D-Shaped Pickoff Mirrors
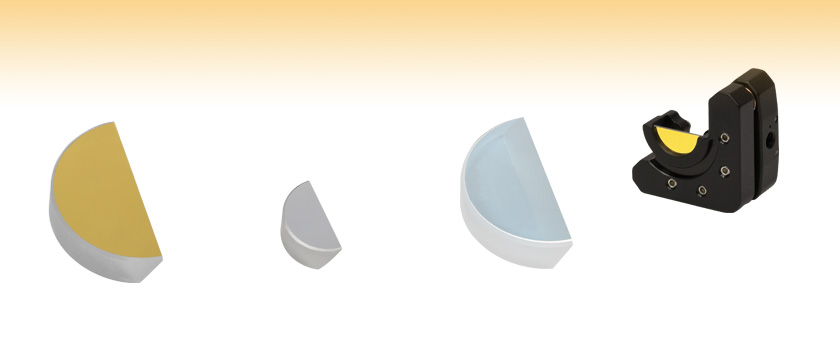
- Ability to Separate Closely Spaced Beams
- Ø1/2" or Ø1" Versions
- Several Different Metallic and Broadband Dielectric Coatings Available
PFD10-03-M01
PFD05-03-P01
BBD1-E03
Application Idea
PFD05-03-M01 Mirror with
KM05DR Mount

Please Wait
Features
- Choose from Five Coatings:
- UV-Enhanced Aluminum: 250 - 450 nm
- Protected Silver: 450 nm - 20 µm
- Protected Gold: 800 nm - 20 µm
- -E02 Broadband Dielectric Coating: 400 - 750 nm
- -E03 Broadband Dielectric Coating: 750 - 1100 nm
- Choose from Ø1/2" or Ø1" Versions
- Ideal for Use with Closely Spaced Beams
- Reflective Coating Beveled 0.05 mm at Straight Edge
These D-shaped pickoff mirrors, which are available with a number of different coatings, are designed to enable the separation of closely spaced beams. D-shaped mirrors are ideal for picking off one of two closely spaced beams because the reflective coating extends to within 0.05 mm of the straight edge of the mirror. In addition, a wedge of the substrate is removed from behind the straight edge of the mirror in order to prevent the beam that was not picked off from clipping the pickoff mirror. We also offer fixed and kinematic mounts for D-shaped mirrors.
Metallic Mirror Specifications
Coating | UV-Enhanced Aluminum | Protected Silver | Protected Gold | |||
---|---|---|---|---|---|---|
Item # | PFD05-03-F01 | PFD10-03-F01 | PFD05-03-P01 | PFD10-03-P01 | PFD05-03-M01 | PFD10-03-M01 |
Diameter | Ø1/2" | Ø1" | Ø1/2" | Ø1" | Ø1/2" | Ø1" |
Diameter Tolerance | +0.0/-0.2 mm | |||||
Thickness | 6 mm | |||||
Material | Fused Silica | |||||
Front Surface Flatness | λ/10 @ 633 nm (Peak to Valley) | |||||
Surface Quality | 40-20 Scratch-Dig | |||||
Clear Aperture | >90% of Diameter | |||||
Reflectance | Ravg > 90% from 250 - 450 nm | Ravg > 97.5% from 450 nm - 2 μm Ravg > 96% from 2 - 20 μm |
Ravg > 96% from 800 nm - 20 μm | |||
Wedge | <5 arcmin | |||||
Damage Threshold (Pulse) | 0.25 J/cm2 (266 nm, 10 ns, 10 Hz, Ø0.150 mm) 0.3 J/cm2 (355 nm, 10 ns, 10 Hz, Ø0.381 mm) |
0.225 J/cm2 (800 nm, 99 fs, 1 kHz, Ø0.167 mm) 3 J/cm2 (1064 nm, 10 ns, 10 Hz, Ø1.000 mm) |
2 J/cm2 (1064 nm, 10 ns, 10 Hz, Ø1.000 mm) | |||
Damage Threshold (CW)a | 300 W/cm (1.064 µm, Ø0.044 mm) 500 W/cm (10.6 µm, Ø0.339 mm) |
500 W/cm (1.07 µm, Ø0.974 mm) 1500 W/cm (10.6 µm, Ø0.339 mm) |
500 W/cm (1.070 µm, Ø0.089 mm) 750 W/cm (10.6 µm, Ø0.339 mm) |
Broadband Dielectric Mirror Specifications
Coating | -E02 Coating | -E03 Coating | ||
---|---|---|---|---|
Item # | BBD05-E02 | BBD1-E02 | BBD05-E03 | BBD1-E03 |
Coating Range | 400 - 750 nm | 750 - 1100 nm | ||
Diameter | Ø1/2" | Ø1" | Ø1/2" | Ø1" |
Diameter Tolerance | +0.0/-0.2 mm | |||
Thickness | 6 mm ± 0.2 mm | |||
Material | Fused Silica | |||
Front Surface Flatness | λ/10 @ 633 nm (Peak to Valley) | |||
Surface Quality | 10-5 Scratch-Dig | |||
Clear Aperture | >90% of Diameter | |||
Reflectance (P and S Polarization for 0 - 45°) |
Ravg > 99% from 400 - 750 nm | Ravg > 99% from 700 - 1100 nm | ||
Wedge | <5 arcmin | |||
Damage Threshold (Pulse) | 0.25 J/cm2 (532 nm, 10 ns, 10 Hz, Ø0.803 mm) | 0.205 J/cm2 (800 nm, 99 fs, 1 kHz, Ø0.166 mm) 1 J/cm2 (810 nm, 10 ns, 10 Hz, Ø0.133 mm) 0.5 J/cm2 (1064 nm, 10 ns, 10 Hz, Ø0.433 mm) |
||
Damage Threshold (CW)a,b | 550 W/cm (532 nm, Ø1.000 mm) | 10 kW/cm (1070 nm, Ø0.971 mm) |
All data shown below is for unpolarized light, unless otherwise stated. The shaded regions in the graphs denote the ranges over which we guarantee the specified reflectance. Please note that the reflectance outside of these bands is typical and can vary from lot to lot, especially in out-of-band regions where the reflectance is fluctuating or sloped.
UV-Enhanced Aluminum Coating (250 - 450 nm)
Protected Silver Coating (450 nm - 20 µm)
Protected Gold Coating (800 nm - 20 µm)
These plots show the reflectivity of our -E02 (400 - 750 nm) and -E03 (750 - 1100 nm) dielectric coatings for a typical coating run. The shaded region in each graph denotes the spectral range over which the coating is highly reflective. Due to variations in each run, this recommended spectral range is narrower than the actual range over which the optic will be highly reflective. If you have any concerns about the interpretation of this data, please contact Tech Support. For applications that require a mirror that bridges the spectral range between the dielectric coatings, please consider a metallic mirror.
-E02 Coating (400 - 750 nm)
Excel Spreadsheet with Raw Data for -E02 Coating, 8° and 45° AOI
-E03 Coating (750 - 1100 nm)
Damage Threshold Specifications | ||
---|---|---|
Coating Designation (Item # Suffix) |
Type | Damage Threshold |
-F01 | Pulsed | 0.25 J/cm2 (266 nm, 10 ns, 10 Hz, Ø0.150 mm) 0.3 J/cm2 (355 nm,10 ns, 10 Hz, Ø0.381 mm) |
CWa | 300 W/cm (1.064 µm, Ø0.044 mm) 500 W/cm (10.6 µm, Ø0.339 mm) |
|
-P01 | Pulsed | 0.225 J/cm2 (800 nm, 99 fs, 1 kHz, Ø0.167 mm) 3 J/cm2 (1064 nm,10 ns, 10 Hz, Ø1.000 mm) |
CWa | 500 W/cm (1.07 µm, Ø0.974 mm) 1500 W/cm (10.6 µm, Ø0.339 mm) |
|
-M01 | Pulsed | 2 J/cm2 (1064 nm, 10 ns, 10 Hz, Ø1.000 mm) |
CWa | 500 W/cm (1.070 µm, Ø0.089 mm) 750 W/cm (10.6 µm, Ø0.339 mm) |
|
-E02 | Pulsed | 0.25 J/cm2 (532 nm,10 ns, 10 Hz, Ø0.803 mm) |
CWa,b | 550 W/cm (532 nm, Ø1.000 mm) | |
-E03 | Pulsed | 0.205 J/cm2 (800 nm, 99 fs, 1 kHz, Ø0.166 mm) 1 J/cm2 (810 nm,10 ns, 10 Hz, Ø0.133 mm) 0.5 J/cm2 (1064 nm,10 ns, 10 Hz, Ø0.433 mm) |
CWa,b | 10 kW/cm (1070 nm, Ø0.971 mm) |
Damage Threshold Data for Thorlabs' Pickoff Mirrors
The specifications to the right are measured data for Thorlabs' pickoff mirrors. Damage threshold specifications are constant for a given coating type, regardless of the size of the lens.
Laser Induced Damage Threshold Tutorial
The following is a general overview of how laser induced damage thresholds are measured and how the values may be utilized in determining the appropriateness of an optic for a given application. When choosing optics, it is important to understand the Laser Induced Damage Threshold (LIDT) of the optics being used. The LIDT for an optic greatly depends on the type of laser you are using. Continuous wave (CW) lasers typically cause damage from thermal effects (absorption either in the coating or in the substrate). Pulsed lasers, on the other hand, often strip electrons from the lattice structure of an optic before causing thermal damage. Note that the guideline presented here assumes room temperature operation and optics in new condition (i.e., within scratch-dig spec, surface free of contamination, etc.). Because dust or other particles on the surface of an optic can cause damage at lower thresholds, we recommend keeping surfaces clean and free of debris. For more information on cleaning optics, please see our Optics Cleaning tutorial.
Testing Method
Thorlabs' LIDT testing is done in compliance with ISO/DIS 11254 and ISO 21254 specifications.
First, a low-power/energy beam is directed to the optic under test. The optic is exposed in 10 locations to this laser beam for 30 seconds (CW) or for a number of pulses (pulse repetition frequency specified). After exposure, the optic is examined by a microscope (~100X magnification) for any visible damage. The number of locations that are damaged at a particular power/energy level is recorded. Next, the power/energy is either increased or decreased and the optic is exposed at 10 new locations. This process is repeated until damage is observed. The damage threshold is then assigned to be the highest power/energy that the optic can withstand without causing damage. A histogram such as that below represents the testing of one BB1-E02 mirror.

The photograph above is a protected aluminum-coated mirror after LIDT testing. In this particular test, it handled 0.43 J/cm2 (1064 nm, 10 ns pulse, 10 Hz, Ø1.000 mm) before damage.

Example Test Data | |||
---|---|---|---|
Fluence | # of Tested Locations | Locations with Damage | Locations Without Damage |
1.50 J/cm2 | 10 | 0 | 10 |
1.75 J/cm2 | 10 | 0 | 10 |
2.00 J/cm2 | 10 | 0 | 10 |
2.25 J/cm2 | 10 | 1 | 9 |
3.00 J/cm2 | 10 | 1 | 9 |
5.00 J/cm2 | 10 | 9 | 1 |
According to the test, the damage threshold of the mirror was 2.00 J/cm2 (532 nm, 10 ns pulse, 10 Hz, Ø0.803 mm). Please keep in mind that these tests are performed on clean optics, as dirt and contamination can significantly lower the damage threshold of a component. While the test results are only representative of one coating run, Thorlabs specifies damage threshold values that account for coating variances.
Continuous Wave and Long-Pulse Lasers
When an optic is damaged by a continuous wave (CW) laser, it is usually due to the melting of the surface as a result of absorbing the laser's energy or damage to the optical coating (antireflection) [1]. Pulsed lasers with pulse lengths longer than 1 µs can be treated as CW lasers for LIDT discussions.
When pulse lengths are between 1 ns and 1 µs, laser-induced damage can occur either because of absorption or a dielectric breakdown (therefore, a user must check both CW and pulsed LIDT). Absorption is either due to an intrinsic property of the optic or due to surface irregularities; thus LIDT values are only valid for optics meeting or exceeding the surface quality specifications given by a manufacturer. While many optics can handle high power CW lasers, cemented (e.g., achromatic doublets) or highly absorptive (e.g., ND filters) optics tend to have lower CW damage thresholds. These lower thresholds are due to absorption or scattering in the cement or metal coating.
LIDT in linear power density vs. pulse length and spot size. For long pulses to CW, linear power density becomes a constant with spot size. This graph was obtained from [1].

Pulsed lasers with high pulse repetition frequencies (PRF) may behave similarly to CW beams. Unfortunately, this is highly dependent on factors such as absorption and thermal diffusivity, so there is no reliable method for determining when a high PRF laser will damage an optic due to thermal effects. For beams with a high PRF both the average and peak powers must be compared to the equivalent CW power. Additionally, for highly transparent materials, there is little to no drop in the LIDT with increasing PRF.
In order to use the specified CW damage threshold of an optic, it is necessary to know the following:
- Wavelength of your laser
- Beam diameter of your beam (1/e2)
- Approximate intensity profile of your beam (e.g., Gaussian)
- Linear power density of your beam (total power divided by 1/e2 beam diameter)
Thorlabs expresses LIDT for CW lasers as a linear power density measured in W/cm. In this regime, the LIDT given as a linear power density can be applied to any beam diameter; one does not need to compute an adjusted LIDT to adjust for changes in spot size, as demonstrated by the graph to the right. Average linear power density can be calculated using the equation below.
The calculation above assumes a uniform beam intensity profile. You must now consider hotspots in the beam or other non-uniform intensity profiles and roughly calculate a maximum power density. For reference, a Gaussian beam typically has a maximum power density that is twice that of the uniform beam (see lower right).
Now compare the maximum power density to that which is specified as the LIDT for the optic. If the optic was tested at a wavelength other than your operating wavelength, the damage threshold must be scaled appropriately. A good rule of thumb is that the damage threshold has a linear relationship with wavelength such that as you move to shorter wavelengths, the damage threshold decreases (i.e., a LIDT of 10 W/cm at 1310 nm scales to 5 W/cm at 655 nm):
While this rule of thumb provides a general trend, it is not a quantitative analysis of LIDT vs wavelength. In CW applications, for instance, damage scales more strongly with absorption in the coating and substrate, which does not necessarily scale well with wavelength. While the above procedure provides a good rule of thumb for LIDT values, please contact Tech Support if your wavelength is different from the specified LIDT wavelength. If your power density is less than the adjusted LIDT of the optic, then the optic should work for your application.
Please note that we have a buffer built in between the specified damage thresholds online and the tests which we have done, which accommodates variation between batches. Upon request, we can provide individual test information and a testing certificate. The damage analysis will be carried out on a similar optic (customer's optic will not be damaged). Testing may result in additional costs or lead times. Contact Tech Support for more information.
Pulsed Lasers
As previously stated, pulsed lasers typically induce a different type of damage to the optic than CW lasers. Pulsed lasers often do not heat the optic enough to damage it; instead, pulsed lasers produce strong electric fields capable of inducing dielectric breakdown in the material. Unfortunately, it can be very difficult to compare the LIDT specification of an optic to your laser. There are multiple regimes in which a pulsed laser can damage an optic and this is based on the laser's pulse length. The highlighted columns in the table below outline the relevant pulse lengths for our specified LIDT values.
Pulses shorter than 10-9 s cannot be compared to our specified LIDT values with much reliability. In this ultra-short-pulse regime various mechanics, such as multiphoton-avalanche ionization, take over as the predominate damage mechanism [2]. In contrast, pulses between 10-7 s and 10-4 s may cause damage to an optic either because of dielectric breakdown or thermal effects. This means that both CW and pulsed damage thresholds must be compared to the laser beam to determine whether the optic is suitable for your application.
Pulse Duration | t < 10-9 s | 10-9 < t < 10-7 s | 10-7 < t < 10-4 s | t > 10-4 s |
---|---|---|---|---|
Damage Mechanism | Avalanche Ionization | Dielectric Breakdown | Dielectric Breakdown or Thermal | Thermal |
Relevant Damage Specification | No Comparison (See Above) | Pulsed | Pulsed and CW | CW |
When comparing an LIDT specified for a pulsed laser to your laser, it is essential to know the following:
LIDT in energy density vs. pulse length and spot size. For short pulses, energy density becomes a constant with spot size. This graph was obtained from [1].
- Wavelength of your laser
- Energy density of your beam (total energy divided by 1/e2 area)
- Pulse length of your laser
- Pulse repetition frequency (prf) of your laser
- Beam diameter of your laser (1/e2 )
- Approximate intensity profile of your beam (e.g., Gaussian)
The energy density of your beam should be calculated in terms of J/cm2. The graph to the right shows why expressing the LIDT as an energy density provides the best metric for short pulse sources. In this regime, the LIDT given as an energy density can be applied to any beam diameter; one does not need to compute an adjusted LIDT to adjust for changes in spot size. This calculation assumes a uniform beam intensity profile. You must now adjust this energy density to account for hotspots or other nonuniform intensity profiles and roughly calculate a maximum energy density. For reference a Gaussian beam typically has a maximum energy density that is twice that of the 1/e2 beam.
Now compare the maximum energy density to that which is specified as the LIDT for the optic. If the optic was tested at a wavelength other than your operating wavelength, the damage threshold must be scaled appropriately [3]. A good rule of thumb is that the damage threshold has an inverse square root relationship with wavelength such that as you move to shorter wavelengths, the damage threshold decreases (i.e., a LIDT of 1 J/cm2 at 1064 nm scales to 0.7 J/cm2 at 532 nm):
You now have a wavelength-adjusted energy density, which you will use in the following step.
Beam diameter is also important to know when comparing damage thresholds. While the LIDT, when expressed in units of J/cm², scales independently of spot size; large beam sizes are more likely to illuminate a larger number of defects which can lead to greater variances in the LIDT [4]. For data presented here, a <1 mm beam size was used to measure the LIDT. For beams sizes greater than 5 mm, the LIDT (J/cm2) will not scale independently of beam diameter due to the larger size beam exposing more defects.
The pulse length must now be compensated for. The longer the pulse duration, the more energy the optic can handle. For pulse widths between 1 - 100 ns, an approximation is as follows:
Use this formula to calculate the Adjusted LIDT for an optic based on your pulse length. If your maximum energy density is less than this adjusted LIDT maximum energy density, then the optic should be suitable for your application. Keep in mind that this calculation is only used for pulses between 10-9 s and 10-7 s. For pulses between 10-7 s and 10-4 s, the CW LIDT must also be checked before deeming the optic appropriate for your application.
Please note that we have a buffer built in between the specified damage thresholds online and the tests which we have done, which accommodates variation between batches. Upon request, we can provide individual test information and a testing certificate. Contact Tech Support for more information.
[1] R. M. Wood, Optics and Laser Tech. 29, 517 (1998).
[2] Roger M. Wood, Laser-Induced Damage of Optical Materials (Institute of Physics Publishing, Philadelphia, PA, 2003).
[3] C. W. Carr et al., Phys. Rev. Lett. 91, 127402 (2003).
[4] N. Bloembergen, Appl. Opt. 12, 661 (1973).
In order to illustrate the process of determining whether a given laser system will damage an optic, a number of example calculations of laser induced damage threshold are given below. For assistance with performing similar calculations, we provide a spreadsheet calculator that can be downloaded by clicking the button to the right. To use the calculator, enter the specified LIDT value of the optic under consideration and the relevant parameters of your laser system in the green boxes. The spreadsheet will then calculate a linear power density for CW and pulsed systems, as well as an energy density value for pulsed systems. These values are used to calculate adjusted, scaled LIDT values for the optics based on accepted scaling laws. This calculator assumes a Gaussian beam profile, so a correction factor must be introduced for other beam shapes (uniform, etc.). The LIDT scaling laws are determined from empirical relationships; their accuracy is not guaranteed. Remember that absorption by optics or coatings can significantly reduce LIDT in some spectral regions. These LIDT values are not valid for ultrashort pulses less than one nanosecond in duration.

A Gaussian beam profile has about twice the maximum intensity of a uniform beam profile.
CW Laser Example
Suppose that a CW laser system at 1319 nm produces a 0.5 W Gaussian beam that has a 1/e2 diameter of 10 mm. A naive calculation of the average linear power density of this beam would yield a value of 0.5 W/cm, given by the total power divided by the beam diameter:
However, the maximum power density of a Gaussian beam is about twice the maximum power density of a uniform beam, as shown in the graph to the right. Therefore, a more accurate determination of the maximum linear power density of the system is 1 W/cm.
An AC127-030-C achromatic doublet lens has a specified CW LIDT of 350 W/cm, as tested at 1550 nm. CW damage threshold values typically scale directly with the wavelength of the laser source, so this yields an adjusted LIDT value:
The adjusted LIDT value of 350 W/cm x (1319 nm / 1550 nm) = 298 W/cm is significantly higher than the calculated maximum linear power density of the laser system, so it would be safe to use this doublet lens for this application.
Pulsed Nanosecond Laser Example: Scaling for Different Pulse Durations
Suppose that a pulsed Nd:YAG laser system is frequency tripled to produce a 10 Hz output, consisting of 2 ns output pulses at 355 nm, each with 1 J of energy, in a Gaussian beam with a 1.9 cm beam diameter (1/e2). The average energy density of each pulse is found by dividing the pulse energy by the beam area:
As described above, the maximum energy density of a Gaussian beam is about twice the average energy density. So, the maximum energy density of this beam is ~0.7 J/cm2.
The energy density of the beam can be compared to the LIDT values of 1 J/cm2 and 3.5 J/cm2 for a BB1-E01 broadband dielectric mirror and an NB1-K08 Nd:YAG laser line mirror, respectively. Both of these LIDT values, while measured at 355 nm, were determined with a 10 ns pulsed laser at 10 Hz. Therefore, an adjustment must be applied for the shorter pulse duration of the system under consideration. As described on the previous tab, LIDT values in the nanosecond pulse regime scale with the square root of the laser pulse duration:
This adjustment factor results in LIDT values of 0.45 J/cm2 for the BB1-E01 broadband mirror and 1.6 J/cm2 for the Nd:YAG laser line mirror, which are to be compared with the 0.7 J/cm2 maximum energy density of the beam. While the broadband mirror would likely be damaged by the laser, the more specialized laser line mirror is appropriate for use with this system.
Pulsed Nanosecond Laser Example: Scaling for Different Wavelengths
Suppose that a pulsed laser system emits 10 ns pulses at 2.5 Hz, each with 100 mJ of energy at 1064 nm in a 16 mm diameter beam (1/e2) that must be attenuated with a neutral density filter. For a Gaussian output, these specifications result in a maximum energy density of 0.1 J/cm2. The damage threshold of an NDUV10A Ø25 mm, OD 1.0, reflective neutral density filter is 0.05 J/cm2 for 10 ns pulses at 355 nm, while the damage threshold of the similar NE10A absorptive filter is 10 J/cm2 for 10 ns pulses at 532 nm. As described on the previous tab, the LIDT value of an optic scales with the square root of the wavelength in the nanosecond pulse regime:
This scaling gives adjusted LIDT values of 0.08 J/cm2 for the reflective filter and 14 J/cm2 for the absorptive filter. In this case, the absorptive filter is the best choice in order to avoid optical damage.
Pulsed Microsecond Laser Example
Consider a laser system that produces 1 µs pulses, each containing 150 µJ of energy at a repetition rate of 50 kHz, resulting in a relatively high duty cycle of 5%. This system falls somewhere between the regimes of CW and pulsed laser induced damage, and could potentially damage an optic by mechanisms associated with either regime. As a result, both CW and pulsed LIDT values must be compared to the properties of the laser system to ensure safe operation.
If this relatively long-pulse laser emits a Gaussian 12.7 mm diameter beam (1/e2) at 980 nm, then the resulting output has a linear power density of 5.9 W/cm and an energy density of 1.2 x 10-4 J/cm2 per pulse. This can be compared to the LIDT values for a WPQ10E-980 polymer zero-order quarter-wave plate, which are 5 W/cm for CW radiation at 810 nm and 5 J/cm2 for a 10 ns pulse at 810 nm. As before, the CW LIDT of the optic scales linearly with the laser wavelength, resulting in an adjusted CW value of 6 W/cm at 980 nm. On the other hand, the pulsed LIDT scales with the square root of the laser wavelength and the square root of the pulse duration, resulting in an adjusted value of 55 J/cm2 for a 1 µs pulse at 980 nm. The pulsed LIDT of the optic is significantly greater than the energy density of the laser pulse, so individual pulses will not damage the wave plate. However, the large average linear power density of the laser system may cause thermal damage to the optic, much like a high-power CW beam.
Posted Comments: | |
Gregory Futia
 (posted 2020-11-11 12:09:47.527) It would be nice to have 1" and 1/2" D mirrors available with a ultrafast-enhanced silver coating. YLohia
 (posted 2020-11-13 10:47:52.0) Hello, thank you for contacting Thorlabs. Custom versions of these optics can be requested by clicking on the "Request Quote" button above. I have reached out to you directly to discuss the possibility of offering this. simon.neves
 (posted 2018-12-30 13:39:11.003) Dear sir/madam,
Would it be possible to get such D-shaped mirror with E04 coating ? If so, could you provide us a quote for this ?
Thank you nbayconich
 (posted 2019-01-03 09:23:41.0) Thank you for contacting Thorlabs. Yes we can provide our D-shaped mirrors with our -E04 dielectric coating. I will reach out to you directly with more information about our custom capabilities. lebouquj
 (posted 2018-06-22 15:42:56.623) It seems there is no mount for D-shaped mirror with the mirror height at 0.5" from the interface surface (to be compatible with Polaris mounts).
Do you confirm ? YLohia
 (posted 2018-06-25 09:30:53.0) Hello, you are correct that the center optic height with respect to the base of the mount is different for the two series of mounts. That being said, you could use posts with post holders, posts with spacers, or TRT2 translating posts to match the optic heights between different optic mounts in a system. welford
 (posted 2016-05-20 11:30:35.837) What is the GDD at 750 nm and 845 nm for the overcoated silver D-shaped mirrors used at 45 degrees? besembeson
 (posted 2016-05-24 11:54:14.0) Response from Bweh at Thorlabs USA: I will contact you with this data. alexbarker
 (posted 2013-03-06 20:56:38.577) Hi, do you guys offer a metric version of the 1 inch kinematic D-mount? i.e. KM100D/M ?
...it seems conspicuously absent from the list here... cdaly
 (posted 2013-03-07 09:10:00.0) Response from Chris at Thorlabs: Thank you for using our web feedback: When kinematic mounts are mounted with a cap screw through a counter bore hole as the KM100D is, it is compatible with both imperial or metric hardware, since the hole is sufficiently large to accommodate either type. Other kinematic mounts such as the KM05D or KM05D/M use tapped mounting holes instead due to size constraints, which would then require a specific thread for mounting, making an imperial and metric version necessary. kaccie
 (posted 2013-01-31 19:18:28.453) This is a great option to have. Are there any plans to offer D version on other optical elements such as ND filters? cdaly
 (posted 2013-02-14 09:13:00.0) Response from Chris at Thorlabs: Thank you for your feedback. At the moment, we do not have plans to release D-shaped optics beyond the mirrors as stock components. We may be able to these for you as a custom, though. I will contact you directly to discuss this further. jens
 (posted 2010-02-05 09:21:33.0) A reply from Jens at Thorlabs: Javier Jurado is working on the request. He tried contacting you earlier but he got an email server reply that message was not deliverable, he may have had a typo in the address. I have forwarded the details to Javier and he will contact you in a few minutes. Thanks. mhorning
 (posted 2010-02-04 20:17:03.0) I called about this two days ago, but havent heard back. We would be interested in a larger version of the D-shaped mirror, or a similar mirror. What we like about the D-shaped mirror is its sharp edge. However, we need the reflective area to be wider. As it is right now, the reflective area only extends 1/2" from the edge with the 1" mirror, but we need about 1.5" wide reflective area. This could be done with either a 2" square mirror, but cut so it had the sharp edge, or a 2" round mirror cut with a sharp edge but not in half (so more than half of the mirror would be used). If you can do this, please write back and let me know the cost. We would want two of the mirrors, and they should be coated with UV enhanced aluminum. |

These aluminum-coated mirrors provide a cost-effective solution for separating closely spaced beams and are available in half inch and one inch sizes. A protective overcoat is layered over bare aluminum, creating a damage resistant surface. Our UV-enhanced coating allows >90% reflection in the 250 - 450 nm range.
The plot to the right shows the measured reflectance of UV-enhanced aluminum as a function of wavelength. The shaded region denotes the 250 - 450 nm range. Data was obtained at a 45° angle of incidence. See the Graphs tab for more data.
For mounting solutions, please see our mounts for D-shaped mirrors.

Silver-coated mirrors have the highest reflectivity of all metal-coated mirrors in the visible wavelength range. Silver offers high reflectivity from 450 nm - 20 µm. In order to protect the mirrors from oxidation, they have an overcoat of SiO2. Though the overcoat helps to protect silver from tarnishing, high humidity environments should be avoided. Due to their high reflectivity over the specified range, these mirrors are well suited for use with femtosecond pulsed lasers.
The plot to the right shows the measured reflectance of protected silver as a function of wavelength. The shaded region denotes the range over which we recommend using these optics. Data was obtained at a 45° angle of incidence. See the Graphs tab for more data.
For mounting solutions, please see our mounts for D-shaped mirrors.
Care and Handling
Silver coated mirrors require additional care due to their susceptibility to damage from environmental conditions and improper handling. Fingerprints, contact with abrasive surfaces, and environments with high humidity or temperature will diminish the effectiveness of the protective overcoat leaving the silver coating susceptible to oxidation and degradation. When working with silver mirrors, follow standard practices for handling optics. Latex gloves or similar protective coverings are recommended to prevent oil and other residues on the user’s fingers from reaching the optical surface. Even with such precautions, care should be taken not to touch the mirrored face or edges. Silver mirrors should be used and stored in areas at room temperature with minimal humidity. For information on how to clean mirrors and other optics, visit our Optic Cleaning Tutorial.

Protected gold coatings are ideal for use over the entire IR range, with an average reflectance in excess of 96% for 800 nm - 20 µm. A protective SiO2 overcoat is layered over the gold to make it damage resistant and easy to clean.
The plot to the right shows the measured reflectivity of protected gold as a function of wavelength. The shaded region denotes the range over which we recommend using these optics. Data was obtained using at a 45° angle of incidence. See the Graphs tab for more data.
For mounting solutions, please see our mounts for D-shaped mirrors.

Thorlabs' E02-Coated Broadband Dielectric D-Shaped Mirrors offer >99% average reflectivity over the 400 - 750 nm spectral range. Although broadband coatings offer smaller operating wavelength ranges than metal mirrors, they typically yield higher reflectivity in those ranges than their metallic counterparts.
The plot to the right shows the measured reflectivity of this coating as a function of wavelength. The shaded region denotes the range over which we recommend using these optics. Data was obtained using at a 45° angle of incidence. See the Graphs tab for more data.
For mounting solutions, please see our mounts for D-shaped mirrors.

Thorlabs' E03-Coated Broadband Dielectric D-Shaped Mirrors offer >99% average reflectivity over the 750 - 1100 nm spectral range. Although broadband coatings offer smaller operating wavelength ranges than metal mirrors, they typically yield higher reflectivity in those ranges than their metallic counterparts.
The plot to the right shows the measured reflectivity of this coating as a function of wavelength. The shaded region denotes the range over which we recommend using these optics. Data was obtained using at a 45° angle of incidence. See the Graphs tab for more data.
For mounting solutions, please see our mounts for D-shaped mirrors.