Bifurcated Fiber Bundles: 19 Fibers
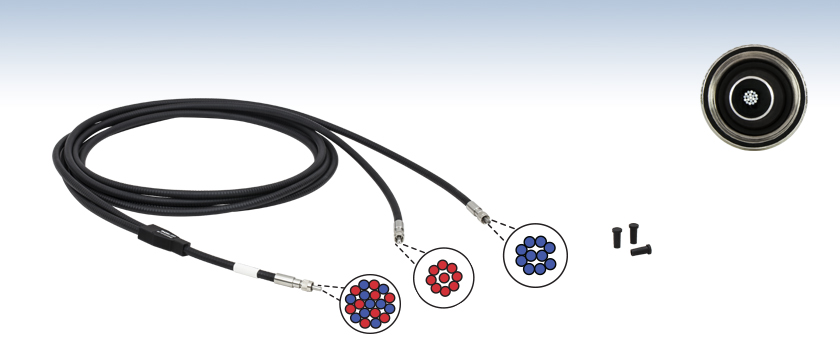
- 2 m Total Length Y-Bundles with 19 Fibers in the Common End
- High-OH (UV to NIR) or Low-OH (Visible to IR) Fiber Composition
- Custom Fiber Bundles Also Available
BF19Y2HS02
Ø200 µm Core Fiber,
High-OH Content
19-Fiber Common End
9-Fiber End
10-Fiber End
Black Rubber
Dust Caps Included
Common Connector Face
BF19Y2
19 x Ø200 µm Core Fibers

Please Wait

Click to Enlarge
The common end of the Ø200 µm core Y-cable when the 10-fiber end is illuminated.

Click to Enlarge
The common end of the Ø200 µm core Y-cable when the 9-fiber end is illuminated.
Features
- Y-Cable with a 19-Fiber Common End Mapped to a 10-Fiber Leg and a 9-Fiber Leg
- SMA905 Connectors Terminate All Ends
- High-OH (UV Enhanced) or Low-OH (IR Enhanced) Fiber Configurations
- High-Quality FT061PS Stainless Steel Tubing with Black Plastic Sheath for Rugged Applications
- No Broken Fibers
- One Black Rubber Dust Cap Included for Each Connector
- Custom Versions Available
These Bifurcated Fiber Bundles, also known as fanout or Y-cables, are constructed from 19 high-grade optical fibers arranged in a round geometry and encased in FT061PS black-plastic-sheathed stainless steel tubing for durability. The 19 fibers are mapped to a 10-fiber end and a 9-fiber end, as shown in the photos below to the right. Compared to our Bifurcated Fiber Bundles with two fibers, these offer more uniform illumination because the input spot can be more evenly distributed over 19 fibers than it can be over two. Additionally, they offer brighter illumination because 19 fibers in a round geometry can collect more light than two.
We offer these bundles with a fiber core size of Ø200 µm and either 19 high-OH fibers or 19 low-OH fibers. All three ends of the cable are terminated with SMA905 connectors with stainless steel sleeves that are engraved with the number of fibers in each leg. The junction box is engraved with the item # on one side and the core diameter, numerical aperture (NA), and wavelength range of the fiber on the other (see the photos below).
One leg of each bundle contains all 19 fibers before passing through a junction where the cable splits into two legs: one containing 10 fibers and one containing 9. The cable is 2 m long from the common end to the branched end. See the table to the right for a summary of the dimensions. The two legs are threaded through a sliding clamp (see drawing above to the right) so that the breakout length of the cable can be adjusted. The clamp can be locked in place by tightening the 8-32 setscrew with the included 5/64" hex key.
When using the common end as the input, these cables perform best when used with sources that provide even illumination across all cores, such as white light sources or LEDs with a large emitter angle (see the photos to the right for examples of the end face geometry in the common connector).
Each bundle includes three protective rubber caps that shield the connector ends from dust and other hazards. Additional CAPM Rubber Fiber Caps or CAPSM Metal Threaded Fiber Caps for SMA-terminated ends are also offered separately.
Custom fiber bundles are available upon request, including straight bundles and bifurcated fiber bundles, with one common connector split into two or more connectors. See the Custom Bundles tab for an overview of some of our custom bundle capabilities. Please contact Tech Support for details.

Click to Enlarge
The stainless steel sleeve at the end of each leg is engraved
with the number of contained fibers.

Click to Enlarge
The front of the junction box is engraved with the item #, while the back is engraved with the core size, NA, and wavelength range of the fibers.
Bundles Selection Guide | |||||||||
---|---|---|---|---|---|---|---|---|---|
Straight | Bifurcated | Fan-Out | |||||||
![]() |
![]() |
![]() |
![]() |
![]() |
![]() |
![]() |
![]() |
![]() |
![]() |
Round | Linear to Linear |
Round to Linear |
2-Fiber Y-Bundle |
19-Fiber Y-Bundle |
Reflection Probes |
Reflection Probes with Reference Leg |
Transmission Dip Probes |
1-to-4 | 1-to-7 |
All Fiber Patch Cables |

Click to Enlarge
Custom 1-to-4 Fan-Out Cable
Custom Fiber Bundles
Thorlabs is pleased to offer custom straight and fan-out fiber bundles with random or mapped fiber configurations. The table below outlines some of our current bundle production capabilities. We are in the process of expanding these production capabilities, so do not hesitate to inquire if you do not see the bundle that you require described here.
Some custom bundles will require techniques outside of our usual production processes. As a result, we cannot guarantee that we will be able to make a bundle configuration to fit the requirements of your specific application. However, our engineers will be happy to work with you to determine if Thorlabs can produce a fiber bundle that fulfills your needs. To receive a quote, please provide a drawing or draft of your bundle configuration.

Click to Enlarge
Custom Silica Fiber Bundle with SMA905 Connectors
Custom Bundle Capabilities | |||
---|---|---|---|
Bundle Configuration |
Straighta | Fan Out (2 or More Legs)a,b | |
Fiber Types |
Single Mode | Standard (320 to 2100 nm), Ultra-High NA (960 to 1600 nm), Photosensitive (980 to 1600 nm) |
|
Multimode | 0.10 NA Step Index (280 to 750 nm), 0.22 NA Step Index (190 to 2500 nm), 0.39 NA Step Index (300 to 2200 nm), Multimode Graded Index (750 to 1450 nm), Multimode ZrF4 (285 nm to 4.5 µm) |
||
Tubing Optionsc | Thorlabs' Stock Furcation Tubing, Stainless Steel Tubing or Black Heat Shrink Tubing | ||
Connectors | SMA905 (Ø2 mm Max Cored), FC/PC (Ø800 µm Max Cored), Ø1/4" Probe, or Flat-Cleaved Unterminated Fiber |
||
Length Tolerancee | ±0.14 m | ||
Active Area Geometryf |
Round or Linear | ||
Angle Polishing | On Special Request. Available for up to Ø105 µm Core on Single Fiber End. Please Inquire for More Information. |
Our cable engineers are available to help manufacture a bundle for your application.
Please contact techsupport@thorlabs.com with your custom bundle requests.
Please provide a drawing or draft of your custom bundle to expedite quote processing.
Quick Links |
---|
Damage at the Air / Glass Interface |
Intrinsic Damage Threshold |
Preparation and Handling of Optical Fibers |
Laser-Induced Damage in Silica Optical Fibers
The following tutorial details damage mechanisms relevant to unterminated (bare) fiber, terminated optical fiber, and other fiber components from laser light sources. These mechanisms include damage that occurs at the air / glass interface (when free-space coupling or when using connectors) and in the optical fiber itself. A fiber component, such as a bare fiber, patch cable, or fused coupler, may have multiple potential avenues for damage (e.g., connectors, fiber end faces, and the device itself). The maximum power that a fiber can handle will always be limited by the lowest limit of any of these damage mechanisms.
While the damage threshold can be estimated using scaling relations and general rules, absolute damage thresholds in optical fibers are very application dependent and user specific. Users can use this guide to estimate a safe power level that minimizes the risk of damage. Following all appropriate preparation and handling guidelines, users should be able to operate a fiber component up to the specified maximum power level; if no maximum is specified for a component, users should abide by the "practical safe level" described below for safe operation of the component. Factors that can reduce power handling and cause damage to a fiber component include, but are not limited to, misalignment during fiber coupling, contamination of the fiber end face, or imperfections in the fiber itself. For further discussion about an optical fiber’s power handling abilities for a specific application, please contact Thorlabs’ Tech Support.

Click to Enlarge
Undamaged Fiber End

Click to Enlarge
Damaged Fiber End
Damage at the Air / Glass Interface
There are several potential damage mechanisms that can occur at the air / glass interface. Light is incident on this interface when free-space coupling or when two fibers are mated using optical connectors. High-intensity light can damage the end face leading to reduced power handling and permanent damage to the fiber. For fibers terminated with optical connectors where the connectors are fixed to the fiber ends using epoxy, the heat generated by high-intensity light can burn the epoxy and leave residues on the fiber facet directly in the beam path.
Estimated Optical Power Densities on Air / Glass Interfacea | ||
---|---|---|
Type | Theoretical Damage Thresholdb | Practical Safe Levelc |
CW (Average Power) |
~1 MW/cm2 | ~250 kW/cm2 |
10 ns Pulsed (Peak Power) |
~5 GW/cm2 | ~1 GW/cm2 |
Damage Mechanisms on the Bare Fiber End Face
Damage mechanisms on a fiber end face can be modeled similarly to bulk optics, and industry-standard damage thresholds for UV Fused Silica substrates can be applied to silica-based fiber. However, unlike bulk optics, the relevant surface areas and beam diameters involved at the air / glass interface of an optical fiber are very small, particularly for coupling into single mode (SM) fiber. therefore, for a given power density, the power incident on the fiber needs to be lower for a smaller beam diameter.
The table to the right lists two thresholds for optical power densities: a theoretical damage threshold and a "practical safe level". In general, the theoretical damage threshold represents the estimated maximum power density that can be incident on the fiber end face without risking damage with very good fiber end face and coupling conditions. The "practical safe level" power density represents minimal risk of fiber damage. Operating a fiber or component beyond the practical safe level is possible, but users must follow the appropriate handling instructions and verify performance at low powers prior to use.
Calculating the Effective Area for Single Mode and Multimode Fibers
The effective area for single mode (SM) fiber is defined by the mode field diameter (MFD), which is the cross-sectional area through which light propagates in the fiber; this area includes the fiber core and also a portion of the cladding. To achieve good efficiency when coupling into a single mode fiber, the diameter of the input beam must match the MFD of the fiber.
As an example, SM400 single mode fiber has a mode field diameter (MFD) of ~Ø3 µm operating at 400 nm, while the MFD for SMF-28 Ultra single mode fiber operating at 1550 nm is Ø10.5 µm. The effective area for these fibers can be calculated as follows:
SM400 Fiber: Area = Pi x (MFD/2)2 = Pi x (1.5 µm)2 = 7.07 µm2 = 7.07 x 10-8 cm2
SMF-28 Ultra Fiber: Area = Pi x (MFD/2)2 = Pi x (5.25 µm)2 = 86.6 µm2 = 8.66 x 10-7 cm2
To estimate the power level that a fiber facet can handle, the power density is multiplied by the effective area. Please note that this calculation assumes a uniform intensity profile, but most laser beams exhibit a Gaussian-like shape within single mode fiber, resulting in a higher power density at the center of the beam compared to the edges. Therefore, these calculations will slightly overestimate the power corresponding to the damage threshold or the practical safe level. Using the estimated power densities assuming a CW light source, we can determine the corresponding power levels as:
SM400 Fiber: 7.07 x 10-8 cm2 x 1 MW/cm2 = 7.1 x 10-8 MW = 71 mW (Theoretical Damage Threshold)
7.07 x 10-8 cm2 x 250 kW/cm2 = 1.8 x 10-5 kW = 18 mW (Practical Safe Level)
SMF-28 Ultra Fiber: 8.66 x 10-7 cm2 x 1 MW/cm2 = 8.7 x 10-7 MW = 870 mW (Theoretical Damage Threshold)
8.66 x 10-7 cm2 x 250 kW/cm2 = 2.1 x 10-4 kW = 210 mW (Practical Safe Level)
The effective area of a multimode (MM) fiber is defined by the core diameter, which is typically far larger than the MFD of an SM fiber. For optimal coupling, Thorlabs recommends focusing a beam to a spot roughly 70 - 80% of the core diameter. The larger effective area of MM fibers lowers the power density on the fiber end face, allowing higher optical powers (typically on the order of kilowatts) to be coupled into multimode fiber without damage.
Damage Mechanisms Related to Ferrule / Connector Termination

Click to Enlarge
Plot showing approximate input power that can be incident on a single mode silica optical fiber with a termination. Each line shows the estimated power level due to a specific damage mechanism. The maximum power handling is limited by the lowest power level from all relevant damage mechanisms (indicated by a solid line).
Fibers terminated with optical connectors have additional power handling considerations. Fiber is typically terminated using epoxy to bond the fiber to a ceramic or steel ferrule. When light is coupled into the fiber through a connector, light that does not enter the core and propagate down the fiber is scattered into the outer layers of the fiber, into the ferrule, and the epoxy used to hold the fiber in the ferrule. If the light is intense enough, it can burn the epoxy, causing it to vaporize and deposit a residue on the face of the connector. This results in localized absorption sites on the fiber end face that reduce coupling efficiency and increase scattering, causing further damage.
For several reasons, epoxy-related damage is dependent on the wavelength. In general, light scatters more strongly at short wavelengths than at longer wavelengths. Misalignment when coupling is also more likely due to the small MFD of short-wavelength SM fiber that also produces more scattered light.
To minimize the risk of burning the epoxy, fiber connectors can be constructed to have an epoxy-free air gap between the optical fiber and ferrule near the fiber end face. Our high-power multimode fiber patch cables use connectors with this design feature.
Determining Power Handling with Multiple Damage Mechanisms
When fiber cables or components have multiple avenues for damage (e.g., fiber patch cables), the maximum power handling is always limited by the lowest damage threshold that is relevant to the fiber component. In general, this represents the highest input power that can be incident on the patch cable end face and not the coupled output power.
As an illustrative example, the graph to the right shows an estimate of the power handling limitations of a single mode fiber patch cable due to damage to the fiber end face and damage via an optical connector. The total input power handling of a terminated fiber at a given wavelength is limited by the lower of the two limitations at any given wavelength (indicated by the solid lines). A single mode fiber operating at around 488 nm is primarily limited by damage to the fiber end face (blue solid line), but fibers operating at 1550 nm are limited by damage to the optical connector (red solid line).
In the case of a multimode fiber, the effective mode area is defined by the core diameter, which is larger than the effective mode area for SM fiber. This results in a lower power density on the fiber end face and allows higher optical powers (on the order of kilowatts) to be coupled into the fiber without damage (not shown in graph). However, the damage limit of the ferrule / connector termination remains unchanged and as a result, the maximum power handling for a multimode fiber is limited by the ferrule and connector termination.
Please note that these are rough estimates of power levels where damage is very unlikely with proper handling and alignment procedures. It is worth noting that optical fibers are frequently used at power levels above those described here. However, these applications typically require expert users and testing at lower powers first to minimize risk of damage. Even still, optical fiber components should be considered a consumable lab supply if used at high power levels.
Intrinsic Damage Threshold
In addition to damage mechanisms at the air / glass interface, optical fibers also display power handling limitations due to damage mechanisms within the optical fiber itself. These limitations will affect all fiber components as they are intrinsic to the fiber itself. Two categories of damage within the fiber are damage from bend losses and damage from photodarkening.
Bend Losses
Bend losses occur when a fiber is bent to a point where light traveling in the core is incident on the core/cladding interface at an angle higher than the critical angle, making total internal reflection impossible. Under these circumstances, light escapes the fiber, often in a localized area. The light escaping the fiber typically has a high power density, which burns the fiber coating as well as any surrounding furcation tubing.
A special category of optical fiber, called double-clad fiber, can reduce the risk of bend-loss damage by allowing the fiber’s cladding (2nd layer) to also function as a waveguide in addition to the core. By making the critical angle of the cladding/coating interface higher than the critical angle of the core/clad interface, light that escapes the core is loosely confined within the cladding. It will then leak out over a distance of centimeters or meters instead of at one localized spot within the fiber, minimizing the risk of damage. Thorlabs manufactures and sells 0.22 NA double-clad multimode fiber, which boasts very high, megawatt range power handling.
Photodarkening
A second damage mechanism, called photodarkening or solarization, can occur in fibers used with ultraviolet or short-wavelength visible light, particularly those with germanium-doped cores. Fibers used at these wavelengths will experience increased attenuation over time. The mechanism that causes photodarkening is largely unknown, but several fiber designs have been developed to mitigate it. For example, fibers with a very low hydroxyl ion (OH) content have been found to resist photodarkening and using other dopants, such as fluorine, can also reduce photodarkening.
Even with the above strategies in place, all fibers eventually experience photodarkening when used with UV or short-wavelength light, and thus, fibers used at these wavelengths should be considered consumables.
Preparation and Handling of Optical Fibers
General Cleaning and Operation Guidelines
These general cleaning and operation guidelines are recommended for all fiber optic products. Users should still follow specific guidelines for an individual product as outlined in the support documentation or manual. Damage threshold calculations only apply when all appropriate cleaning and handling procedures are followed.
-
All light sources should be turned off prior to installing or integrating optical fibers (terminated or bare). This ensures that focused beams of light are not incident on fragile parts of the connector or fiber, which can possibly cause damage.
-
The power-handling capability of an optical fiber is directly linked to the quality of the fiber/connector end face. Always inspect the fiber end prior to connecting the fiber to an optical system. The fiber end face should be clean and clear of dirt and other contaminants that can cause scattering of coupled light. Bare fiber should be cleaved prior to use and users should inspect the fiber end to ensure a good quality cleave is achieved.
-
If an optical fiber is to be spliced into the optical system, users should first verify that the splice is of good quality at a low optical power prior to high-power use. Poor splice quality may increase light scattering at the splice interface, which can be a source of fiber damage.
-
Users should use low power when aligning the system and optimizing coupling; this minimizes exposure of other parts of the fiber (other than the core) to light. Damage from scattered light can occur if a high power beam is focused on the cladding, coating, or connector.
Tips for Using Fiber at Higher Optical Power
Optical fibers and fiber components should generally be operated within safe power level limits, but under ideal conditions (very good optical alignment and very clean optical end faces), the power handling of a fiber component may be increased. Users must verify the performance and stability of a fiber component within their system prior to increasing input or output power and follow all necessary safety and operation instructions. The tips below are useful suggestions when considering increasing optical power in an optical fiber or component.
-
Splicing a fiber component into a system using a fiber splicer can increase power handling as it minimizes possibility of air/fiber interface damage. Users should follow all appropriate guidelines to prepare and make a high-quality fiber splice. Poor splices can lead to scattering or regions of highly localized heat at the splice interface that can damage the fiber.
-
After connecting the fiber or component, the system should be tested and aligned using a light source at low power. The system power can be ramped up slowly to the desired output power while periodically verifying all components are properly aligned and that coupling efficiency is not changing with respect to optical launch power.
-
Bend losses that result from sharply bending a fiber can cause light to leak from the fiber in the stressed area. When operating at high power, the localized heating that can occur when a large amount of light escapes a small localized area (the stressed region) can damage the fiber. Avoid disturbing or accidently bending fibers during operation to minimize bend losses.
-
Users should always choose the appropriate optical fiber for a given application. For example, large-mode-area fibers are a good alternative to standard single mode fibers in high-power applications as they provide good beam quality with a larger MFD, decreasing the power density on the air/fiber interface.
-
Step-index silica single mode fibers are normally not used for ultraviolet light or high-peak-power pulsed applications due to the high spatial power densities associated with these applications.
Posted Comments: | |
basrak
 (posted 2019-01-01 20:24:30.517) I am interested in the THORLABS Bifurcated Fiber Bundles (BFB's) with 19 fibers (19-Fiber Y-Bundles). Is it possible to produce a BFB which on the 19 fibers leg terminates by a standard FC/PC connector instead by the usual SMA905 connector? If that is feasible, how much such a modified item BF19Y2LS02 (i.e. with fiber FG200LEA) will cost? YLohia
 (posted 2019-01-02 08:32:31.0) Hello, thank you for contacting Thorlabs. Unfortunately, FC/PC connectors cannot support any more than two fibers on the common end due the the stress imposed on its springs, so this cannot be produced. If you would like to inquire about any other customization, please email techsupport@thorlabs.com for a quote. |

Item # | Hydroxyl Content |
Wavelength Range |
Fiber Item # |
# of Fibers |
Core Diameter |
Cladding Diameter |
NA | Minimum Bend Radius | Common End Face Drawingc |
9-Fiber End Drawingc |
10-Fiber End Drawingc |
|
---|---|---|---|---|---|---|---|---|---|---|---|---|
Short Term | Long Termb | |||||||||||
BF19Y2HS02 | High OH | 250 - 1200 nma | FG200UEA | 19 | 200 µm ± 2% | 220 ± 2 µm | 0.22 ± 0.02e | 6.5 cm | 13 cm | ![]() |
![]() |
![]() |
BF19Y2LS02 | Low OH | 400 - 2400 nm | FG200LEA |

- Connect Fiber Bundles to our Fiber Light Source
- SM1SMA Allows SMA Terminated Bundles to be the Output of our Current OSL2 Light Source
- OSL1-SMA Allows SMA Terminated Bundles to be the Output of our Former OSL1 Light Source
Thorlabs’ SM1SMA and OSL1-SMA Fiber Connector Adapters allow SMA terminated fiber bundles to be the output of our OSL2 and former OSL1 Fiber Light Sources, respectively. Our fiber bundles with SMA connectors offer lower attenuation than the fiber bundle included with the former OSL1 and the current OSL2YFB bifurcated fiber bundle, and they are available in longer lengths.
The SM1SMA adapter plate can be attached to the front SM1-threaded (1.035"-40) output port of the OSL2 light source. The fiber bundle adapter that comes preinstalled on the OSL2 must first be removed by unscrewing it from the output port before attaching the SM1SMA. The OSL1-SMA adapter inserts into the front panel of the former OSL1 unit and is secured by a thumbscrew. They are both compatible with SMA905- and SMA906-style connectors.
Note: The OSL1-SMA is not compatible with our current OSL2 light source.