Polaris® Side Optic Retention Mounts for Ø1" Optics
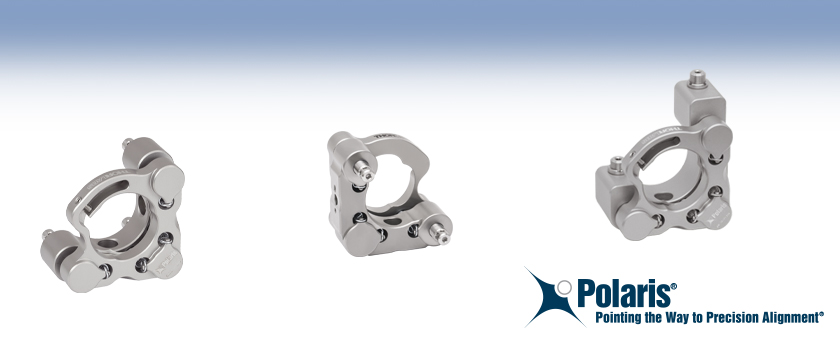
- Designed for Long-Term Stability
- Matched Actuator and Back Plate Threading Minimize Drift and Backlash
- Minimal Temperature-Dependent Hysteresis
- Sapphire Adjuster Seats Prevent Wear Over Time
POLARIS-K1S4
2-Adjuster Mirror Mount
POLARIS-K1S5
3-Adjuster Mirror Mount
POLARIS-K1VS2
2-Adjuster Mirror Mount, Vertical Drive

Please Wait
Quick Links | |
---|---|
3-Adjuster Mounts | |
2-Adjuster Mounts | |
2-Adjuster Mount, Vertical Drive | |
Adjuster Knobs | |
Side Hole Adjustment Tool | |
Lock Nut | |
Locking Collar | |
Torque Wrench |

Click to Enlarge
Each Polaris mount undergoes extensive thermal testing to ensure high-quality performance. Please see the Test Data tab for additional test results.
Features
- Machined from Heat-Treated Stainless Steel with Low Coefficient of Thermal Expansion (CTE)
- Hardened Stainless Steel Ball Contacts with Sapphire Seats for Durability and Smooth Movement
- Matched Actuator and Back Plate Provide Stability and Smooth Kinematic Adjustment
- POLARIS-K1 and POLARIS-K1-H Have Bronze Bushing Inserts
- Extensive Testing Guarantees Less than 2 μrad Deviation after 12.5 °C Temperature Cycling (See Test Data Tab for Details)
- Passivated Stainless Steel Surface Ideal for Vacuum and High-Power Laser Cavity Applications (Except POLARIS-K1 and POLARIS-K1-H)
- Custom Mount Configurations are Available by Contacting Tech Support
- Patented Optic Bore Design with Monolithic Flexure Arm (US Patent 10,101,559 for POLARIS-K1S4, POLARIS-K1S5, and POLARIS-K1VS2)
Polaris® Low-Drift Kinematic Mirror Mounts are the ultimate solution for applications requiring stringent long-term alignment stability.
Optic Retention
The POLARIS-K1S5, POLARIS-K1S4, and POLARIS-K1VS2 feature a patented optic bore design with a monolithic flexure arm, while the POLARIS-K1, POLARIS-K1-H, and POLARIS-K1-2AH use a flexure spring and setscrew combination to hold the optic. These designs provide high holding force and pointing stability with minimal optic distortion. For more details, please see the Test Data tab.
Polaris optic bores are precision machined to achieve a fit that will provide optimum beam pointing stability over changing environmental conditions such as temperature changes, transportation shock, and vibration. Performance will be diminished if a Ø1" mount is used with a Ø25 mm optic or an optic with an outer diameter tolerance greater than zero. See our Ø25 mm Polaris mount if you require a mount that is compatible with Ø25 mm optics.
Polaris® Side Optic Retention Mounts Selection Guide |
---|
Ø1/2" Optic Mounts |
Ø19 mm Optic Mount |
Ø25 mm Optic Mount |
Ø1" Optic Mounts |
Ø1.5" Optic Mount |
Ø50 mm Optic Mount |
Ø2" Optic Mounts |
Ø3" Optic Mounts |
Design
Machined from heat-treated stainless steel, Polaris mounts utilize precision-matched adjusters with ball contacts and sapphire seats to provide smooth kinematic adjustment. As shown on the Test Data tab, these mounts have undergone extensive testing to ensure high-quality performance. The Polaris design addresses all of the common causes of beam misalignment; please refer to the Design Features tab for detailed information.
Post Mounting
The Polaris mirror mounts are equipped with #8 (M4) counterbores for post mounting. Select mounts also include Ø2 mm alignment pin holes around the mounting counterbore, allowing for precision alignments when paired with our posts for Polaris mirror mounts. See the Usage Tips tab for more recommendations about mounting configurations.
Cleanroom and Vacuum Compatibility
All our Polaris mounts except the POLARIS-K1 and POLARIS-K1-H are designed to be compatible with cleanroom and vacuum applications. See the Specs tab and the Design Features tab for details. The POLARIS-K1 and POLARIS-K1-H are also available in vacuum-compatible versions as a custom order. Please contact Tech Support for custom orders.
Item # Suffixa | -K1 | -K1H | -K1-2AH | -K1S5 | -K1S4 | -K1VS2 |
---|---|---|---|---|---|---|
Optic Sizeb | Ø1" | |||||
Optic Thickness (Min) | 0.08" (2 mm) | 0.14" (3.5 mm) | ||||
Number of Adjusters | Three | Two | Three | Two | ||
Adjuster Drive | Removable Knobs |
Low-Profile 5/64" Hex |
Low-Profile 5/64" Hex |
5/64" Hex, Ø0.07" Side Adjustment Holes | Vertical Drive 5/64" Hex |
|
Adjuster Pitch | 100 TPI | |||||
Actuator Matching | Matched Actuator/Bushing Pairs | Matched Actuator/Body Pairs | ||||
Measured Point-to-Point Mechanical Resolution per Adjuster (Bidirectional Repeatability) |
5 µrad (Typical); 2 µrad (Achievable) | |||||
Adjustment per Revolutionc | ~7 mrad/rev | ~7.7 mrad/rev | ||||
Front Plate Translation (Max) | 6 mm | N/A | 6 mm | N/A | ||
Mechanical Angular Range (Nominal) | ±4° | |||||
Front Plate Separation at Pivot Adjuster | 3.175 mm (Nominal) | 3.175 mm | 3.175 mm (Nominal) | 3.175 mm | ||
Beam Deviationd After Thermal Cycling | <2 μrad | <1 μrad | ||||
Recommended Optic Mounting Torquee | 6 - 10 oz-in for 6 mm Thick UVFS Optics | 5 - 7 oz-in for 6 mm Thick UVFS Optics | ||||
Mounting | Two #8 (M4) Counterbores | One #8 (M4) Counterbore | ||||
Alignment Pin Holes | None | Two at Each Counterboref | ||||
Vacuum Compatibilityg | Noh | 10-9 Torr at 25 °C with Proper Bake Out 10-5 Torr at 25 °C without Bake Out Grease Vapor Pressure:10-13 Torr at 20 °C; 10-5 Torr at 200 °C |
||||
Operating Temperature Range | -30 to 200 °C |
Polaris Mirror Mounts Test Data
All of the Polaris Low-Drift Kinematic Mirror Mounts have undergone extensive testing to ensure high-quality performance. Thermal Shock testing confirms the exceptional stability of the mounts and demonstrates that they reliably return to their initial position after a transient temperature shift. Interferometric wavefront distortion testing demonstrates the ability of Polaris mounts to secure an optic without significantly distorting the optical surface.
Vibration Testing for Polaris Mounts (Ø19 mm Polaris Mount Shown)
Vibration Testing
Purpose: This testing was done to determine how reliably Polaris mirror mounts behave when subjected to intense physical vibrations.
Procedure: A pair of identical POLARIS-K1S4 mirror mounts were mounted on Ø1" Posts for Polaris Mirror Mounts and secured to a stainless steel breadboard with POLARIS-CA1 clamping arms. Laser beams were reflected from the mirrors onto two position sensing detectors, located on the same breadboard. The entire platform was vibrated with a variable frequency and amplitude and the displacement of the beam on the detector was recorded. The two beam paths were oriented at right angles so that the vibrational motion was in a direction parallel to the face of one mount and perpendicular to the face of the other. Please see the video to the right for a demonstration of our Polaris vibration test (the mount shown in the video is the POLARIS-K19S4).
Results: When subjected to vibrational frequencies as high as 100 Hz and accelerations as high as 6 g, the POLARIS-K1S4 mounts remained mechanically sound. The angular position of the mounts remained stable within about 10 µrad for both parallel and perpendicular vibrations.
Conclusions: Our POLARIS-K1S4 Ø1" Polaris mirror mounts provide exceptional performance, even under rugged operating conditions. As a result, these mounts are ideal for use in systems that require the greatest degree of stability when vibrational noise is expected.
Positional Repeatability After Thermal Shock
Purpose: This testing was done to determine how reliably the mount returns the mirror, without hysteresis, to its initial position. These measurements show that the alignment of the optical system is unaffected by the temperature shock.
Procedure: After mounting the Polaris to a Ø1" Post, the mirror and post assembly was secured to a stainless steel optical table in a temperature-controlled environment. The mirror was held using the flexure mechanism; see the Usage Tips tab for additional mounting recommendations. A beam from an independently temperature-stabilized laser diode was reflected by the mirror onto a position sensing detector. The temperature of each mirror mount tested was raised to at least 37 °C. The elevated temperature was maintained in order to soak the mount at a constant temperature. Then the temperature of the mirror mount was returned to the starting temperature. The results of these tests are shown below.
Results: As can be seen in the plots below, when the Polaris mounts were returned to their initial temperature, the angular position (both pitch and yaw) of the mirrors returned to within 2 µrad (1 µrad for the monolithic retention mounts) of its initial position. The best result achieved with a competitor’s mount was significantly worse than the Polaris mounts. The performance of the Polaris was tested further by subjecting the mount to repeated temperature change cycles. After each cycle, the mirror’s position reliably returned to within 1 µrad of its initial position.
For Comparison: To get a 1 µrad change in the mount’s position, the 100 TPI adjuster on the POLARIS-K1 Ø1" Polaris mount needs to be rotated by only 0.05° (1/7200 of a turn). A highly skilled operator might be able to make an adjustment as small as 0.3° (1/1200 of a turn), which corresponds to 6 µrad.
Conclusions: The Polaris Mirror Mounts are high-quality, ultra-stable mounts that will reliably return a mirror to its original position after cycling through a temperature change. As a result, the Polaris mounts are ideal for use in applications that require long-term alignment stability.
POLARIS-K1 and POLARIS-K1H 3-Adjuster Mounts, Flexure Spring Optic Retention |
---|
![]() Click to Enlarge Thermal Repeatability for Ø1", 3-Adjuster Polaris Mirror Mounts |
POLARIS-K1-2AH 2-Adjuster Mount, Flexure Spring Optic Retention |
---|
![]() Click to Enlarge Thermal Repeatability for Ø1", 2-Adjuster Polaris Mirror Mount |
POLARIS-K1S5 3-Adjuster Mount, Monolithic Optic Retention |
---|
![]() Click to Enlarge Thermal Repeatability for Ø1", 3-Adjuster Polaris Mirror Mount |
||||||||||
![]() Click to Enlarge The plot above shows the final angular position of the POLARIS-K1S5 for 10 consecutive thermal shock tests. The change in temperature is the difference between the starting temperature and the temperature at the end of the test and includes factors such as the variation in room and mount temperature. |
POLARIS-K1S4 2-Adjuster Mount, Monolithic Optic Retention |
---|
![]() Click to Enlarge Thermal Repeatability for Ø1", 2-Adjuster Polaris Mirror Mount |
||||||||||
![]() Click to Enlarge The plot above shows the final angular position of the POLARIS-K1S4 for 10 consecutive thermal shock tests. The change in temperature is the difference between the starting temperature and the temperature at the end of the test and includes factors such as the variation in room and mount temperature. |
POLARIS-K1VS2 2-Adjuster Mount, Monolithic Optic Retention, Vertical Drive |
---|
![]() Click to Enlarge Thermal Repeatability for Ø1", 2-Adjuster Polaris Mirror Mount |
||||||||||
![]() Click to Enlarge The plot above shows the final angular position of the POLARIS-K1VS2 for 10 consecutive thermal shock tests. The change in temperature is the difference between the starting temperature and the temperature at the end of the test and includes factors such as the variation in room and mount temperature. |
Optical Distortion Testing Using a ZYGO Phase-Shifting Interferometer
Mounting stresses are responsible for the strain that results in optical surface distortion. Minimizing distortion effects is crucial; any distortion to the optic affects the reflected wavefront. Our Ø19 mm and Ø2" Polaris mounts, as well as select Ø1" Polaris mounts, feature a monolithic flexure arm that is designed to provide maximum stability while minimizing optic distortion.
To determine the amount of optic distortion exerted on the mirror by the flexure arm, a ZYGO Phase-Shifting Interferometer was used to measure the wavefront distortion at different torque values (see the images below to the left). Based on results of the tests seen below, we recommend a torque of 5 - 7 oz-in for our Ø1" Polaris mounts, at which the optic wavefront distortion is ≤0.1λ.
Please note that the optimal optic mounting torque can vary by ±1 oz-in due to variations in optic diameter and tolerance buildup.
Procedure:
A broadband dielectric mirror was installed into a Polaris mount using the setscrew to clamp down the flexure arm. Measurements of the optic distortion were then recorded using the ZYGO interferometer. Once each measurement was complete, the amount of force needed to push the optic out of the mount was measured to check optic retention. The wavefront distortion values shown here give peak-to-valley distortion across the entire optic, representing the worst-case scenario; the center of the optic exhibits significantly less distortion than the edge.
Results:
As seen in the table below, the peak-to-valley wavefront distortion was found to be ≤0.1λ when 5 - 7 oz-in of torque was applied to the setscrew of the POLARIS-K1S4 Ø1" mount.
Torque (oz-in)a | Push-Out Force (lbf)b | Wavefront Distortion (Peak to Valley)c (Click for Example Zygo Screenshot) |
---|---|---|
4.5 | >12 | 0.072λ to 0.093λ |
5 | 0.047λ to 0.090λ | |
5.5 | 0.057λ to 0.097λ | |
6 | 0.085λ to 0.100λ | |
6.5 | 0.057λ to 0.073λ | |
7 | 0.059λ to 0.067λ | |
7.5 | 0.083λ to 0.092λ | |
8 | 0.128λ to 0.145λ | |
8.5 | 0.102λ to 0.117λ | |
9 | 0.141λ to 0.162λ | |
10 | 0.188λ to 0.224λ |

Click to Enlarge
POLARIS-K1S4 Wavefront Distortion for Setscrew Torque of
7 oz-in (See Table to the Right for Other Setscrew Torques)

Click to Enlarge
Details of the POLARIS-K1S4 Design. Note that some mounts on this page use a flexure spring to retain the optic and have bronze bushings instead of matched actuator/body pairs.
Several common factors typically lead to beam misalignment in an optical setup. These include temperature-induced hysteresis of the mirror's position, crosstalk, drift, and backlash. Polaris mirror mounts are designed specifically to minimize these misalignment factors and thus provide extremely stable performance. Hours of extensive research, multiple design efforts using sophisticated design tools, and months of rigorous testing went into choosing the best components to provide an ideal solution for experiments requiring ultra-stable performance from a kinematic mirror mount.
Thermal Hysteresis
The temperature in most labs is not constant due to factors such as air conditioning, the number of people in the room, and the operating states of equipment. Thus, it is necessary that all mounts used in an alignment-sensitive optical setup be designed to minimize any thermally induced alignment effects. Thermal effects can be minimized by choosing materials with a low coefficient of thermal expansion (CTE), like stainless steel. However, even mounts made from a material with a low CTE do not typically return the mirror to its initial position when the initial temperature is restored. All the critical components of the Polaris mirror mounts are heat treated prior to assembly since this process removes internal stresses that can cause a temperature-dependent hysteresis. As a result, the alignment of the optical system will be restored when the temperature of the mirror mount is returned to the initial temperature.
The method by which the mirror is secured in the mount is another important design factor for the Polaris; these Polaris mounts offer excellent performance without the use of adhesives. Instead, they use a flexure spring that is pressed onto the edge of the mirror using a setscrew. Setscrews, when used by themselves to hold an optic, tend to move as the temperature changes. In contrast, the holding force provided by the stainless steel flat spring is sufficient to keep the mirror locked into place regardless of the ambient temperature. The POLARIS-K1S4, POLARIS-K1S5, and POLARIS-K1VS2 use a monolithic flexure arm to hold the edge of the optic, further reducing both sensitivity to fluctuations in temperature and distortion on the optic surface.
Crosstalk
Crosstalk is minimized by carefully controlling the dimensional tolerances of the front and back plates of the mount so that the pitch and yaw actuators are orthogonal. In addition, sapphire seats are used at all three contact points. Standard metal-to-metal actuator contact points will wear down over time. The polished sapphire seats of the Polaris mounts, in conjunction with the hardened stainless steel actuator tips, maintain the integrity
of the contact surfaces over time.
Drift and Backlash
In order to minimize the positional drift of the mirror mount and backlash, it is necessary to limit the amount of play in the adjuster as well as the amount of lubricant used. When an adjustment is made to the actuator, the lubricant will be squeezed out of some spaces and built up in others. This non-equilibrium distribution of lubricant will slowly relax back into an equilibrium state. However, in doing so, this may cause the position of the front plate of the mount to move. The Polaris mounts use adjusters matched to the body or bushings that exceed all industry standards so very little adjuster lubricant is needed. As a result, alignment of the Polaris mounts is extremely stable even after being adjusted (see the Test Data tab for more information). In addition, these adjusters have a smooth feel that allows the user to make small, repeatable adjustments.

Click to Enlarge
All Vacuum Compatible Polaris Mounts are Shipped Inside Two Vacuum Bag Layers
Cleanroom and Vacuum Compatibility
All our Polaris mounts except the POLARIS-K1 and POLARIS-K1-H are designed to be compatible with cleanroom and vacuum applications. Vacuum compatible mounts are chemically cleaned using the Carpenter AAA passivation method to remove sulfur, iron, and contaminants from the surface. After passivation, they are assembled in a clean environment and double vacuum bagged to eliminate contamination when transported into a cleanroom.
All vacuum compatible Polaris mounts have sapphire contacts bonded into place using a NASA-approved low outgassing procedure. In addition, DuPont Krytox® LVP High-Vacuum Grease, an ultra-high-vacuum-compatible, low outgassing PTFE grease, is applied to the adjusters. Please note that the 8-32 and M4 cap screws included with the Polaris mounts are not rated for pressures below 10-5 Torr.
Each vacuum-compatible Polaris mount is packaged within two vacuum bag layers after assembly in a clean environment, as seen in the image to the right. These vacuum bags do not contain any desiccant materials and tightly wrap the mount, preventing friction against the mount during shipping. This packing method protects the mount from corrosion, gas or liquid contamination, and particulates during transport. The first vacuum bag should be opened in a clean environment while the second vacuum bag should only be opened just prior to installation. When operating at pressures below 10-5 Torr, we highly recommend using an appropriate bake out procedure prior to installing the mount in order to minimize contamination caused by outgassing.
The POLARIS-K1 and POLARIS-K1-H can also be provided with vacuum treated components, low-outgassing grease, and vacuum and clean-room rated packaging as a custom order. Please contact Tech Support for details.

Click to Enlarge
A POLARIS-K05 mount can be mounted to a surface using a Ø1" Post for Polaris Mirror Mounts and a Polaris Clamping Arm. Using a 1.50" long post, the optical axis is 2.0" above the table surface.

Click to Enlarge
At zero torque, the sample mirror's flatness was λ/20 over the clear aperture (λ = 633 nm). The shaded region in this plot denotes the recommended optic mounting torque for a 6 mm thick optic in the POLARIS-K1. At higher mounting torque values, the optic distortion increases dramatically.
Through thermal changes and vibrations, the Polaris® kinematic mirror mounts are designed to provide years of use. Below are some usage tips to ensure that the mount provides optimal performance.
Match Materials
Due to its relatively low coefficient of thermal expansion, stainless steel was chosen as the material from which to fabricate the front and back plates of the Polaris mounts. When mounting, we recommend using components fabricated from the same material, such as our Ø1" Posts for Polaris Mirror Mounts and Polaris Clamping Arm.
Use a Wide Post
The Polaris' performance is optimized for use with our Ø1" Posts and our Polaris Clamping Arm. These posts are made of stainless steel and provide two lines of contact with the mount, which help confine the bottom of the mount during variations in the surrounding temperature, thereby minimizing potential alignment issues.
Optic Mounting
Since an optic is prone to movement within its mounting bore, all optics should be mounted with the Polaris out of the setup to ensure accurate mounting that will minimize misalignment effects. We recommend using a torque wrench when installing an optic in the Polaris mounts. Over torquing the flexure-spring optic retainer can result in dramatic surface distortions (see the graph to the left).
Front Plate’s Position
Ø1" Polaris mounts are designed to allow adjustments of up to 8°. To achieve the best performance, it is recommended that the front plate be kept as parallel as possible to the back plate. This ensures the highest stability of the adjustments.
Mount as Close to the Table’s Surface as Possible
To minimize the impact of vibrations and temperature changes, it is recommended that your setup has as low of a profile as possible. Using short posts will reduce the Y-axis translation caused by temperature variations and will minimize any movements caused by vibrations. Mount the Polaris directly onto a flat surface such as a breadboard using a 1/4"-20 to 8-32 thread adapter (AE8E25E) or M6 x 1.0 to M4 x 0.7 adapter (AE4M6M). For direct mounting, the POLARIS-K1 must have the bottom two knobs removed, as in the photo to the right. By doing so, the instability introduced by a post will be eliminated.
Polish and Clean the Points of Contact
We highly recommend that the points of contact between the mount and the post, as well as the post and the table, are clean and free of scratches or defects. For best results, we recommend using a polishing stone to clean the table’s surface and a LFG1P polishing pad for the top and bottom of the post as well as the bottom of the mount.
Use Polaris-Specific Adjustment Tools
We offer stainless steel knobs for most of our Polaris adjusters, either included with the mount or available separately. For Polaris mounts with side hole adjusters, we recommend using the SA1 Side Hole Adjustment Tool, which features a precision-fit tip designed for the side holes to allow backlash-free adjustment. The stainless steel material is chemically cleaned for use in clean setups. For securing adjuster lock nuts on these Polaris mounts, we recommend using the TW13 torque wrench below, which is designed to ensure proper torque is applied to the lock nuts for long-term locking. For securing POLARIS-LNS1 locking collars (such as on vertical-drive adjusters), we recommend using the POLARIS-T2 spanner wrench; the TW13 torque wrench can be used in combination with the spanner wrench for long-term locking. These wrenches are chemically cleaned and compatible with cleanroom and vacuum chamber applications.
Not Recommended
We do not recommend taking the adjusters out of the back plate, as it can contaminate the threading. This can reduce the fine adjustment performance significantly. Also, do not pull the front plate away as it might stretch the springs beyond their operating range or crack the sapphire seats. Finally, do not over tighten the retaining screws that secure the flat spring that holds the optic in place; only slight force is required to secure the optic in place.
Posted Comments: | |
user
 (posted 2018-09-30 15:40:11.75) Good day, we are in general happy with the Polaris mounts in our lab due to their long-term stability. Unfortunately, the relatively low thread pitch (100 TPI) makes delicate alignments with them fairly annoying in some of our applications. Is there a specific reason to not offer them with a finer pitch like several of your competitors do with their mirror mounts (up to 250 TPI or even better with differential micrometer screws), this strikes me as a bit odd for a top-of-range product like the Polaris mounts. Thank you. llamb
 (posted 2018-10-12 01:54:00.0) Thank you for your feedback. We choose to tap threads in our Polaris mounts for the most repeatable standards from mount to mount, as well as better strength for the threaded adjusters and our own equipment. The amount of thread per inch (TPI) are limited because of these taps. Alternatively, we have been able to offer custom mounts with higher TPI by using a single-point threading method, which will decrease the strength of the threads and thus decrease the allowable spring force on the Polaris mounts. These single-point threaded mounts would also be more expensive to custom-make. I see you did not leave a contact email address, so please contact techsupport@thorlabs.com if you are interested in a custom solution. lebouquj
 (posted 2018-01-30 10:15:47.697) Is it possible to mount the 1" OAP (MPD124-M01) in the POLARIS-K1S5 ? Thanks. Jean-Baptiste tcampbell
 (posted 2018-02-01 03:47:09.0) Hello, thank you for contacting Thorlabs. Yes, the 1" diameter housing of the OAP can be mounted in a 1" Polaris mount. graham.stutter
 (posted 2017-03-15 14:42:45.68) Do you sell unanodised 1 inch adapters for 1/2 inch optics that are vacuum compatible for use with the polaris mounts? tfrisch
 (posted 2017-03-15 03:09:58.0) Hello, thank you for contacting Thorlabs. I would hesitate to recommend an adapter for a Polaris system because the are designed for stability and adding an extra element would certainly perform worse, even if by a small amount. We may be able to offer a custom, but we do offer 1/2" mounts. I will reach out to you directly concerning this application. j.travers
 (posted 2016-07-20 12:02:12.193) How is the 5 urad adjustment resolution measured? Is that with a long hex key, or with knobs? It seems extraordinary for 100 TPI screws. j.fischer
 (posted 2016-06-20 10:31:18.183) Hi, are there any plans for a top-actuated 0.5" polaris mount? (I see that this is likely difficult to realize while maintaining the superior performance of the polaris series). Best regards, Joachim tmorgus
 (posted 2016-06-20 10:24:53.0) Hello Joachim,
We've thought about designing a top-actuated Polaris mount but haven't launched an active development project yet. One solution that we have offered to customers is our side hole adjuster screws. See the Polaris-K19S4 marketing presentation. This allows the traditional style kinematic mount to be adjusted from the top by using the holes drilled into the end of the actuator screw. I'll email you a photo and we can discuss the possibility of designing a new mount that meets your application needs. Sincerely, Tyler, Mechanics Business Unit Leader Loren.VanBosch
 (posted 2015-02-13 10:22:20.377) SO I see this 50 mm mount at the tradeshow in the US now for many years but I never see it at your website or in Europe. Why don't you sell this to Europe. cdaly
 (posted 2015-02-24 04:14:03.0) Response from Chris at Thorlabs: We have just recently released the 2"(50mm) series of Polaris kinematic mounts as standard catalog items. These are not restricted in any way to the US. joachim.fischer
 (posted 2014-01-30 11:14:41.39) Response to Chris at Thorlabs:
Hi Chris, sounds great. However, I didn't get an email or so, also found none in my SPAM folder... ?
Best regards,
Joe jlow
 (posted 2014-01-30 02:11:49.0) Response from Jeremy at Thorlabs: Not sure what happened to the first e-mail. We will contact you again. joachim.fischer
 (posted 2013-12-17 15:36:20.093) Dear Thorlabs team,
I'm using the POLARIS-K1-2AH and I really like the stability of the mounts. We use them at low beam heights, like 5cm above the optical table. However, so far we use a home-made metal base as I could not find a low-footprint high stability base for the polaris in your shop.
I would like to use the 1" Pedestal Pillar Posts, however, the clamp CF125 is very bulky, and the footprint of the mirror-post-clamp-combination gets very large in this way. Screwing the post directly onto the table using a setscrew is also not always possible, as in many occasions you want the incoming and the reflected beams be located directly above a row of holes. And for that, the M4 screw that mounts the polaris must be just in the middle of 4 table-holes, not above a single table-hole...
Is there any low-footprint high stability mounting I didn't find?
Otherwise, it might be a good idea to have something like PB1 or PB2 in a smaller version (with about 4.5cm diameter), so that 4 directly adjacent table-holes can be used. Another interesting base would have a square surface, with about 3.5cm edge length, four M6 counterbores in the corners and in the middle a possibility to mount a RS1 post. This would mean, that the base must be moutned to the table first and the RS1 can only be attached after mounting the base to the table, but would result in a very small footprint mounting possibility of the polaris mounts.
Best regards,
Joe cdaly
 (posted 2014-01-20 12:29:57.0) Response from Chris at Thorlabs: Thank you for your feedback. We do currently have a prototype in the works as a mounting solution for the Polaris line coupled with a 1" diameter post. We should be able provide this as a custom to you prior to release. I will contact you directly to discuss the parts and provide a quote. user
 (posted 2013-11-22 13:23:24.663) What torque is required to rotate the adjusters? jlow
 (posted 2013-12-02 08:41:36.0) Response from Jeremy at Thorlabs: The breakaway torque and the drive torque are approximately 2 oz-in. xiaoken2000
 (posted 2013-11-07 13:47:38.903) hi, i'm having a problem removing the lower two knobs from the K1 mount, can you give me the exact instructions? thank you :) cdaly
 (posted 2013-11-07 01:44:36.0) Response from Chris at Thorlabs: The knob and lead screw are just threaded together. You'll need to insert a 5/64" hex key or a ball driver through the knob into the screw. Then keep this stationary as you turn the knob counterclockwise. kucirek
 (posted 2013-08-15 16:21:14.03) Is there a metric version of the POLARIS-K05 just like KS05/M ? sharrell
 (posted 2013-08-15 10:39:00.0) Response from Sean at Thorlabs: Thank you for using our feedback tool. Our KS05/M and KM05/M mounts use a M4 tap for post mounting, thus necessitating separate metric and imperial verisons. Conversely, the POLARIS-K05 uses a counterbored hole for post mounting, making the mount post-mountable with either an 8-32 or M4 cap screw. Due to the design of the counterbore on the POLARIS-K05, both an 8-32 and M4 low-profile cap screw are included with each mount. Based on your feedback, I'll make sure that this point is clarified in the web presentation. hadmack
 (posted 2013-07-10 13:42:41.617) What is the mass of the POLARIS-K1-H and the POLARIS-K1? sharrell
 (posted 2013-07-10 17:11:00.0) Response from Sean at Thorlabs: The weight (mass) of the POLARIS-K1 is 0.46 lbs (0.209 kg), while the POLARIS-K1-H is 0.39 lbs (0.177 kg). The weights for all our products can be found by clicking on the blue Item # link in the price tables. G.Bellermin
 (posted 2013-02-27 03:40:52.807) Can you explain why the thermal test graphs have changed from what was originally posted.. I assumed the old data was real but the new graphs show such different curves It makes me question the validity...Gary sharrell
 (posted 2013-02-27 16:58:00.0) Response from Sean at Thorlabs: Thank you for your feedback regarding the new test results for our Polaris mounts. We appreciate that you took the time to look at our plots so carefully. Since the Polaris mounts were first introduced, we have been continually improving our manufacturing techniques to produce an even better mirror mount. Throughout this time, the mounts have consistently been within the stated specifications. Manufacturing improvements include a better heat treatment for deeper stress relieving and a better finishing process which also reduces material stress. In the process of developing the newest Polaris mounts, we also made several improvements to our internal test procedure and our mounting recommendations. We have added better thermal and environmental isolation to our test apparatus so that the results presented are purely due to temperature cycling. We have also performed extensive testing to determine the proper torque to apply to all of the mounting screws, and these test results were performed using these values. Torque values are listed on the spec sheet that is shipped with every Polaris mount, and we have introduced a torque driver (Item # TD24 and TD75) so that users may properly torque mounts as well. Because of these changes, we felt it was necessary to update the plots presented on our webpage. We unfortunately do not have your complete email address, but we would be happy to provide more details about any of these points via email at techsupport@thorlabs.com. noah
 (posted 2013-01-15 08:54:32.287) Hi,
I'd love to use Polaris mounts but require the fine angular control that only a differential screw has been able to provide. Can you make this with differential screws ? Is there a reason that differential screws are fundamentally incompatible with the goal of the Polaris ? tcohen
 (posted 2012-09-23 22:07:00.0) Response from Tim at Thorlabs to Ivan: The Polaris mounts do not have separate lockscrews for fixing the adjustment screws. The high TPI matched actuator/bushing results in an ultra-stable, minimal alignment drift mount that has better performance than can be done with separate screws. I would encourage you to visit our “Test Data” tab to see this. If your question is whether the actuator can be removed, yes. However, with this fine pitch using the matched actuator is recommended. We will contact you to answer any questions you may have and to discuss any features that you are looking for. diacom-ltd
 (posted 2012-09-17 22:54:14.0) Please tell me whether the adjustment screws are fixed at Polaris.
Best regards,
Ivan tcohen
 (posted 2012-07-19 09:27:00.0) Response from Tim at Thorlabs to Ryan: This will depend on how you place the load. I’d like to discuss this with you further. We may be able to offer stiffer springs for a beefier front plate and I will contact you to assist you directly. rpsmith
 (posted 2012-07-10 19:15:26.0) Hello,
I'm wondering if you have any experience with attaching more weight to the front surface of the polaris mount. The front plate of the polaris weighs 68 grams. I intend to attach an additional 250 grams onto the front of this plate. Will this be a problem with the stability? Would you suggest that I heat treat the mass that I will be attaching (200 C for 2 hours)? I was also thinking that maybe stiffer springs (that attach the front plate to the part holding the adjustment knobs) would be helpful. Do you offer more stiff springs for these mirror mounts?
Sincerely,
Ryan tcohen
 (posted 2012-05-04 14:48:00.0) Response from Tim at Thorlabs: Thank you for your feedback! The POLARIS-K1-H utilizes a shortened actuator that will limit the angular adjustment range when using our traditional removable adjustment knobs. We are able to offer an item that has a 5/64 hex key fixed to a removable knob that will not limit the angular range. I will contact you with more information. parkse
 (posted 2012-05-03 11:05:03.0) I need removable adjustment knob for POLARIS-K1-H. tcohen
 (posted 2012-04-12 16:28:00.0) Response from Tim at Thorlabs: Thank you for your feedback! We are currently developing a new product family that addresses this concern by creating a design with better performance than a nylon tipped set screw. We would love to provide our data and discuss this with you to ensure that our new design meets or exceeds your expectations. We will contact you directly as well as update our presentation with this information soon. aatarasov
 (posted 2012-04-12 14:20:19.0) We have bought more than 20 mounts and use them in our laser laboratory. In general, we are satisfied with alignment accuracy and position stability of this mount and are intended to use them in our lasers. But we meet one serious disadvantage of mirror retainer design: high mecanical pressure at the contact point between spring and mirror substrate induce birefringence in the substrate. Birefringence is maximum near contact point and remains considerable even at the mirror center. Contact point position is ~under 45 deg to vertical and horyzontal axis. In this case axis of birefringence alo is directed at +/- 45 deg to vertical axis. Working with lasers, we usially set vertical or horyzontal linear polarisation. So, mirror substrate with induced birefringence acts as a waveplate for transmitting light. In my case, I used this mount for Ti: Sapphire laser pump mirror (HT for 532nm and HR for Ti: Sapphire wavelengths) and was shocked when linear polarisation of pump light was turned into almost circular polarisation. The same problem you will obtain, if use mount for output mirror or beamsplitter.
To my mind, the best solution to retain mirror is New Focus solution (3-point flexible O-ring spring at mirror face). tcohen
 (posted 2012-03-28 11:19:00.0) Response from Tim at Thorlabs: We should be able to offer a vacuum compatible version of the POLARIS-K05. I have contacted you with some details and to get more information. ale.cere
 (posted 2012-03-28 08:24:48.0) Is there a vacuum compatible version for the POLARIS-K05? bdada
 (posted 2012-02-08 19:52:00.0) Response from Buki at Thorlabs to bmills:
This is an update on an earlier post about the threaded Polaris mounts. We featured the threaded Polaris mount at Photonics West 2012 and will be releasing it soon. Please contact TechSupport@thorlabs.com if you have any questions. bdada
 (posted 2012-02-08 19:49:00.0) Response from Buki at Thorlabs to flickingerd:
To add an update to my previous post, our design engineers are working out some ideas for versions of the Polaris-K05 that would include integrated or removable knobs. We will contact you with more information and would love to send you a prototype.
We will also review your comment about the mislabeled picture. Thank you again for your feedback. bdada
 (posted 2012-02-08 00:58:00.0) Response from Buki at Thorlabs:
Thank you for your feedback regarding the Polaris-K05. We are discussing this with our production team and will post an update shortly. flickingerd
 (posted 2012-02-07 13:24:35.0) I would buy some Polaris-K05, but the lack of knobs is a deal-breaker for some applications for me. I'd highly recommend at least selling little removable knobs. They could have a diameter not much larger than the screw and still be useful. The knob would just have a little hex-profile bit that comes out that you could insert into the screws. FYI: one of the supposed pictures of the POLARIS-K1 below is actually a mislabeled picture of the POLARIS-K05. bdada
 (posted 2011-10-03 15:42:00.0) Response from Buki at Thorlabs:
Thank you for your feedback. We provide Temperature Cycling Test data on our website for the Polaris mount. Please contact TechSupport@thorlabs.com to discuss your set up so we can determine the cause of the drift you are experiencing. user
 (posted 2011-09-29 14:07:44.0) Response from Tyler at Thorlabs: Thorlabs managed to keep or lower prices on over 80% of our products in the recently released V21 catalog. For the remaining products, it was difficult, but necessary to raise the price. The increase in price of the POLARIS-K1 was the first price change for this product since it was introduced in the 2009 Volume 20 Thorlabs catalog. Because of our commitment to keeping product prices fixed between printings of our catalog, Thorlabs continued to honor the V20 price even though manufacturing and material costs for the POLARIS-K1 rose substantially in 2009 and 2010. Thorlabs is committed to being a valuable member of the photonics community and will continue to strive to provide the best possible value for the products and services that it provides. user
 (posted 2011-09-23 19:10:55.0) Hey Javier, there must be a mistake with the prices on these mounts. They were just $99 and now they are something like $130. Please correct the price back to $99 where it was. user
 (posted 2011-09-21 20:17:34.0) I have a few of these K1 mounts and they look very cool but after I align them, they drift more than 5ur and Im in a temperture controled lab. Its not terribe but its also not 5ur. Im gettng something like 10 to 20 ur of drift. I mounted it on a pedesal post too. Ater a few days they dont drift as much but it still is moving more than 5ur. How could you possibly get 5ur in a temperture varent environment. jjurado
 (posted 2011-08-18 11:22:00.0) Response from Javier at Thorlabs to roger.vanzee: As previously mentioned in our response to akobuije below, the POLARIS mounts are not vacuum compatible, but we can offer vacuum compatible versions. I will contact you directly to get the quotation process started. roger.vanzee
 (posted 2011-08-17 18:15:40.0) Are the Polaris mounts vacuum compatible? - Roger jjurado
 (posted 2011-08-01 13:53:00.0) Response from Javier at Thorlabs to bmills: Thank you very much for contacting us. We are currently developing the design of a threaded version of the POLARIS-K1 mirror mount. I will contact you directly to keep you up to date on the status. bmills
 (posted 2011-07-27 22:00:28.0) When will a version of the Polaris mount be available with a 1 inch threaded face (like a KM100T)? cbrideau
 (posted 2011-05-12 12:52:52.0) The 1/2" mount looks very streamlined. It reminds me of the typical design of most cars, with a highly aerodynamic look. Nice work! jjurado
 (posted 2011-05-02 13:54:00.0) Response from Javier at Thorlabs to bloombj: Thank you very much for your feedback. We currently do not have 2" and cage compatible versions of the Polaris mirror in the development phase. However, I will share your comments with our mechanics engineers and let you know if we decide to undertake these projects. bloombj
 (posted 2011-05-02 09:26:44.0) Also, cage mount compatible versions would be nice as well. bloombj
 (posted 2011-05-02 09:25:30.0) Will a 2" diameter version be available soon? We really like the 1" versions. user
 (posted 2010-08-30 09:06:24.0) A reply from Jens at Thorlabs: yes, the KGM60 is compatible with the Polaris-K1 mount. The back side of the KGM mount has a diameter of 1" and will fit into the Polaris mount where it is held in place using the standard Polaris clamping mechanism. sshosseini
 (posted 2010-08-29 13:01:15.0) Can i use KGM60 installed on POLARIS-K1? How? Adam
 (posted 2010-05-04 00:36:39.0) A response from Adam at Thorlabs to h2004k: Currently, the Polaris mounts do not have locking mechanisms. The reason there is no locking mechanism is because during the lock engagement the alignment would shift significantly. Please note that the POALRIS mount can be comfortably adjusted to within 5 urad, and it was found to hold its alignment (within 5urad band) throughout multiple days of vigorous thermal cycling. Theoretically, the mount should be quite stable over the time frame of a few months, but do not have the test data to confirm this. h2004k
 (posted 2010-05-03 22:29:48.0) I am wondering if lockable screws are available? In my experiment of testing several mirror mounts from several manufactures, my conclusion is that the lock function is needed if long term (longer than few months) stability is expected. apalmentieri
 (posted 2010-02-08 15:27:23.0) A response from Adam at Thorlabs to akobuije: The current design of the POLARIS-K1 does not contain vacuum compatible grease so it is not considered vacuum compatible. We can provide this item as a special and I will email you directly to see if you are interested in this option. akobuije
 (posted 2010-02-07 21:44:58.0) Is POLARIS-K1 vacuum compatible? |
Polaris Mount Optic Retention Methods (Click Image to Enlarge) | |||
---|---|---|---|
Side Lock | SM Threaded | Low Distortion | Glue In |
![]() |
![]() |
![]() |
![]() |
Polaris Mount Adjuster Types (Click Image for Details) | ||||
---|---|---|---|---|
Side Hole | Hex | Adjuster Knobs | Adjuster Lock Nuts |
Piezo Adjusters |
![]() |
![]() |
![]() |
![]() |
![]() |
Thorlabs offers several different general varieties of Polaris mounts, including kinematic side optic retention, SM-threaded, low optic distortion, piezo-actuated, and glue-in optic mounts, as well as a fixed monolithic mirror mount and fixed optic mounts. Click to expand the tables below and see our complete line of Polaris mounts, listed by optic bore size, and then arranged by optic retention method and adjuster type. We also offer a line of accessories that have been specifically designed for use with our Polaris mounts; these are listed in the table immediately below.
Accessories for Polaris Mounts |
---|
Ø1" Posts for Polaris Mirror Mounts |
Polaris Clamping Arm |
Polaris 45º Adapter |
Polaris Mounts for Ø1/2" Optics |
---|
Polaris Mounts for Ø19 mm (3/4") Optics |
---|
Polaris Mounts for Ø25 mm Optics |
---|
Polaris Mounts for Ø1" Optics |
---|
Polaris Mounts for Ø1.5" Optics |
---|
Polaris Mounts for Ø50 mm Optics |
---|
Polaris Mounts for Ø2" Optics |
---|
Polaris Mounts for Ø3" Optics |
---|
Polaris Kinematic Platform Mount |
---|


Click to Enlarge
Methods of Adjusting the POLARIS-K1S5 Ø1" Mount:
A: 5/64" or 2.0 mm Hex Key in the End of the Adjuster
B: SA1 Tool Through Adjuster Side Holes
C: POLARIS-N5 Removable Knobs on the Adjuster
D: HKTS-5/64 Hex Knobs with Side Hole Fine Adjustment

Click to Enlarge
Mount Shown with Optional POLARIS-N5 Removable Knobs
- 3 Hex Adjusters with Side Holes (See Image to the Right)
- Designed for use with Ø1" Optics
- 100 TPI Matched Actuator/Body Pairs
- ±4° Mechanical Angular Range
- ~7.7 mrad/rev Resolution
- Less than 1 µrad Deviation after Temperature Cycling
(See the Test Data Tab for Details) - Patented Monolithic Flexure Arm Design for Minimal Optic Distortion and Improved Optic Holding Stability (US Patent 10,101,559, See the Test Data Tab for Details)
The POLARIS-K1S5 is the three-adjuster option of the POLARIS-K1S4 (sold below). This 3-adjuster Ø1" Polaris Kinematic Mirror Mount is designed to provide easy high-resolution adjustment and long-term alignment stability. The mount features a monolithic flexure arm that can be actuated using the included screw and a 0.05" (1.3 mm) hex key. The monolithic flexure arm design keeps wavefront distortion on the mounted optic to a minimum while providing an optic retention force that is much stronger than the force provided by our other Ø1" Polaris mounts that use a setscrew and flexure spring design, as shown in the Test Data tab. The three-adjuster design provides tip and tilt plus Z-axis (optical axis) adjustment. Compared to the POLARIS-K1 and POLARIS-K1-H Ø1" mounts, the monolithic front plate and stiffer springs used in the construction of the POLARIS-K1S5 provide enhanced stability and reduced optic distortion, making this mount an ideal solution for OEM applications that require reliable operation in rugged environments.
The 100 TPI adjusters feature three Ø0.07" through holes that allow for actuation from the side using our precision-fit SA1 Side Hole Adjustment Tool (sold below) or a 1/16" (1.5 mm) balldriver or hex key. Each adjuster also has a 5/64" (2.0 mm) hex and may be adjusted with the hex on the end of the SA1, our HKTS-5/64 Hex Key Thumbscrews (sold below), or any other 5/64" (2.0 mm) hex wrench. Alternatively, POLARIS-N5 removable, low-profile adjustment knobs (sold below) can be threaded onto the adjusters for improved feel in fine-resolution adjustments; note that the removable knobs will block the adjuster side holes but not the hex. The adjusters on this mount can be locked using the POLARIS-LN1 lock nuts or POLARIS-LNS1 locking collars (sold separately below).
Post mounting is provided by two #8 (M4) counterbores. For custom mounting configurations, two Ø2 mm alignment pin holes are located on each mounting face for setting a precise location and mounting angle. Standard DIN 7-m6 ground dowel pins are recommended (click on the red documents icon below for details). We recommend using this mount with a stainless steel post that also has Ø2 mm alignment pin holes, such as our Ø1" Posts for Polaris Mirror Mounts.


Click to Enlarge
Methods of Adjusting the POLARIS-K1S4 Ø1" Mount:
A: 5/64" or 2.0 mm Hex Key in the End of the Adjuster
B: SA1 Tool Through Adjuster Side Holes
C: POLARIS-N5 Removable Knobs on the Adjuster
D: HKTS-5/64 Hex Knobs with 1/16" or 1.5 mm Balldriver Through Side Holes for Fine Adjustment

Click to Enlarge
Mount Shown with Optional POLARIS-N5 Removable Knobs
- 2 Hex Adjusters with Side Holes (See Image to the Right)
- Designed for use with Ø1" Optics
- 100 TPI Matched Actuator/Body Pairs
- ±4° Mechanical Angular Range
- ~7.7 mrad/rev Resolution
- Less than 1 µrad Deviation after Temperature Cycling
(See the Test Data Tab for Details) - Patented Monolithic Flexure Arm Design for Minimal Optic Distortion and Improved Optic Holding Stability (US Patent 10,101,559, See the Test Data Tab for Details)
This 2-Adjuster Ø1" Polaris Kinematic Mirror Mount is designed to provide easy high-resolution adjustment and long-term alignment stability. The mount features a monolithic flexure arm that can be actuated using the included screw and a 0.05" (1.3 mm) hex key. The monolithic flexure arm design keeps wavefront distortion on the mounted optic to a minimum while providing an optic retention force that is much stronger than the force provided by our other Ø1" Polaris mounts that use a setscrew and flexure spring design, as shown in the Test Data tab. The 2-adjuster design improves mount stability by limiting the available degrees of freedom for movement. Compared to the POLARIS-K1 and POLARIS-K1-H Ø1" mounts, the monolithic front plate and stiffer springs used in the construction of the POLARIS-K1S4 provide enhanced stability and reduced optic distortion, making this mount an ideal solution for OEM applications that require reliable operation in rugged environments.
The 100 TPI adjusters feature three Ø0.07" through holes that allow for actuation from the side using our precision-fit SA1 Side Hole Adjustment Tool (sold below) or a 1/16" (1.5 mm) balldriver or hex key. Each adjuster also has a 5/64" (2.0 mm) hex and may be adjusted with the hex on the end of the SA1, our HKTS-5/64 Hex Key Thumbscrews (sold below), or any other 5/64" (2.0 mm) hex wrench. Alternatively, POLARIS-N5 removable, low-profile adjustment knobs (sold below) can be threaded onto the adjusters for improved feel in fine-resolution adjustments; note that the removable knobs will block the adjuster side holes but not the hex. The adjusters on this mount can be locked using the POLARIS-LN1 lock nuts or POLARIS-LNS1 locking collars (sold separately below).
Post mounting is provided by two #8 (M4) counterbores. For custom mounting configurations, two Ø2 mm alignment pin holes are located on each mounting face for setting a precise location and mounting angle. Standard DIN 7-m6 ground dowel pins are recommended (click on the red documents icon below for details). We recommend using this mount with a stainless steel post that also has Ø2 mm alignment pin holes, such as our Ø1" Posts for Polaris Mirror Mounts.
To order compatible knobs, please contact techsupport@thorlabs.com.


Click to Enlarge
Using the POLARIS-K1VS2 Ø1" Mount:
A: POLARIS-T2 Tool for Adjusting POLARIS-LNS1 Collars
B: 5/64" or 2.0 mm Hex Key in the End of an Adjuster
C: POLARIS-N5 Removable Knobs on the Adjusters*
D: HKTS-5/64 Hex Knobs on the Adjusters

Click to Enlarge
Mount Shown with Optional POLARIS-N5 Removable Knobs* (Not Included)
- Designed for use with Ø1" Optics
- ±4° Mechanical Angular Range
- ~7.7 mrad/rev Resolution
- 100 TPI Matched Actuator/Body Pairs
- Less than 1 µrad Deviation after Temperature Cycling
(See the Test Data Tab for Details) - Patented Monolithic Flexure Arm Design for Minimal Optic Distortion and Improved Optic Holding Stability (US Patent 10,101,559, See the Test Data Tab for Details)
This 2-Adjuster Ø1" Polaris Kinematic Mirror Mount provides long-term stability and high-resolution adjustment using vertical drives. This design allows for adjustment in situations where there may not be space behind the mount for horizontal access to the adjusters. To secure an optic, the mount uses a monolithic flexure arm that can be actuated using the included screw and a 0.05" (1.3 mm) hex key. The monolithic flexure arm design keeps wavefront distortion on the mounted optic to a minimum while providing strong optic retention force (see the Test Data tab for details).
The 2-adjuster design improves mount stability by limiting the available degrees of freedom for movement. The monolithic front plate and stiff springs used in the construction of the POLARIS-K1VS2 mount provide enhanced stability and reduced optic distortion, making this mount an ideal solution for OEM applications that require reliable operation in rugged environments.
The 100 TPI adjusters feature a 5/64" (2.0 mm) hex and may be adjusted with our HKTS-5/64 Hex Key Thumbscrews, the hex on the end of the SA1 Adjustment Tool, or any other 5/64" (2.0 mm) hex wrench. Alternatively, POLARIS-N5 removable, low-profile adjustment knobs can be threaded onto the adjusters for improved feel in fine-resolution adjustments, although mechanical angular range may be reduced.
The adjusters on this mount can be locked using the POLARIS-LNS1 locking collars. Two are pre-installed on the POLARIS-K1VS2, one for each adjuster. The included locking collars can be loosened or tightened most easily using the POLARIS-T2 spanner wrench.
Post mounting is provided by two #8 (M4) counterbores. For custom mounting configurations, two Ø2 mm alignment pin holes are located on each mounting face for setting a precise location and mounting angle. Standard DIN 7-m6 ground dowel pins are recommended (click on the red documents icon below for details). We recommend using this mount with a stainless steel post that also has Ø2 mm alignment pin holes, such as our Ø1" Posts for Polaris Mirror Mounts.
*POLARIS-N5 Removable Knobs thread directly onto the exposed adjuster screws. Using them on the POLARIS-K1VS2 may result in a reduced mechanical angular range.


Click to Enlarge
POLARIS-K1C4 Mount with Optic and Optional POLARIS-N5 Removable Knobs
Compatible Mounts |
---|
POLARIS-K25S4/M POLARIS-K1C4 POLARIS-K1G4 POLARIS-K1S4 POLARIS-K1S5 POLARIS-K15S4 POLARIS-K15F4 POLARIS-K50S4/M |
- For Convenient Adjustment of 1/4"-100 Adjusters
- Attaches Directly to Adjuster Threading
- Sold Individually
The Polaris® Removable Knobs for 1/4"-100 Adjusters allows the user to adjust a Polaris kinematic mirror mount by hand. The knobs can be used with select Polaris mounts, listed in the table to the right. Note that when the knobs are used with any of these mounts, they will block the side through holes on the adjuster. The adjuster screw's 5/64" (2 mm) hex socket is still usable when the knobs are attached.
The knobs are made from chemically cleaned and heat-treated 303 stainless steel that provides vacuum compatibility down to 10-9 Torr at 25 °C with proper bake out (10-5 Torr at 25 °C without bake out).
To order compatible knobs, please contact Tech Support.


Click to Enlarge
F25USK2 Knob Shown Attached to a POLARIS-K1 Mirror Mount
- Ø0.925" Knob for Additional Angular Resolution
- Clearance Hole Allows Access to Hex Socket of the Adjuster
This removable adjustment knob is compatible with many of our 1/4"-100 adjusters, including those used in the Ø1" and Ø2" Polaris Kinematic Mounts and our Polaris Kinematic Platform Mount. The larger Ø0.925" size provides additional angular resolution over the standard Polaris knobs.
Please note that the F25USK2 knob is not compatible with Polaris mounts that use side-hole adjusters. The recessed bore of knob is not deep enough to allow the knob to engage the threads on the side-hole adjuster.

- For Convenient Adjustment of 5/64" and 2 mm Hex-Driven Actuators
- Red Anodized Adjustment Knob with Engraved Hex Size
- Replaceable Hex Tip
- Sold in Packages of 4
These 5/64" Hex Key Adjuster Thumbscrews allow for quick adjustment of many 5/64" and 2 mm hex-driven actuators (or standard actuators with the knobs removed). These temporary knobs can be left in the screw's hex socket between adjustments for convenience (see photo to the right). An 8-32 setscrew (5/64" hex) secures the replaceable hex bit, which can be reversed if the tip is stripped. Contact Tech Support to order replacement hex key bits.
We offer hex key thumbscrews in sizes from 0.050" to 3/16" and 2 mm to 5 mm.


Click to Enlarge
The SA1 Adjusting a POLARIS-K1S4 Using the Side Holes and Rear Hex
- Ø0.07" Precision-Fit Tip for Side Holes on Polaris Adjusters
- 5/64" (2.0 mm) Hex on Handle
- Magnetic, Chemically Cleaned Stainless Steel
The Side Hole Adjustment Tool features a Ø0.07" precision-fit tip designed for Polaris mounts with side hole adjusters. The handle features a 5/64" (2.0 mm) hex allowing the SA1 to act as a small knob, and the central nut is compatible with a 6.0 mm wrench allowing for a longer lever arm. The precision-fit tip minimizes backlash during adjustments and the depth stop allows the tool to rest securely in a side hole between adjustments. On Ø25 mm mirror mounts and larger, the 1.62" length allows the tool to adjust the actuator 360° without interfering with the other adjuster on the back of the mount.
The SA1 is made of chemically cleaned, hardened, super alloy stainless steel for durability and compatibility with clean environments. The tool is also magnetic allowing it to be easily retrieved from tight or sensitive setups using a magnet.

To install a lock nut without cross threading, gently place the lock nut against the end of the adjuster. "Unscrew" the nut until the threads of the nut and the adjuster align before threading the nut onto the adjuster. This animation shows the installation of a POLARIS-LN1 lock nut on a POLARIS-K1F1 low distortion mount.
- Provides Long Term Adjuster Stability
- Compatible with Select Polaris Mounts
- 0.08" (1.9 mm) Thick
- 13 mm Hex can be Tightened with Thin-Head or Cone Wrench
This lock nut is compatible with Polaris mounts that have 1/4"-100 adjusters, excluding the piezo-driven mounts, mounts with low-profile adjusters (Item #s POLARIS-K1-H and POLARIS-K1-2AH), and vertically driven mount (Item # POLARIS-K1VS2). Designed for long-term adjuster stability or applications that are exposed to shock and vibration, the lock nut is pre-greased with the same ultra-high-vacuum-compatible, low-outgassing PTFE grease as the Polaris mounts and has been tested for adjuster fit.
For applications that require frequent tuning of the adjusters, the lock nuts only need to be lightly tightened by hand to a torque of approximately 4 to 8 oz-in (0.03 to 0.06 N·m). For long term stability, we recommend tightening to a torque of 32 oz-in, which can be achieved by using our TW13 preset torque wrench (sold below). POLARIS-LN1 lock nuts have a 13 mm hex. To avoid cross threading the lock nut, place it against the adjuster and "unscrew" the lock nut until you feel a slight drop; then thread the lock nut onto the adjuster.

- Provides Long Term Adjuster Stability
- Compatible with Select Polaris Mounts
- Low Profile: Ø0.33" (Ø8.4 mm) x 0.08" (1.9 mm) Thick
- Tighten Along Rotational Axis Using the POLARIS-T2 Spanner Wrench
This locking collar is compatible with Polaris mounts that have 1/4"-100 adjusters, excluding the piezo-driven mounts and mounts with low-profile adjusters (Item #s POLARIS-K1-H and POLARIS-K1-2AH). Designed for long-term adjuster stability or applications that are exposed to shock and vibration, these locking collars are pre-greased with the same ultra-high-vacuum-compatible, low-outgassing PTFE grease as the Polaris mounts and have been tested for adjuster fit.
The POLARIS-T2 spanner wrench has been specifically designed for use in securing the POLARIS-LNS1 locking collar. The double spanner head enables complete engagement while the design allows locking collar adjustments to be along the same line as the adjuster itself. A center through hole allows a 2 mm ball driver to pass through the spanner wrench, so that the adjuster can be held in position while the locking collar is engaged.
For applications that require frequent tuning of the adjusters, the locking collar only needs to be lightly tightened to a torque of approximately 4 to 8 oz-in (0.03 to 0.06 N·m). For long term stability, we recommend tightening to a torque of 32 oz-in, which can be achieved by using our TW13 preset torque wrench (sold below) in combination with the POLARIS-T2 spanner wrench. To avoid cross threading the locking collar, place it against the adjuster and "unscrew" the collar until you feel a slight drop; then thread the collar onto the adjuster.


Click to Enlarge
TW13 Torque Wrench Used to Secure POLARIS-LN1 Lock Nut on POLARIS-K2S2 Mirror Mount

Click to Enlarge
The TW13 wrench is engraved with its preset torque value and item #.
- 13 mm Hex for Use with POLARIS-LN1 Lock Nut and POLARIS-T2 Spanner Wrench, as well as POLARIS-LN4 Lock Nut
- Preset Torque Value of 32 oz-in (0.23 N•m)
- Break-Over Design Ensures Proper Torque is Applied
- Ideal for Applications Requiring Long-Term Locking
This torque wrench has a preset torque value of 32 oz-in for use with the
POLARIS-LN1 lock nut used on Polaris® mounts as well as the POLARIS-T2 spanner wrench. The wrench is also compatible with the POLARIS-LN4 lock nut. When the preset torque value has been achieved, the break-over design will cause the pivoting joint to "break," as shown to the right. The wrench's hex head will move back into place once the force is removed. This design prevents further force from being applied to the lock nut. Engraved guidelines indicate the angle the wrench should pivot in order to apply the specified torque; pivoting the handle past these guidelines will over-torque the lock nut. The wrench is also engraved with its preset torque value, torque direction, wrench size, and item # for easy identification in the field.
This wrench is designed to be compatible with cleanroom and vacuum chamber applications. It is chemically cleaned using the Carpenter AAA passivation method to remove sulfur, iron, and contaminants from the surface. After passivation, it is assembled in a clean environment and double vacuum bagged to eliminate contamination when transported into a cleanroom. The wrench has a bead blasted finish to minimize reflections when working with setups that include lasers.
Please note that these wrenches are not intended for use in applications where adjusters are frequently tuned, as these applications typically require torque values of 4 to 8 oz-in (0.03 to 0.06 N·m).