Single-Axis Scanning Galvo Systems, ±22.5° Scan Angle
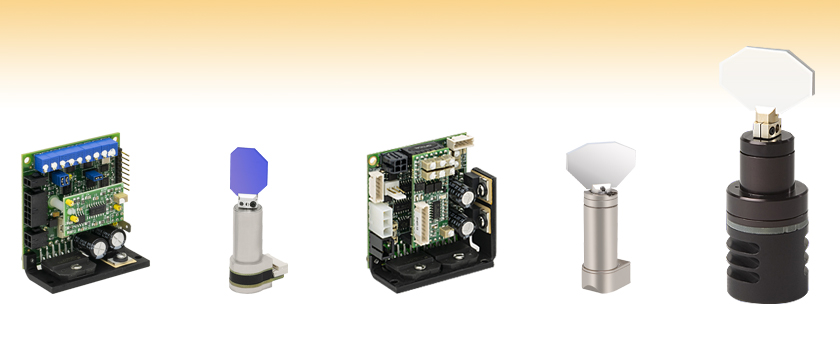
- 22.5° Scan Angle and Beam Diameters up to 45 mm
- Choice of Broadband Protected Silver or Nd:YAG Mirror Coatings
- Easy to Integrate with OEM Systems
- Analog Control Electronics
Servo Driver Included with
Galvo Scanners for
Ø7 or Ø10 mm Beams
QS10Y-Y3
Vertical Mirror for Ø10 mm Beams,
Dielectric Nd:YAG Coating
Servo Driver Included with
Galvo Scanners for
Ø15 to Ø45 mm Beams
QS15X-AG
Horizontal Mirror for Ø15 mm Beams,
Protected Silver Coating
QS30X-AG
Horizontal Mirror for
Ø30 mm Beams,
Protected Silver
Coating

Please Wait
Single-Axis Galvo Scanner Selection Guide | |||||
---|---|---|---|---|---|
Item # Prefix (X- or Y-Axis) |
Mirror Coatingsa | Max Beam Diameter |
Position Detector |
||
-AG | -Y3 | -Y1 | |||
QS7(X)(Y) | ![]() |
- | - | 7 mm | Optical |
QS10(X)(Y) | - | ![]() |
![]() |
10 mm | |
QS15(X)(Y) | ![]() |
![]() |
![]() |
15 mm | |
QS20(X)(Y) | ![]() |
![]() |
![]() |
20 mm | |
QS30(X)(Y) | ![]() |
- | ![]() |
30 mm | Capacitive |
QS45(X)(Y) | ![]() |
- | ![]() |
45 mm | |
Power Supply & Command Cables |
Applications
- Laser Marking
- Additive Manufacturing
- Laser Engraving
- Welding
- Micromachining
- Laser Drilling
- Ablation/Surface Texturing
- Cutting/Scribing
- Laser Scanning Microscopy
- Laser Projection
Large-Volume Orders
For orders where a large quantity of an item is purchased and the delivery of that item is scheduled with our production (i.e., not taken directly from inventory), Thorlabs passes on to the customer the cost savings associated with planned production of high volumes of that item. Since the volume and planned production are key to realizing the cost savings, we ask that you contact us to obtain volume pricing.
Additional requests can include custom optic sizes and coatings, specialized tuning, and variable cable options.
Features
- Moving Magnet Motor Design for Fast Response (250 µs for 0.4° Optical with a Mirror for Ø7 mm Beams)
- High-Precision Optical or Capacitive Mirror Position Detection (See Table to the Right for Details)
- Three Mirror Coatings Available:
- Protected Silver, 450 to 10.6 µm
- Nd:YAG Laser, 3rd Harmonic, 355 nm
- Nd:YAG Laser, 1064 nm
- High Reflectance at 633 nm for Alignment Laser
- Analog PID Control Electronics with Current Damping
- 24" (610 mm) Drive Cable Included
- Power Supply, Power Cables, and Command Cables Available Separately
- Custom Coatings Available upon Request (Contact Tech Support for More Details)
These high-speed scanning galvanometer mirror positioning systems are designed for integration into OEM or custom laser beam steering applications. Models are available for beam diameters up to 45 mm. Each system includes a single-axis galvo motor with mirror and a matched driver card. Dimensions and mounting features can be accessed by clicking on the red docs icon () next to the Item # below. The mirror/motor assembly can be mounted using a clamp to hold the servo shaft. A compatible power supply and command cable(s) are sold separately below. The user must provide a function generator or other analog voltage output device in order to operate the servo drivers. The mirrors are offered with one of three coatings, as shown in the table to the right. Custom coatings are available upon request. Please contact Tech Support for more details. We also offer dual-axis systems that use these scan heads.
Servo Driver Board
These closed-loop servo drivers interpret the signals from the position detecting system inside the motor and produce the drive voltage required to rotate the mirror to the desired position. High bandwidth ensures following of analog command waveforms with speed and accuracy.
Both drivers feature proportional-integral-derivative (PID) servo driver circuits with advanced current damping for high performance. The drivers incorporate low-noise components to maximize the signal-to-noise ratio for better accuracy and low-drift components to reduce the effects of temperature variation. A notch filter is selected and tuned for each unique mirror-galvo combination to maximize system bandwidth for faster, more accurate scanning. These systems are ideal for use in applications including step-and-hold positioning, vector positioning (e.g., laser marking), and raster positioning (printing or scanning laser microscopy).
Servos are optimized for high-speed, precise positioning for all applications. Servos for scanners with ≥15 mm maximum beam diameters additionally feature dual-output power amplifiers to keep power supply requirements modest for larger motors without sacrificing performance. Servo driver circuits provide soft start/stop operation, open circuit AGC fail, and over/under-voltage protections. Onboard status LEDs indicate servo status and fault conditions and a diagnostic port provides position, velocity, error, and current information. Each driver-galvo-mirror set is tested and tuned to specification. The unique serial number of the galvo is noted on its associated driver board. Note that the X and Y drivers are matched to their respective servos and are not interchangeable.
Galvo Scanner Specs | |||||||
---|---|---|---|---|---|---|---|
Item # Prefix | QS7X QS7Y |
QS10X QS10Y |
QS15X QS15Y |
QS20X QS20Y |
QS30X QS30Y |
QS45X QS45Y |
|
Max Beam Diameter | 7 mm | 10 mm | 15 mm | 20 mm | 30 mm | 45 mm | |
Mirror Substrate | Fused Silica | Silicon Carbide | |||||
Step Response Time (0.4° Optical) | 250 µs | 350 µs | 600 µs | 650 µs | 1200 µs | 1000 µs | |
Mechanical and Electrical Specs | |||||||
Rated Excursion | ±22.5° Opticala | ||||||
Rotor Inertial Load |
Recommended | 0.17 g·cm2 | 1.8 g·cm2 | 5.1 g·cm2 | |||
Max | 0.85 g·cm2 | 9 g·cm2 | 25 g·cm2 | ||||
Torque Constant | 40 000 dyne·cm/A | 180 000 dyne·cm/A | 280 000 dyne·cm/A | ||||
Coil Resistance | 1.3 Ω | 3.0 Ω | 5.8 Ω | ||||
Coil Inductance | 76 µH @ 1 kHz | 530 µH @ 1 kHz | 450 µH @ 1 kHz | ||||
Position Detector | |||||||
Type | Optical | Capacitive | |||||
Linearity | 99.8% @ ±20° | >99.9% | |||||
Gain Drift | 50 ppm/°C | 50 ppm/°C | |||||
Offset Drift | 30 µrad/°C | 40 µrad/°C | |||||
Repeatability | 10 µrad | 15 µrad | |||||
Output Signal (Typ.) |
Differential Mode | 7.1 µA/° Optical | 40 µA/° Optical | ||||
Common Mode | 385 µA | 2100 µA | |||||
Supply Current | 30 - 40 mA | 10 - 20 mA | |||||
General Specs | |||||||
Operating Temperature | 0 to 40 °C (Non-Condensing) | ||||||
Storage Temperature | -10 to 50 °C | ||||||
Servo Shaft Size | Ø14 mm x 26.3 mm | Ø22 mm x 50 mm | Ø30.5 mm x 30 mm | ||||
Mass (Without Cable) | 36 g | 128 g | 306 g |
Mirror Coating Specs | |||
---|---|---|---|
Item # Suffix | -AG | -Y3 | -Y1 |
Coating Type | Protected Silver | Hard Dielectric for Nd:YAG Laser 3rd Harmonic |
Hard Dielectric for Nd:YAG Laser Fundamental |
Absolute Reflectance |
≥92% (450 - 500 nm) ≥94.5% (500 - 2000 nm) ≥98% (2 - 10.6 µm) |
≥99% (355 nm) ≥80% (633 nm) |
≥98% (1064 nm) ≥80% (633 nm) |
Surface Quality (Scratch-Dig) |
40-20 | 20-10 | 40-20 |
Servo Amplifier Specsa | ||
---|---|---|
Item # Prefix | QS7(X)(Y) QS10(X)(Y) |
QS15(X)(Y) QS20(X)(Y) QS30(X)(Y) QS45(X)(Y) |
Inputs | ||
Command Input Range | ±5 V | |
Position Input Scale Factor | 0.22 V/° Optical | |
Command Input Impedance | 400 kΩ (Differential) 200 kΩ (Single Ended) |
20 kΩ ± 1% (Differential) 10 kΩ ± 1% (Single Ended) |
Position Offset Range | ±0.25 V | |
External Enable | TTL (Low: Disable Drive) | See Footnote b for Details |
Diagnostic Outputs | ||
Servo Ready | TTL | 12 V |
Position | 0.22 V/° Optical | |
Position Error | 0.22 V/° Optical | |
Velocity | Analog (Reference Only) | |
AGC Voltage | Analog (DC) | |
Coil Current | 1 V/A | |
Analog Output Impedance | Unbuffered | 1 kΩ ± 1% (For All Outputs) |
Power Supply (Not Included) | ||
Input Voltage | ±15 VDC <100 mV Ripple <0.5% DC to 30 MHz Noise |
±15 to ±24 VDC <100 mV Ripple <0.5% DC to 30 MHz Noise |
Maximum Drive Current Limit | 3 A (RMS); 10 A (Peak) | 4 A (RMS); 10 A (Peak) |
Quiescent Current | 220 mA (Servo Enabled, Galvo at Rest) | |
Gain Drift | Up to 20 ppm/°C | |
Offset Drift | Up to 26 µrad/°C | Up to 30 µrad/°C |
General Specs | ||
Operating Temperature | 0 to 45 °C (With Appropriate Cooling) | |
Storage Temperature | -10 to 60 °C | |
Dimensions | 2.38" x 2.22" x 1.06" (60.5 mm x 56.4 mm x 27.0 mm) |
2.38" x 2.13" x 1.06" (60.5 mm x 54.1 mm x 27.0 mm) |
Mass (Weight) | 49 g (1.7 oz) | 74 g (2.6 oz) |

Galvo Motor/Mirror Assembly
The galvo consists of a galvanometer-based scanning motor with an optical mirror mounted on the shaft and a detector that provides positional feedback to the control board. The moving magnet design for the QS series of galvanometer motors was chosen over a stationary magnet and rotating coil design in order to provide the fastest response times and the highest system resonant frequency. The position of the mirror is encoded using an optical or capacitive sensing system located inside of the motor housing.
Due to the large angular acceleration of the rotation shaft, the size, shape, and inertia of the mirrors become significant factors in the design of high-performance galvo systems. Furthermore, the mirror must remain rigid (flat) even when subjected to large accelerations. All these factors have been precisely balanced in our galvo systems in order to match the characteristics of the galvo motor and maximize performance of the system.
The galvo mirrors are secured to the motor/mirror assembly by a flexure clamp. The positions of the mirror holders are set at the factory and should not be changed by the user.
System Operation
The servo driver must be connected to a DC power supply, the galvo motor, and an input voltage source (the monitoring connection is optional). For continuous scanning applications, a function generator with a square or sine wave output is sufficient for scanning the galvo mirror over its entire range. For more complex scanning patterns, a programmable voltage source such as a DAQ card can be used. User-generated motion trajectories with smooth acceleration profiles are preferred; uncontrolled steps should be avoided if possible. Please note that these systems do not include a power supply (sold separately below), function generator, or DAQ card. The drivers below are factory configured for a 0.22 V/° ratio between the input voltage and mirror position, as well as an input voltage of ±5 VDC. Drivers configured for 0.44 V/° and ±10 VDC are available upon request; please contact Tech Support. The control circuit also provides monitoring outputs that allow the user to track the position of the mirror. In addition, voltages proportional to the drive current being supplied to the motor and the difference between the command position and the actual position of the mirror are supplied by the control circuit.
Closed-Loop Mirror Positioning
The angular orientation (position) of the mirror is measured using an optical or capacitive sensing system, which is integrated into the interior of the galvanometer housing, and allows for the closed-loop operation of the galvo mirror system.
Posted Comments: | |
No Comments Posted |

Key Specsa | ||||||||
---|---|---|---|---|---|---|---|---|
Item # | Mirror Orientation |
Mirror Coating | Max Beam Diameter | Position Detector |
Rated Excursion | Recommended Rotor Inertial Load |
Step Response Time | Housing Diameter |
QS7X-AG | Horizontal | Protected Silver: Rabs ≥ 92% (450 - 500 nm) Rabs ≥ 94.5% (500 - 2000 nm) Rabs ≥ 98% (2 - 10.6 µm) |
7 mm | Optical | ±22.5° Optical | 0.17 g·cm2 | 250 µs | 14 mm |
QS7Y-AG | Vertical |
Each system includes a galvo scan head, driver board, and drive cable. A compatible GPWR15 Power Supply and CBLS2F Command and Power Cables can be purchased separately below.

Key Specsa | ||||||||
---|---|---|---|---|---|---|---|---|
Item # | Mirror Orientation |
Mirror Coating | Max Beam Diameter | Position Detector |
Rated Excursion | Recommended Rotor Inertial Load |
Step Response Time | Housing Diameter |
QS10X-Y3 | Horizontal | Nd:YAG Laser, 3rd Harmonic: Rabs ≥ 99% (355 nm) Rabs ≥ 80% (633 nm) |
10 mm | Optical | ±22.5° Optical | 0.17 g·cm2 | 350 µs | 14 mm |
QS10Y-Y3 | Vertical | |||||||
QS10X-Y1 | Horizontal | Nd:YAG Laser: Rabs ≥ 98% (1064 nm) Rabs ≥ 80% (633 nm) |
||||||
QS10Y-Y1 | Vertical |
Each system includes a galvo scan head, driver board, and drive cable. A compatible GPWR15 Power Supply and CBLS2F Command and Power Cables can be purchased separately below.

Key Specsa | ||||||||
---|---|---|---|---|---|---|---|---|
Item # | Mirror Orientation |
Mirror Coating | Max Beam Diameter | Position Detector |
Rated Excursion | Recommended Rotor Inertial Load |
Step Response Time | Housing Diameter |
QS15X-AG | Horizontal | Protected Silver: Rabs ≥ 92% (450 - 500 nm) Rabs ≥ 94.5% (500 - 2000 nm) Rabs ≥ 98% (2 - 10.6 µm) |
15 mm | Optical | ±22.5° Optical | 1.8 g·cm2 | 600 µs | 22 mm |
QS15Y-AG | Vertical | |||||||
QS15X-Y3 | Horizontal | Nd:YAG Laser, 3rd Harmonic: Rabs ≥ 99% (355 nm) Rabs ≥ 80% (633 nm) |
||||||
QS15Y-Y3 | Vertical | |||||||
QS15X-Y1 | Horizontal | Nd:YAG Laser: Rabs ≥ 98% (1064 nm) Rabs ≥ 80% (633 nm) |
||||||
QS15Y-Y1 | Vertical |
Each system includes a galvo scan head, driver board, and drive cable. A compatible GPWR15 Power Supply and CBLS3F Command and Power Cables can be purchased separately below.

Key Specsa | ||||||||
---|---|---|---|---|---|---|---|---|
Item # | Mirror Orientation |
Mirror Coating | Max Beam Diameter | Position Detector |
Rated Excursion | Recommended Rotor Inertial Load |
Step Response Time | Housing Diameter |
QS20X-AG | Horizontal | Protected Silver: Rabs ≥ 92% (450 - 500 nm) Rabs ≥ 94.5% (500 - 2000 nm) Rabs ≥ 98% (2 - 10.6 µm) |
20 mm | Optical | ±22.5° Optical | 1.8 g·cm2 | 650 µs | 22 mm |
QS20Y-AG | Vertical | |||||||
QS20X-Y3 | Horizontal | Nd:YAG Laser, 3rd Harmonic: Rabs ≥ 99% (355 nm) Rabs ≥ 80% (633 nm) |
||||||
QS20Y-Y3 | Vertical | |||||||
QS20X-Y1 | Horizontal | Nd:YAG Laser: Rabs ≥ 98% (1064 nm) Rabs ≥ 80% (633 nm) |
||||||
QS20Y-Y1 | Vertical |
Each system includes a galvo scan head, driver board, and drive cable. A compatible GPWR15 Power Supply and CBLS3F Command and Power Cables can be purchased separately below.

Key Specsa | ||||||||
---|---|---|---|---|---|---|---|---|
Item # | Mirror Orientation |
Mirror Coating | Max Beam Diameter | Position Detector |
Rated Excursion | Recommended Rotor Inertial Load |
Step Response Time | Housing Diameter |
QS30X-AG | Horizontal | Protected Silver: Rabs ≥ 92% (450 - 500 nm) Rabs ≥ 94.5% (500 - 2000 nm) Rabs ≥ 98% (2 - 10.6 µm) |
30 mm | Optical | ±22.5° Optical | 5.1 g·cm2 | 1200 µs | 30.5 mm |
QS30Y-AG | Vertical | |||||||
QS30X-Y1 | Horizontal | Nd:YAG Laser: Rabs ≥ 98% (1064 nm) Rabs ≥ 80% (633 nm) |
||||||
QS30Y-Y1 | Vertical |
Each system includes a galvo scan head, driver board, and drive cable. A compatible GPWR15 Power Supply and CBLS3F Command and Power Cables can be purchased separately below.

Key Specsa | ||||||||
---|---|---|---|---|---|---|---|---|
Item # | Mirror Orientation |
Mirror Coating | Max Beam Diameter | Position Detector |
Rated Excursion | Recommended Rotor Inertial Load |
Step Response Time | Housing Diameter |
QS45X-AG | Horizontal | Protected Silver: Rabs ≥ 92% (450 - 500 nm) Rabs ≥ 94.5% (500 - 2000 nm) Rabs ≥ 98% (2 - 10.6 µm) |
45 mm, Converging |
Optical | ±22.5° Optical | 5.1 g·cm2 | 1000 µs | 30.5 mm |
QS45Y-AG | Vertical | |||||||
QS45X-Y1 | Horizontal | Nd:YAG Laser: Rabs ≥ 98% (1064 nm) Rabs ≥ 80% (633 nm) |
||||||
QS45Y-Y1 | Vertical |
Each system includes a galvo scan head, driver board, and drive cable. A compatible GPWR15 Power Supply and CBLS3F Command and Power Cables can be purchased separately below.

- GPWR15: ±15 V Power Supply for QS Series Galvo Scanners (Single- and Dual-Axis Systems; One Supply Can Power up to Two Galvos)
- Input: 100-120 or 220-240 VAC
- Output: ±15 V @ 5 A (150 W Max Power)
- Operating Temperature: 0 to 50 °C
- Dimensions: 14.0" x 4.9" x 3.5" (356 mm x 124 mm x 90 mm)
- CBLS2F: Command and Power Cables for QS7 and QS10 Series Galvo Scanners (One Set Required per Axis)
- CBLS3F: Command and Power Cables for QS15/20/30/45 Series Galvo Scanners (One Set Required per Axis)