1" (25 mm) Travel Motorized Actuators
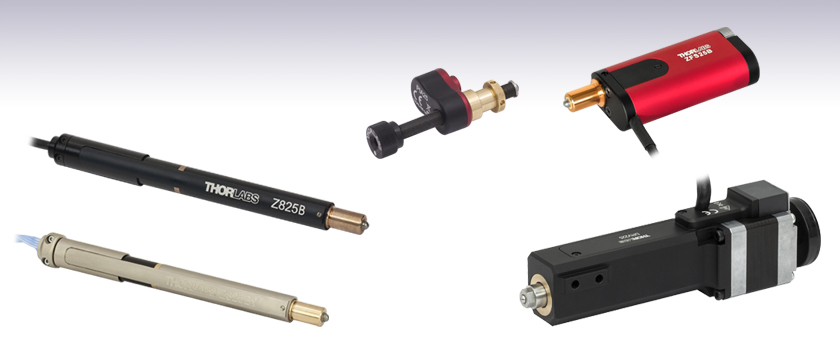
- Piezo Inertia, DC Servo, or Stepper Actuators with 25 mm of Travel
- Load Capacities Up to 55 lbs (25 kg) Available
- Maximum Speeds Up to 50 mm/s Available
- Compatible with a Wide Range of Stages
PIA25
Piezo Inertia Actuator
ZFS25B
Compact Stepper Motor Actuator
Z825B
DC Actuator
Z825BV
Vacuum Compatible
DRV225
Trapezoidal Stepper Motor Actuator

Please Wait
Required Controller:
KIM001 or KIM101
- KIM001: Single-Channel Output
- KIM101: Four Output Channels, Capable of Multi-Channel Operation
- Standalone Control via Top Panel or PC-Control via USB Plug and Play
- Voltage Output from 85 V to 125 V
Item # | PIA25 |
---|---|
Travel | 25 mm |
Typical Step Sizea | 20 nm |
Maximum Step Sizeb | <30 nm |
Step Size Adjustabilityc | ≤30% |
Maximum Step Frequencyd | 2000 Hz |
Backlash | None |
Maximum Axial Preloade | 25 N |
Recommended Maximum Axial Load Capacityf |
2.5 kg (5.51 lbs) |
Velocity |
2 mm/min (Typical) <3.5 mm/min (Maximum) |
Drive Screw | 1/4"-80 Thread, Hard PVD Coated |
Motor Type | Piezoelectric Inertia |
Mounting Options | Ø3/8" (9.525 mm) Barrel |
3/8"-40 Threaded Barrel | |
Operating Temperature | 10 to 40 °C (50 to 104 °F) |
Dimensions | 2.81" x 1.24" x 0.67” (71.4 mm x 31.5 mm x 17.0 mm) |
Cable Length | 1.0 m (3.28') |
Connector | SMC, Female |
Compatible Controller | KIM101 |
Features
- Compact Design, 31.5 mm x 17.0 mm (W x H)
- Piezo Inertia Actuator Offers 20 nm Typical Step Size
- Manual Adjustment via Rear-Located Thumbscrew
- 125 V Maximum Operating Voltage
- Compatible with Translation Stages using 3/8"-40 Thread or 3/8" Mounting Block
- Also Available in 10 mm, 13 mm, and 50 mm Travel Versions
- Ideal for Set-and-Hold Applications that Require Relative Positioning with High Resolution
- Control Cable can be Adjusted up to 110° for Space-Constrained Applications
Thorlabs' PIA25 Piezoelectric Inertia Actuator provides high-resolution linear motion control with a long piezo-controlled translation range in a compact package. It can support loads up to 2.5 kg (5.51 lbs) and preloads up to 30 N with typical movements of 20 nm and no backlash. The step size can be adjusted up to 30% to a maximum of approximately 30 nm using the KIM101 Controller and Kinesis® software. However, due to the open-loop design, hysteresis, and application conditions, the achieved step size of the system can vary over 20%. An external feedback system will need to be used to overcome this variance.
This actuator has a Ø3/8" (9.525 mm) mounting barrel with a 3/8"-40 thread on the front of the barrel for compatibility with our wide range of translation and rotation stages. For compatibility with 1/4"-80 threaded mirror mounts see our 10 mm travel piezo inertia actuator. The actuator is self-locking when at rest and when there is no power supplied to the piezo, making the actuator ideal for set-and-hold applications that require nanometer resolution and long-term alignment stability. Manual adjustments can be made at any time, as long as the piezo is not actively translating the screw, by using the rear-located thumbscrew or with a 5/64" (2 mm) hex key.

Click for Details
The Control Cable Can be Adjusted up to 110° for Space-Constrained Applications
Powered by a 10 mm (0.39") long discrete piezo stack, the actuator can operate at speeds of up to 3.5 mm/min. The design of the piezo motor will rotate the tip of the lead screw during translation. As shown in the image to the left, the control cable for each actuator can be rotated up to 110° for space-constrained applications.
For information on the design of our piezo inertia "slip-stick" motor actuators, please see the complete presentation here.
Required Controller
The KIM101 Controller is required to operate our PIA25 Piezo Inertia Actuator; the actuator cannot be operated using a standard piezo controller. The KIM101 has an internal sawtooth voltage signal generator capable of sending sub-millisecond pulses (steps) with controllable amplitudes from 85 V to 125 V. The driver features four channels and is capable of single- or dual-channel operation, making the controller ideal for applications involving multiple motorized actuators, such as beam steering.
For more information, please see the full web presentation.
Posted Comments: | |
No Comments Posted |
Required
Controller
KST101
- 49,152 Microsteps per Revolution
- 15 V Output at 12 W
- Trapezoidal and
'S-Curve' Velocity Profiles
Features
- Non-Rotating Drive Tip
- Bi-Polar Stepper Motor Actuator: 150.5 mm (5.93") Long
- Compatible with Stages and Mounts that Accept Ø3/8" (Ø9.525 mm) Barrels
- Also Available in 6 mm and 13 mm Travel Versions
The ZST225B Actuator provides smooth, precise linear motion control in a package measuring 150.5 mm (5.93") in length. Powered by a small-diameter, dual-phase stepper motor, this actuator operates at speeds of up to 2.0 mm/s. The non-rotating drive tip reduces wear and friction and improves smoothness of motion by removing rotational contact at the tip. Mounting is via a standard Ø3/8" (Ø9.525 mm) barrel.
This actuator uses a stepper motor that provides sufficient torque for loads up to 40 N (8.99 lb). It allows very small step sizes over the entire travel range, delivering greater flexibility with low (<15 µm) backlash and fine resolution. The design incorporates a 41:1 gear reduction head which, when combined with the 49,152 microsteps per revolution offered by the KST101 stepper motor driver, gives a theoretical travel per microstep of 0.5 nm (see the Calculations tab for details).
Specification | Value |
---|---|
Travel | 25 mm (0.98") |
Backlasha | <15 µm |
Repeatability | <5.0 µm |
Home Location Accuracy | <5.0 µm |
Maximum Load Capacity | 40 N (8.99 lb) |
Speed | 2.0 mm/s (Max) |
Acceleration | 10 mm/s2 (Max) |
Gearbox Ratio | 29791:729 (Approx 41:1) |
Limit Switches | Hall Effect Sensor |
Lead Screw Pitch | 1.0 mm |
Motor Type | 2-Phase Stepper |
Microsteps per Revolution of the Motorb |
24 Full Steps, 2048 µsteps per Full Step 49,152 µsteps per Revolution |
Calculated Minimum Incremental Motion |
0.5 nm |
Mounting | Ø3/8" (9.525 mm) Barrel |
Operating Temperature | 5 to 40 °C (41 to 104 °F) |
Cable Length | 0.6 m (2 ft) |
Connector | HDDB15 |
Required Controller | KST101 |
Hall effect limit switches prevent the unit from being overdriven and provide homing capability with an accuracy of <5.0 μm. The ZST225B ships with 0.6 m (2 ft) of cable terminated in a 15-pin D-Type connector that is compatible with our KST101 stepper motor controller.
The ZST225B has a standard Ø3/8" (Ø9.525 mm) mounting barrel for fastening into any application compatible with our precision micrometer heads, like the PT1 Single-Axis Translation Stage or the PT3 Three-Axis Translation Stage.
Click to Enlarge
An LNR25 1" travel stage shown with the manual adjuster replaced by a ZST225B actuator.
How to calculate the linear displacement per microstep
Each member of the ZST200 series of motors has 24 full steps per revolution, and when driven by the KST101 drivers, there are 2048 microsteps per full step. Hence, there are 49,152 microsteps per revolution of the motor. The output shaft of the motor goes into a 40.866:1 gear head. This requires the motor to rotate 40.866 times to rotate the 1.0 mm pitch lead screw one revolution. The end result is the lead screw advances by 1.0 mm. To calculate the linear displacement of the actuator per microstep, use the following:
Linear displacement of the lead screw per microstep:
Number of Microsteps x Gearbox Ratio = 49,152 x 40.866 = 2,008,645.63
The linear displacement of the lead screw per microstep is
1.0 mm / 2,008,645.63 = 0.49 x 10-6 mm = 0.5 nm
Pin Diagram

High-Density D-Type Male 15 Pin Connector
Connector Pin Out
Pin | Description | Pin | Description |
---|---|---|---|
1 | Limit Ground | 8 | Reserved For Future Use |
2 | CCW Limit Switch | 9 | Reserved For Future Use |
3 | CW Limit Switch | 10 | Vcc (+5 VDC) |
4 | Motor Phase B- | 11 | Reserved For Future Use |
5 | Motor Phase B+ | 12 | Reserved For Future Use |
6 | Motor Phase A- | 13 | Reserved For Future Use |
7 | Motor Phase A+ | 14 | Reserved For Future Use |
- | - | 15 | Ground |

Click to Enlarge
High-Density D-Type Male 15 Pin Connector
Posted Comments: | |
ruby.mchone
 (posted 2015-04-24 16:12:26.65) Please provide details on designing the mating part to best press fit the actuator mounting the part. Thank you. bhallewell
 (posted 2015-04-27 10:41:06.0) Response from Ben at Thorlabs: Thanks for your request here Ruby. This is dependent upon the size of the acceptance bore of the particular stage you would intend to mount this actuator to. To mount the stage into a 0.5" hole we hold the item RBA1 an adapter which would encompass the 3/8" barrel on the actuator.
I will contact you directly to discuss this. martien.veekens
 (posted 2015-03-11 13:53:36.193) Dear Mrs./Mr.
To add these parts in our systems we need some more information. We could not find it in the available datasheets.
Can you inform me about the materials and surface treatments of the below mentioned parts.
ZST225B
NRT150/M
LNR50SE/M
LNR50S/M
Thanks in advance for your help. bhallewell
 (posted 2015-03-16 11:40:47.0) Response from Ben at Thorlabs: Thank you for your request for this information. I will contact you directly to see if I can clarify surface detail to wihtin your requirements. mszheng
 (posted 2014-09-20 12:23:38.257) I have a brand new ZST225B that becomes scalding hot once plugged in, without any load or movement at all. It is on default settings. This appears to be a defective unit, can you replace it for us? msoulby
 (posted 2014-09-22 08:43:29.0) Response from Mike at Thorlabs: Our older model of TST001 and stepper actuators have a different current settings which are set in the APT Config utility. We will contact you directly to learn more about your configuration settings as if these are set incorrectly you could inadvertently supply the incorrect moving and rest currents to the motor causing it to overheat. hamid.jahroudi
 (posted 2014-08-04 11:32:48.177) Hello
I need an actuator for moving in 266 nm steps and with constant velocity and minimum error.
I saw "Calculated Minimum Incremental Motion" section but I'm worried about backlash of this apparatus.
Overally, can I use this apparatus for my Goal?
I'm grateful for your help.:) msoulby
 (posted 2014-08-05 05:47:52.0) Response from Mike at Thorlabs: The calculated minimum increment is a calculation based on the microstep count of the stepper motor when driven with our TST001 controller. In reality the actual minimum incremental will be much larger than the 0.5nm calculated; this is due to friction, load, mechanical slack in the system and backlash. The actuator is however very capable of moving a very low velocities and sub-micron increments. Our software also has built in backlash correction to compensate for any predictable errors to improve the repeatability of the actuator, this setting can be adjusted by the user or even disabled if necessary. michael.renner
 (posted 2014-05-14 16:20:49.24) Is it possible to fit the actuators to the 10mm barrels of the metric stages (PT3/m) somehow? cdaly
 (posted 2014-05-22 11:36:38.0) Response from Chris at Thorlabs: It's is not possible to take an existing PT3/M and replace the micrometers with these actuators, but it is possible for us to provide a custom which uses these. Due to the barrel size (10mm) of the metric micrometer used in the standard PT3/M, the hole is to large for the standard 3/8" actuators barrels. This would be possible with the other metric version of the stage though, which do not eed to have the larger hole, such a PT3A or PT1B. |
Required
Controller
KST101
- 49,152 Microsteps per Revolution
- 15 V Output at 12 W
- Trapezoidal and
'S-Curve' Velocity Profiles
Features
- Compact, Bi-Polar Stepper Motor Actuator: 88.5 mm (3.48") Long when Fully Retracted
- Manual Adjustment via Rear-Located Thumbscrew
- Non-Rotating Drive Tip
- Compatible with Stages and Mounts that Accept Ø3/8" (Ø9.525 mm) Barrels
- Also Available in 6 mm and 13 mm Travel Versions
Our ZFS25B Actuator provides smooth, precise linear motion control in a sleek, compact package measuring just 88.5 mm (3.48") in length when fully retracted. This compact profile reduces the distance between the end of the actuator and optomechanical components, keeping the center of mass closer to the contact point than the ZST225B actuator described above.
Powered by a small-diameter, dual-phase stepper motor, this actuator operates at speeds of up to 2.0 mm/s. The non-rotating drive tip reduces wear and friction and improves smoothness of motion by removing rotational contact at the tip. If power is not supplied to the actuator, manual adjustment is accomplished using the rear-located thumbscrew. The actuator motor can be damaged if this thumbscrew is rotated while power is being supplied. Mounting is accomplished via a standard Ø3/8" (Ø9.525 mm) barrel.
The ZFS25B Motorized Actuator uses a stepper motor that provides sufficient torque for loads up to 40 N (8.99 lb). The actuator allows very small step sizes over the entire travel range, delivering greater flexibility with low (<15 µm) backlash and fine resolution. The design incorporates a 400:9 gear reduction head which, when combined with the 49,152 microsteps per revolution offered by the TST101 stepper motor driver, gives a theoretical travel per microstep of 0.46 nm (see the Calculations tab for details).
Specification | Value |
---|---|
Travel | 25 mm (0.98") |
Backlasha | <15 µm |
Repeatability | <5.0 µm |
Home Location Accuracy | <5.0 µm |
Maximum Load Capacity | 40 N (8.99 lb) |
Speed | 2.0 mm/s (Max) |
Acceleration | 10 mm/s2 (Max) |
Gearbox Ratio | 400:9 (Approx 44:1) |
Limit Switches | Hall Effect Sensor |
Lead Screw Pitch | 1.0 mm |
Motor Type | 2-Phase Stepper |
Microsteps per Revolution of the Motorb |
24 Full Steps, 2048 µsteps per Full Step 49,152 µsteps per Revolution |
Calculated Minimum Incremental Motion c |
0.46 nm |
Mounting | Ø3/8" (9.525 mm) Barrel |
Operating Temperature | 5 to 40 °C (41 to 104 °F) |
Dimensions (L x W x H) | 88.5 mm x 35.0 mm x 19.0 mm (3.48" x 1.38" x 0.75") |
Cable Length | 0.6 m (2 ft) |
Connector | HDDB15 |
Required Controller | KST101 |
Hall effect limit switches prevent the unit from being overdriven and provide homing capability with an accuracy of <5.0 μm. The ZFS25B ships with 0.6 m (2 ft) of cable terminated in a 15-pin D-Type connector (see the Pin Diagrams tab) that is compatible with our KST101 stepper motor controller.
The ZFS25B has a standard Ø3/8" (Ø9.525 mm) mounting barrel for fastening into any application compatible with our precision micrometer heads, like the PT1 Single-Axis Translation Stage or the PT3 Three-Axis Translation Stage. The manual adjuster of the LNR25 stage in the photo below was replaced with a ZFS25B motorized actuator.
Click to Enlarge
The ZFS25B actuator is a component of the LNR25ZFS Translation Stage.
How to calculate the linear displacement per microstep
The ZFS series of motors has 24 full steps per revolution, and when driven by the KST101 drivers, there are 2048 microsteps per full step, giving 49,152 microsteps per revolution of the motor. The output shaft of the motor goes into a 400:9 gear head. This requires the motor to rotate 44.445 times to rotate the 1.0 mm pitch lead screw one revolution. The end result is the lead screw advances by 1.0 mm.
Linear displacement of the lead screw per microstep:
Number of Microsteps x Gearbox Ratio = 49,152 x 44.445 = 2184560.64
The linear displacement of the lead screw per microstep is
1.0 mm / 2184560.64 = 0.46 x 10-6 mm = 0.46 nm
Pin Diagram

High-Density D-Type Male 15 Pin Connector
Connector Pin Out
Pin | Description | Pin | Description |
---|---|---|---|
1 | Limit Ground | 8 | Reserved for Future Use |
2 | CCW Limit Switch | 9 | Reserved for Future Use |
3 | CW Limit Switch | 10 | Vcc (+5 VDC) |
4 | Motor Phase B- | 11 | Reserved for Future Use |
5 | Motor Phase B+ | 12 | Reserved for Future Use |
6 | Motor Phase A- | 13 | Reserved for Future Use |
7 | Motor Phase A+ | 14 | Reserved for Future Use |
- | - | 15 | Ground |

Click to Enlarge
High-Density D-Type Male 15 Pin Connector
Posted Comments: | |
No Comments Posted |
Recommended Controllers
BSC201, BSC202, or BSC203
- 409,600 Microsteps per Revolution
- 48 V Output at 25 W
- Trapezoidal and
'S-Curve' Velocity Profiles
Key Specificationsa | |
---|---|
Travel Range | 25 mm (0.98") |
Unidirectional Repeatability | ±1.6 µm |
Bidirectional Repeatability | ±3.9 µm |
Maximum Pushing Forceb | 180 N |
Maximum Velocity | 50 mm/s |
Maximum Acceleration | 50 mm/s2 |
Limit Switches | Hall Effect |
Homing Repeatability | ±3.6 µm |
Feedback | Nonec |
Motor Type | 2-Phase Stepper Motor |
Full Step Angle | 1.8° |
Lead Screw Pitch | 1.0 mm |
Microsteps per Revolution | 409 600 |
Actuator Mass | 0.58 kg |
Compatible Controllers | BSC201, BSC202, BSC203, or MST602 |
Features
- Specifically Designed to be Used with LNR50 TravelMax™ Stages
- ±1.6 µm Unidirectional Repeatability
- Maximum Pushing Force: 180 N
- Preload to Eliminate Backlash
- Non-Rotating Tip
- 50 mm Travel Version Also Available
The DRV225 Trapezoidal Stepper Motor Drive offers 25 mm (0.98") of travel and a unidirectional repeatability of ±1.6 μm. When used with one of our stepper motor controllers, this actuator can achieve a theoretical minimum step size of 2.4 nm and a maximum speed of 50 mm/s.
The hybrid stepper motor, with its rotor that consists of 50 individual magnetic teeth, is ideally suited for microstepping applications. Its 200 full steps per revolution are further broken down into 409 600 microsteps. In addition to the resulting increase in resolution, microstepping produces smoother low-speed motion by allowing the discrete 1.8° step size to be reduced to much smaller steps with inherently lower vibrational noise.
The DRV225 stepper motor drive is equipped with a trapezoidal screw thread for more efficient high-load operation than is available from standard threading.
This actuator is compatible with our 2" TravelMax manual stages. To use the DRV225 with these stages, mount the motor to the side of the stage using two 40 mm long M4 cap screws (included).
Click to Enlarge
An LNR50 Series 2" Travel Stage with the Manual Adjuster Replaced by a DRV225 Actuator
Pin Diagram

High-Density D-Type Male 15 Pin Connector
15-Pin D-Sub Connector Pin Out
Pin | Description | Pin | Description |
---|---|---|---|
1 | Limit Grounda | 9 | Ident (for Future Use) |
2 | CCW Limit Switch | 10 | +5 V |
3 | CW Limit Switch | 11 | Reserved for Future Use |
4 | Motor Phase B- | 12 | Reserved for Future Use |
5 | Motor Phase B+ | 13 | +5 V |
6 | Motor Phase A- | 14 | Reserved for Future Use |
7 | Motor Phase A+ | 15 | Ground |
8 | Reserved for Future Use | - | - |

Click to Enlarge
High-Density D-Type Male 15 Pin Connector
How to Calculate Linear Displacement per Microstep
The stepper motor used in the DRV225 actuator has 200 full steps per revolution of the motor. Each full step is broken down into 2048 microsteps. There are 409,600 microsteps per revolution of the motor when using the BSC201 controller. The leadscrew has a pitch of 1.0 mm, meaning that it will produce 1.0 mm of linear motion per revolution. The linear displacement of one actuator microstep can be calculated as follows:
1.0 mm per Revolution / 409,600 Microsteps per Revolution = 2.4 x 10-6 mm per Microstep
To calculate the linear displacment for a full step, substitute 409,600 microsteps per revolution with 200 full steps per revolution.
Posted Comments: | |
Thorlabs
 (posted 2010-11-30 08:55:50.0) Response from Javier at Thorlabs to Olivier: We currently do not have any stages specifically designed to work with the DRV013 actuator. However, you can use it with our LNR50 2" travel stage (http://www.thorlabs.com/NewGroupPage9.cfm?ObjectGroup_ID=2295&pn=LNR50D). I will contact you directly to discuss your application. olivier.theobald
 (posted 2010-11-29 09:49:26.0) I am interested with this product for a precise xy motorized table. Which tables would you recommand for a 25mm travel ? |
Required
Controller
KDC101
- 34,304 Microsteps per Revolution
- 15 V Output at 2.5 W
- Trapezoidal Velocity Profile
Specification | Value |
---|---|
Travel Range | 25 mm |
Backlash | <8 µm |
Bidirectional Repeatability | <1.5 µm |
Home Location Accuracy | ±1.0 µm |
Homing Repeatability | ±1.0 µm |
Vertical Load Capacity | 4.5 kg (Max) |
Horizontal Load Capacity | 9 kg (Max) |
Vertical Load Capacitya | <4.0 kg |
Horizontal Load Capacitya | <7.5 kg |
Velocityb | 2.6 mm/s (Max) |
Acceleration | 4 mm/s2 (Max) |
Absolute On-axis Accuracy | 130 µm |
Percentage Accuracy | 0.52% (Max) |
Phase to Phase Resistance | 33.0 Ω (Max) |
Phase to Phase Inductance | 0.6 mH (Max) |
Motor Typec | 6 VDC Servo |
Minimum Achievable Incremental Movement | 0.05 µm |
Minimum Repeatable Incremental Movement | 0.2 µm |
Mounting Barrel | Ø3/8" (9.525 mm) |
Weight | 0.134 kg |
Features
- 6 VDC Servo Actuator
- Sub-micron Resolution
- Maximum Velocity: 2.3 mm/s
- Drop In Replacement for Most 25 mm Manual Actuators
- Compatible with Stages and Mounts that Accept Ø3/8" (Ø9.525 mm) Barrels
- Limit Switches for Zero Datum and Actuator Protection
- Also Available in 6 mm and 12 mm Travel Versions
Our Z8 Series Motorized Actuators are engineered for use with optical positioning devices. They offer high resolution in a lightweight package, which makes these actuators ideally suited for demanding optical laboratory automation applications. The Z825B delivers 25 mm of travel and has been designed as a replacement for the Z725 motor.
Commercial limit switches have been added to provide overdrive protection and accurate home positioning. The motor in the Z8 provides a motion velocity of 2.3 mm/sec. The precision of the encoder (512 counts/rev) results in a minimum resolution of about 29 nm.
The Z825B has been designed specifically to replace the manual adjusters in stages and mirror mounts that have a Ø3/8" (Ø9.525 mm) barrel clamp, like the PT1 Single-Axis Translation Stage or the PT3 Three-Axis Translation Stage.
To install, remove the existing manual adjuster from the mount, and fit the replacement Z8 Actuator. The photo below shows a PT3 three-axis stage with a Z825B fitted to one of the axes.
The units are shipped with 1.6' (0.5 m) of cable. A 2.5 m (8 ft) extension cable (PAA632) is available separately.
For applications with different travel requirements, please see our 6 mm Z806 and 12 mm Z812 actuators. We also offer the Z825BV vacuum-compatible version (sold below), which is rated for use down to 10-6 torr and is shipped with a 1.6' (0.5 m) flat ribbon cable, IDC connector, and a converter cable for use with our KDC101 controller.
The KDC101 DC Servo Controller is the required driver for the Z8 series actuators. Please note that previous generation TDC001 units will require a firmware upgrade to V1.0.10 or later, before they can be used with the Z8 series motors. An upgrade is included with the latest APT Server software, which can be downloaded here.
How to Calculate the Linear Displacement per Encoder Count
For the Z825B, there are 512 encoder counts per revolution of the motor. The output shaft of the motor goes into a 67:1 planetary gear head. This requires the motor to rotate 67 times to rotate the 1.0 mm pitch lead screw one revolution. The end result is the lead screw advances by 1.0 mm.
The linear displacement of the actuator per encoder count is given by
512 x 67 = 34,304 encoder counts per revolution of the lead screw,
whereas the linear displacement of the lead screw per encoder count is given by
1.0 mm / 34,304 counts = 2.9 x 10-5 mm (29 nm).
Pin Diagram

High-Density D-Type Male 15 Pin Connector
Connector Pin Out
Pin | Description | Pin | Description |
---|---|---|---|
1 | Ground (Limit and Vcc) | 8 | Reserved For Future Use |
2 | Forward Limit | 9 | Ident Resistor |
3 | Reverse Limit | 10 | Vcc (+5 VDC) |
4 | Reserved For Future Use | 11 | Encoder Channel A |
5 | Motor (-) | 12 | Reserved for Future Use |
6 | Reserved for Future Use | 13 | Encoder Channel B |
7 | Motor (+) | 14, 15 | Reserved For Future Use |

Click to Enlarge
High-Density D-Type Male 15 Pin Connector
Posted Comments: | |
HYESANG KIM
 (posted 2020-04-23 12:05:12.517) KDC101 with Z825B. Wanted to control them with matlab, and it worked a bit successfully.
I can use device.Home() and device.MoveTo(), but device.MoveToAt() or device.MoveContinuous() and several commands are not working with error : "Class 'Thorlabs.MotionControl.KCube.DCServoCLI.KCubeDCServo' does not have the appropriate method, property, field 'MoveToAt'.".
How can I use them? DJayasuriya
 (posted 2020-04-24 09:30:11.0) Response from Dinuka at Thorlabs: Thank you for your feedback, I will be in contact with you directly to help troubleshoot your programming issues. himada
 (posted 2018-11-04 21:58:18.32) Can we remove the spherical tip and attach another tip? rmiron
 (posted 2018-11-05 06:40:18.0) Response from Radu at Thorlabs: Unfortunately, this is not possible with Z825B. I will relay your question internally so that it is taken into account when we design the next iteration of this product. chao.he
 (posted 2018-06-07 15:19:34.433) Hi, I am using Z825B and the KDC101 to control. I can understand the calculation process and the resolution. But how could I know how many rotating steps (number on KDC101 display) corresponding to the real distance moving by one direction? For example, if I change the control number from 0 to 0.25 on KDC, what will be the real distance moving by the Z825B induced? Thanks rmiron
 (posted 2018-06-11 05:53:03.0) Response from Radu at Thorlabs: I am afraid that I do not know what is the number on KDC101's display that you are referring to. By default, the controller only displays the current position in mm or degrees and the reading should be labelled accordingly. Therefore, no conversion should be necessary. I will contact you directly for clarification purposes. Javier
 (posted 2010-06-17 09:47:59.0) From Javier at Thorlabs to c.j.lee: You may also be interested in our liquid crystal variable retarder. We offer three different versions which cover the 450-1650 nm wvalength range.(http://www.thorlabs.com/NewGroupPage9.cfm?ObjectGroup_ID=3925&pn=LCR-1-IR1&CFID=2840336&CFTOKEN=81043801) c.j.lee
 (posted 2010-06-17 03:18:36.0) Is the actuator compatible with your babinet-soilet compensators? (e.g. http://www.thorlabs.com/NewGroupPage9.cfm?ObjectGroup_ID=871). If not, is there a way to automate the compensator? klee
 (posted 2009-07-31 23:38:48.0) Response from Ken at Thorlabs to davymooree: These DC Servo Motor Actuators are only compatible with TDC001. davymooree
 (posted 2009-07-31 19:44:48.0) Is this actuator compatible with other motor drivers or only the TDC001? |
Required
Controller
KDC101
- 34,304 Microsteps per Revolution
- 15 V Output at 2.5 W
- Trapezoidal Velocity Profile
Specifications | Value |
---|---|
Travel Range | 25.0 mm |
Backlash | <8 µm |
Bidirectional Repeatability | <1.5 µm |
Home Location Accuracy | <2 µm |
Homing Repeatability | ±1.0 µm |
Vertical Load Capacity | 4.5 kg (Max) |
Horizontal Load Capacity | 9 kg (Max) |
Vertical Load Capacitya | <4.0 kg |
Horizontal Load Capacitya | <7.5 kg |
Velocityb | 2.6 mm/s (Max) |
Acceleration | 4 mm/sec2 (Max) |
Absolute On-axis Accuracy | 130 µm |
Percentage Accuracy | 0.52% (Max) |
Motor Coil Temperature | 85 °C (Max) |
Limit Switch Life Time | >100,000 Cycles |
Motor Typec | 6 VDC Servo |
Min Achievable Incremental Movement | 0.05 µm |
Min Repeatable Incremental Movement | 0.2 µm |
Operating Temperature Range | 41 to 104 °F (5 to 40 °C) |
Vacuum Rating | 10-6 Torr |
Mounting Barrel | Ø3/8" (9.525 mm) |
Weight | 0.134 kg |
Features
- 6 VDC Servo Actuator
- Sub-micron Resolution
- 2.3 mm/s Maximum Velocity
- Drop In Replacement for Most 12 mm Manual Actuators
- Compatible with Ø3/8" (Ø9.525 mm) Barrel-Fitting Stages and Mounts
- Limit Switches for Zero Datum and Actuator Protection
- Rated Down To 10-6 Torr.
- Also Available in 6 mm and 12 mm Travel Versions
The Z825BV offers all the features and specifications of the Z825B described above, together with vacuum compatibility. These motors feature vacuum rated servo motors, a phosphorus bronze internal coupling mechanism and mounting bush, and high vacuum grease. They are rated for use down to 10-6 Torr and are shipped with a 1.6' (0.5 m) vacuum compatible flat ribbon cable with IDC connector. This cable has a 0.05" (1.27 mm) pitch, 28 AWG stranded conductors and Fluorinated Ethylene Propylene (FEP) insulation. A converter cable for use with the KDC101 controller is also supplied, but it is not vacuum compatible and should only be used outside the chamber.
The Z825BV has been designed specifically to replace the manual adjusters in stages and mirror mounts that have a Ø3/8" (Ø9.525 mm) barrel clamp, like the PT1 Single-Axis Translation Stage or the PT3 Three-Axis Translation Stage.
To install, remove the existing manual adjuster from the mount, and fit the replacement Z8 Actuator The photo below shows a Z825BV fitted to a custom vacuum compatible PT1 stage. For custom vacuum compatible stages, please contact Tech Support. For applications with different travel requirements, please see our 6 mm Z806V and 12 mm Z812V and Z812BV actuators.
A Z825BV motorized actuator fitted to a custom vacuum-compatible PT1 stage.
The KDC101 DC Servo Controller is the required driver for the Z8 and Z6 series actuators. Please note that previous generation TDC001 units will require a firmware upgrade to V1.0.10 or later, before they can be used with the Z8 series motors. An upgrade is included with the latest APT Server software, which can be downloaded here.
How to Calculate the Linear Displacement per Encoder Count
For the Z825BV, there are 512 encoder counts per revolution of the motor. The output shaft of the motor goes into a 67:1 planetary gear head. This requires the motor to rotate 67 times to rotate the 1.0 mm pitch lead screw one revolution. The end result is the lead screw advances by 1.0 mm.
The linear displacement of the actuator per encoder count is given by
512 x 67 = 34,304 encoder counts per revolution of the lead screw,
whereas the linear displacement of the lead screw per encoder count is given by
1.0 mm / 34,304 counts = 2.9 x 10-5 mm (29 nm).
The vacuum-compatible cable integrated with the Z825BV is terminated in a Female IDC 10-Pin socket connector. A short converter cable, which adapts this female IDC socket connector to a D-Type male HD15 pin connector, is included with the Z825BV to facilitate connecting the actuator to the recommended KDC101 controller. This converter cable, whose terminating connectors are shown at right, is not vacuum compatible. Information describing the pin assignments for both the female IDC socket and Male D-Type HD connector (when it is connected to the female IDC socket connector) follows.
Pin Diagram

10 Pin Female IDC Socket Connector
(Amphenol T812 Series, 2.54 mm Pitch)
Female IDC 10-Pin Connector Pin Out
Pin | Description | Pin | Description |
---|---|---|---|
1 | Motor (+ve) (6 V)a | 6 | Motor (-ve) (6 V)a |
2 | Vcc (+5 V) | 7 | Limit Ground |
3 | Encoder Channel A | 8 | Reverse Limit |
4 | Encoder Channel B | 9 | Forward Limit |
5 | Ground | 10 | Reserved for Future Use |
Pin Diagram

High-Density D-Type Male 15 Pin Connector
Male HDDB15 Connector Pin Out
Pin | Description | Pin | Description |
---|---|---|---|
1 | Ground (Limit and Vcc) | 8 | Reserved For Future Use |
2 | Forward Limit | 9 | Ident Resistor |
3 | Reverse Limit | 10 | Vcc (+5 VDC) |
4 | Reserved For Future Use | 11 | Encoder Channel A |
5 | Motor (-) | 12 | Reserved for Future Use |
6 | Reserved for Future Use | 13 | Encoder Channel B |
7 | Motor (+) | 14, 15 | Reserved For Future Use |

Click to Enlarge
Connectors terminating the converter cable. The image on the left shows the high-density D-Type male 15-pin connector, and the image on the right shows the 10-pin male IDC socket connector.
Posted Comments: | |
No Comments Posted |
Features
- 1.5 cc Syringe of Apiezon 100 Grease
- Convenient, Inexpensive Package that Reduces Waste
- Prolongs Lifetime of Actuator
- Ready to Dispense
- Vacuum Compatible to 10-9 Torr
This Apiezon grease has excellent anti-seize properties. It contains PTFE for maximum lubricity and is ideal for re-lubricating the lead screw threads of our ZST, ZFS, and Z8 series actuators described above. It is supplied in a syringe for easy application and is recommended both for general use and for vacuum applications down to 10-9 Torr. It has an optimal working range of 10 to 30 °C (50 to 86 °F).
Note: It is recommended that the lead screws of the Z8, ZFS, and ZST motors are lubricated every 50,000 cycles or 6 months, whichever comes first.
Posted Comments: | |
No Comments Posted |