLohia
 (posted 2018-11-01 12:05:43.0) Hello, thank you for contacting Thorlabs. I will reach out to you directly with some data. Please note that it's possible that the poor RWE of these can have an impact on applications such as interferometry. The circular versions of these optics tend to offer better RWE performance than the rectangular versions by virtue of being thicker. akuznetsov
 (posted 2018-09-28 18:04:38.537) Can you please provide polarization transmission for your dichroic products? YLohia
 (posted 2018-10-01 09:18:33.0) Hello, the polarization-based reflection and transmission plots for these dichroics can be found on the main product page in the products' corresponding blue info icons. tomrumx
 (posted 2018-09-20 17:44:38.25) Hello, i need to combine two laser beams, red CW laser diode and pulsed IR laser of 3000 nm wavelength. I guess I need semi-transparent mirror which passes IR laser and reflects red laser into one beam. Which mirror should I use? YLohia
 (posted 2018-09-20 04:17:09.0) Hello, thank you for contacting Thorlabs. Based on our direct discussion, it appears that you do not mind a high loss for your led light as long as the IR light has a relatively high transmission. In that case, we recommend looking into something like the WG31050-E1, which is a sapphire window with an AR coating for 3um, at 45 degrees. The IR beam should be mostly transmitted and there should be some reflection of the visible beam as well (enough to be seen if the input power is high enough), though we cannot guarantee exactly what the performance would look like. afalamas
 (posted 2018-09-17 13:38:59.493) Hello,
I would like to ask, does this filter need to be mounted at 45 degrees relative to the incident beam?
I would like to use it with fs lasers, can you tell me about group velocity dispersion and the damage threshold?
Thank you! YLohia
 (posted 2018-09-18 03:09:21.0) Hello, thank you for contacting Thorlabs. For optimal performance, this filter should be used at 45 degrees. That being said, it can be used at various AOIs as well, though we cannot guarantee the performance in that case and there will be a shift in the cutoff wavelength & transmission. I have reached out to you directly with the GVD data. Unfortunately, we have not yet performed conclusive damage threshold testing on this unit. benalunda10
 (posted 2018-08-22 19:58:03.883) I was wondering if I could use the DMSP567 dichroic mirror or any shortpass /&longpass dichroic mirror beamsplitters with POLARIZED light. I see you mention uplolarized light.
Thanks. YLohia
 (posted 2018-08-23 10:57:06.0) Hello, you can definitely use this dichroic mirror with linearly polarized light. We have data for s- and p-polarized light that can be accessed by clicking the blue "info" icon next to the part number. As you can see, these differ slightly from the unpolarized case. jonas.ogien
 (posted 2018-06-15 10:00:26.233) Hello,
I have been using a DMSP650R as a dichroic mirror (in reflection) in an arm of a broadband white light interferometer. I noticed strong dispersion effects in the interference fringes. Nevertheless, when using a 50:50 beamsplitter (BSW10R), those effects do not appear. I have been careful to position them so that light does not pass through the glass subtrate. Do you know what could be the reason for this difference ? I would like to know if I could get more information regarding the difference in coating of those two elements in order to try to understand the difference I observed.
Thank you. YLohia
 (posted 2018-07-02 08:50:20.0) Hello, thank you for contacting Thorlabs. This is expected behavior out of the two optics. One coating is designed to reflect white light relatively evenly (the BSW10) while the other is designed to reflect only some part of that spectrum and pass the rest (DMSP650). Are you talking about GVD effects here? Alternatively, if you’re looking at the reflected beam, the DMSP is going to be more curved, and thus induce worse-looking fringes. lijie.wang
 (posted 2018-06-08 11:47:44.203) Hi, I would like to buy a 567 nm short pass dichroic mirror, but may I ask about it's group delay dispersion(GDD)? or do you have any experience to use it on fs laser pulse? YLohia
 (posted 2018-06-15 12:59:51.0) Hello, thank you for contacting Thorlabs. I will reach out to you directly with the theoretical GDD plots. hutchguy
 (posted 2018-04-04 19:42:07.0) Under the "Damage Thresholds" tab I only see 4 of the 13 DMSP coatings. Is there a good reason why the other 9 aren't specified?
I am specifically interested in this information for DMSP490 and DMSP505. nbayconich
 (posted 2018-04-06 09:18:29.0) Thank you for contacting Thorlabs. We have not yet tested the other dichroic mirror coatings for a pulsed laser damage threshold. I will reach out to you directly to discuss your application and suggest whether these will be suitable. user
 (posted 2017-11-06 18:08:54.977) Do the reflection/transmission curves change very much at zero degrees incidence? The plots seem to all be at 45 degrees. tfrisch
 (posted 2017-11-16 11:49:21.0) Hello, thank you for contacting Thorlabs. At greater angles of incidence, the cutoff wavelength will shift towards shorter wavelengths, and and lower angles of incidence, the edge will shift to longer wavelengths. In both cases, the shape of the cutoff curve would change. While angle tuning is common to adjust the cutoff edge a small amount, reducing the angle of incidence to zero would have significant effect on the performance. Please reach out to us at TechSupport@Thorlabs.com if you'd like to discuss a specific dichroic mirror. jwu45
 (posted 2017-10-13 15:43:08.94) Do you have a thinner one for the DMSP1000L? It's too thick and has a lot of aberration to our system. nbayconich
 (posted 2017-11-13 02:48:51.0) Thank you for contacting Thorlabs. We can provide these dichroic mirrors in thinner versions. I will contact you directly with more information about our custom capabilities. aortiza
 (posted 2017-05-29 16:58:37.437) Hello. I was wondering if there is information about the reflected wavefront error we can expect of this filters.
Thanks,
Antonio nbayconich
 (posted 2017-06-15 09:53:00.0) Thank you for contacting Thorlabs. The reflected wavefront error is higher in these dichroic mirrors around 2-3 Waves as opposed to 1/4 wave of the transmitted wavefront error. Around 5 waves for the 1mm thick optics. A Techsupport representative will contact you directly. parksj003
 (posted 2016-12-09 17:45:09.043) Hello,
I am looking for the proper dichroic mirror (size of 25.0 mm x 36.0 mm) for the super- resolution microscope.
Would you let me know if there is any rule to choose proper dichroic in terms of flatness? As far as I know, flatness affects the imaging quality a lot. Here, the beam is reflected at the dichroic and directed to the objective lens.
Best,
Seongjun Park tfrisch
 (posted 2016-12-15 05:18:53.0) Hello, thank you for contacting Thorlabs. In most imaging applications, the transmitted wavefront error (TWE) is more critical than the flatness, and generally TWE is much better than the flatness. I will contact you directly about when to use flatness and when to use TWE. |


Click to Enlarge
Click Here for Raw Data from 250 - 2500 nm
The blue shaded regions denote the transmission and reflection bands for which the performance is guaranteed to meet the stated specifications. Performance outside the shaded regions will vary from lot to lot and is not guaranteed.


Click to Enlarge
Click Here for Raw Data from 250 - 2500 nm
The blue shaded regions denote the transmission and reflection bands for which the performance is guaranteed to meet the stated specifications. Performance outside the shaded regions will vary from lot to lot and is not guaranteed.


Click to Enlarge
Click Here for Raw Data from 250 - 2500 nm
The blue shaded regions denote the transmission and reflection bands for which the performance is guaranteed to meet the stated specifications. Performance outside the shaded regions will vary from lot to lot and is not guaranteed.


Click to Enlarge
Click Here for Raw Data from 250 - 2500 nm
The blue shaded regions denote the transmission and reflection bands for which the performance is guaranteed to meet the stated specifications. Performance outside the shaded regions will vary from lot to lot and is not guaranteed.


Click to Enlarge
Click Here for Raw Data from 250 - 2500 nm
The blue shaded regions denote the transmission and reflection bands for which the performance is guaranteed to meet the stated specifications. Performance outside the shaded regions will vary from lot to lot and is not guaranteed.


Click to Enlarge
Click Here for Raw Data from 250 - 2500 nm
The blue shaded regions denote the transmission and reflection bands for which the performance is guaranteed to meet the stated specifications. Performance outside the shaded regions will vary from lot to lot and is not guaranteed.


Click to Enlarge
Click Here for Raw Data from 250 - 2500 nm
The blue shaded regions denote the transmission and reflection bands for which the performance is guaranteed to meet the stated specifications. Performance outside the shaded regions will vary from lot to lot and is not guaranteed.


Click to Enlarge
Click Here for Raw Data from 250 - 2500 nm
The blue shaded regions denote the transmission and reflection bands for which the performance is guaranteed to meet the stated specifications. Performance outside the shaded regions will vary from lot to lot and is not guaranteed.


Click to Enlarge
Click Here for Raw Data from 250 - 2500 nm
The blue shaded regions denote the transmission and reflection bands for which the performance is guaranteed to meet the stated specifications. Performance outside the shaded regions will vary from lot to lot and is not guaranteed.


Click to Enlarge
Click Here for Raw Data from 250 - 2500 nm
The blue shaded regions denote the transmission and reflection bands for which the performance is guaranteed to meet the stated specifications. Performance outside the shaded regions will vary from lot to lot and is not guaranteed.


Click to Enlarge
Click Here for Raw Data from 350 - 2500 nm
The blue shaded regions denote the transmission and reflection bands for which the performance is guaranteed to meet the stated specifications. Performance outside the shaded regions will vary from lot to lot and is not guaranteed.


Click to Enlarge
Click Here for Raw Data from 250 - 2500 nm
The blue shaded regions denote the transmission and reflection bands for which the performance is guaranteed to meet the stated specifications. Performance outside the shaded regions will vary from lot to lot and is not guaranteed.


Click to Enlarge
Click Here for Raw Data from 250 - 2500 nm
The blue shaded regions denote the transmission and reflection bands for which the performance is guaranteed to meet the stated specifications. Performance outside the shaded regions will vary from lot to lot and is not guaranteed.


Click to Enlarge
Click Here for Raw Data from 250 - 2500 nm
The blue shaded regions denote the transmission and reflection bands for which the performance is guaranteed to meet the stated specifications. Performance outside the shaded regions will vary from lot to lot and is not guaranteed.


Click to Enlarge
Click Here for Raw Data from 250 - 2500 nm
The blue shaded regions denote the transmission and reflection bands for which the performance is guaranteed to meet the stated specifications. Performance outside the shaded regions will vary from lot to lot and is not guaranteed.


Click to Enlarge
Click Here for Raw Data from 250 - 2500 nm
The blue shaded regions denote the transmission and reflection bands for which the performance is guaranteed to meet the stated specifications. Performance outside the shaded regions will vary from lot to lot and is not guaranteed.


Click to Enlarge
Click Here for Raw Data from 250 - 2500 nm
The blue shaded regions denote the transmission and reflection bands for which the performance is guaranteed to meet the stated specifications. Performance outside the shaded regions will vary from lot to lot and is not guaranteed.


Click to Enlarge
Click Here for Raw Data from 250 - 2500 nm
The blue shaded regions denote the transmission and reflection bands for which the performance is guaranteed to meet the stated specifications. Performance outside the shaded regions will vary from lot to lot and is not guaranteed.


Click to Enlarge
Click Here for Raw Data from 250 - 2500 nm
The blue shaded regions denote the transmission and reflection bands for which the performance is guaranteed to meet the stated specifications. Performance outside the shaded regions will vary from lot to lot and is not guaranteed.


Click to Enlarge
Click Here for Raw Data from 250 - 2500 nm
The blue shaded regions denote the transmission and reflection bands for which the performance is guaranteed to meet the stated specifications. Performance outside the shaded regions will vary from lot to lot and is not guaranteed.


Click to Enlarge
Click Here for Raw Data from 250 - 2500 nm
The blue shaded regions denote the transmission and reflection bands for which the performance is guaranteed to meet the stated specifications. Performance outside the shaded regions will vary from lot to lot and is not guaranteed.