Piezo Actuators with Replaceable Tips
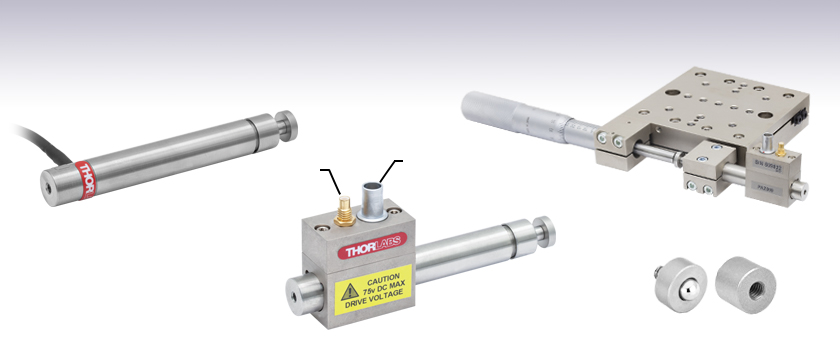
- Three Travel Ranges Available: 20, 40, and 100 µm
- Open or Closed Loop Piezo Designs
- Ø1/2" Barrel Diameter
Application Idea
Feedback
Piezo
Input
PAS009
Open Loop Actuator,
40 µm Travel
PAZ009
Closed-Loop Actuator,
40 µm Travel
Modular Contact Tips
PAA005
PAA013

Please Wait
Common Specifications | |
---|---|
Mounting Barrel | Ø1/2" (Ø12.7 mm) |
Preload | 30 N |
Piezo Blocking Force | 1000 N at 60 V 1150 N at 75 V |
Operating Temp | -20 to 80 °C |
Piezo Input Voltage | 0 to 75 V |
Features
- Modular Piezoelectric Actuators for Fine Positioning
- Available as Open or Closed-Loop with Feedback
- Ø1/2" Barrel for Compatibility with LNR50 Series TravelMax Stages
These piezo actuators offer a wide selection of travel ranges in a convenient mounting package. Available with or without feedback, both types offer the flexibility of interchangable tips.
Piezo Driver Bandwidth Tutorial
Knowing the rate at which a piezo is capable of changing lengths is essential in many high-speed applications. The bandwidth of a piezo controller and stack can be estimated if the following is known:
- The maximum amount of current the controllers can produce. This is 0.5 A for our BPC Series Piezo Controllers, which is the driver used in the examples below.
- The load capacitance of the piezo. The higher the capacitance, the slower the system.
- The desired signal amplitude (V), which determines the length that the piezo extends.
- The absolute maximum bandwidth of the driver, which is independent of the load being driven.
To drive the output capacitor, current is needed to charge it and to discharge it. The change in charge, dV/dt, is called the slew rate. The larger the capacitance, the more current needed:
For example, if a 100 µm stack with a capacitance of 20 µF is being driven by a BPC Series piezo controller with a maximum current of 0.5 A, the slew rate is given by
Hence, for an instantaneous voltage change from 0 V to 75 V, it would take 3 ms for the output voltage to reach 75 V.
Note: For these calculations, it is assumed that the absolute maximum bandwidth of the driver is much higher than the bandwidths calculated, and thus, driver bandwidth is not a limiting factor. Also please note that these calculations only apply for open-loop systems. In closed-loop mode, the slow response of the feedback loop puts another limit on the bandwidth.
Sinusoidal Signal
The bandwidth of the system usually refers to the system's response to a sinusoidal signal of a given amplitude. For a piezo element driven by a sinusoidal signal of peak amplitude A, peak-to-peak voltage Vpp, and frequency f, we have:
A diagram of voltage as a function of time is shown to the right. The maximum slew rate, or voltage change, is reached at t = 2nπ, (n=0, 1, 2,...) at point a in the diagram to the right:
From the first equation, above:
Thus,
For the example above, the maximum full-range (75 V) bandwidth would be
.
For a smaller piezo stack with 10 times lower capacitance, the results would be 10 times better, or about 1060 Hz. Or, if the peak-to-peak signal is reduced to 7.5 V (10% max amplitude) with the 100 µm stack, again, the result would be 10 times better at about 1060 Hz.
Triangle Wave Signal
For a piezo actuator driven by a triangle wave of max voltage Vpeak and minimum voltage of 0, the slew rate is equal to the slope:
.
Or, since f = 1/T:
Square Wave Signal
For a piezo actuator driven by a square wave of maximum voltage Vpeak and minimum voltage 0, the slew rate limits the minimum rise and fall times. In this case, the slew rate is equal to the slope while the signal is rising or falling. If tr is the minimum rise time, then
or
.
For additional information about piezo theory and operation, see the Piezoelectric Tutorials page.
Displacement Sensor
7 Pin LEMO Male
PAZ Series ONLY

Pin | Designation |
---|---|
1 | +15 V |
2 | Oscillator + |
3 | 0 V |
4 | Signal Out - |
5 | Signal Out + |
6 | -15 V |
7 | Travel |
Piezo Drive Input
SMC Male
Maximum Input Voltage: 75 V
Posted Comments: | |
pier29
 (posted 2017-06-12 00:25:32.8) It says "Compatible with our LNR50 Series TravelMax Stages."
And will the response of the linear stage would be fast enough?
Is there any source I can get information about mechanical response of the stages?
Thanks. bwood
 (posted 2017-06-13 04:26:36.0) Response from Ben at Thorlabs: Thank you for your feedback. These piezo actuators should be compatible with the LNR50 except perhaps for the most extreme of corner cases. I will contact you directly to discuss your application further. shettianil
 (posted 2016-11-04 18:05:07.77) We want SMC male connector part number for PAS005 module. bwood
 (posted 2016-11-04 11:18:51.0) Response from Ben at Thorlabs: Thank you for your feedback. Unfortunately, Thorlabs do not currently provide individual SMC connectors. However, they are just standard 50 Ohm connectors, and you should be able to find them at any good electrical component suppliers. bdada
 (posted 2011-11-04 18:07:00.0) Response from Buki at Thorlabs:
Thank you for using our Feedback tool. The PAS015 has multiple piezo stacks but we cannot specify a certain voltage vs. displacement because the relationship is not linear and there's hysteresis on the displacement. Please contact TechSupport@thorlabs.com if you have further questions. phucborso1
 (posted 2011-11-04 17:02:40.0) how can I know the relation between input voltage ( the voltage diplayed on the screen in driver MDT694A) and the displacement of piezo? jjurado
 (posted 2011-02-24 14:15:00.0) Response from Javier at Thorlabs to hadmack: Thank you very much for submitting your inquiry. The PAS series piezos are designed for open loop control, so they can be connected directly to the controller. The PAZ series are equipped with feedback by means of a strain gauge system. These do need to be connected to a strain gauge reader such as the TSG001:
http://www.thorlabs.com/NewGroupPage9.cfm?ObjectGroup_ID=2423
The PAS actuators include a 3 meter long SMC cable, and PAZ series include one SMC(3m) and a LEMO cable (9-pin D-Sub Male to 7-pin LEMO Female). hadmack
 (posted 2011-02-23 23:15:08.0) Do these piezos require a strain gauge preamplifier module or do they connect directly to the controller? Do you provide the cables and/or LEMO connectors? Thorlabs
 (posted 2010-09-07 11:05:10.0) Response from Javier at Thorlabs to reeedy2: The PAS005, PAS009, and PAS015 use 2, 4, and 10 piezo-electric stacks , respectively (connected in parallel). The capacitance of each stack is 1800 nF. Please remember that the mechanical load also affects bandwidth. reedy2
 (posted 2010-09-03 13:14:41.0) Im trying to get an idea of actual driving frequency of these piezos by using the sample calculations shown in the Piezo Bandwidth tab. What is the capacitance for PAS005, PAS009, and PA015? Thanks. user
 (posted 2010-05-07 11:07:22.0) What is the maximum acceptable force load for PAZ100 actuator? klee
 (posted 2009-10-13 09:52:37.0) A response from Ken at Thorlabs to raul.cordero: The cable is included with the PAS series and it is 3m long. raul.cordero
 (posted 2009-10-12 02:36:24.0) Is the cable included with the PAS series, how long is the cable? Thank you klee
 (posted 2009-07-13 16:50:21.0) A response from Ken at Thorlabs to okelddo: You can use a DAQ card to drive it. However, you will not achieve the full travel as the DAQ card only puts out 10V max and the piezo requires 75V for maximum travel. Also, you will need to be careful of not driving the piezo with negative voltage from the DAQ card as it will damage the piezo. okelddo
 (posted 2009-07-13 05:28:44.0) Hi,
I have a question on this product.
Instead of using the Piezo Actuators controller, can I use a DAQ card (NI USB-6251) to control it?
How much electrical current is need to drive the Piezo Actuator (PAS020)?
Best Regards klee
 (posted 2009-06-24 10:33:31.0) A response from Ken at Thorlabs to james.hanssen: The resonance frequencies are >250 kHz - >22 kHz. james.hanssen
 (posted 2009-06-22 15:26:35.0) What are the resonance frequencies for these piezo actuators? Thanks! |

Open-Loop Actuator Specifications | |||
---|---|---|---|
Item # | PAS005 | PAS009 | PAS015 |
Travel | 20 µm | 40 µm | 100 µm |
Length | 2.24" (57 mm) |
3.66" (93 mm) |
7.91" (201 mm) |
Resolution | 20 nm | 40 nm | 100 nm |
Capacitance | 3.6 µF | 7.2 µF | 18 µF |
Included Cable | SMC Female, 3 m | ||
Recommended Controllers |
BPC301, MDT694B, MPZ601, KPZ101 | ||
Compatible Stages | LNR50 Series or OEM Applications |
- Removable Tip
- Permanent Preload
- Compatible with our LNR50 Series TravelMax Stages
The PAS Series of Piezoelectric Actuators offer three travel ranges in a convenient mounting package: 20, 40, and 100 µm. The mounting barrel allows the actuator to be mounted in any standard Ø1/2" (Ø12.7 mm) mounting hole. These actuators can be driven by any of our Piezo Controllers.
A PAA001 Flat End tip is included with each actuator. The tip of the actuator is tapped to accept any of our PAA Series Actuator Tips (sold below).

Specifications | ||
---|---|---|
Item # | PAZ005 | PAZ009 |
Travel | 20 µm | 40 µm |
Length | 2.24" (57 mm) |
3.66" (93 mm) |
Resolutiona | 5 nm | 10 nm |
Capacitance | 3.6 µF | 7.2 µF |
Feedback | Strain Gauge | |
Accuracy | +1%/-0% | |
Repeatablity | 0.7 µm | |
Included Cables | SMC Female to SMC Female, 3 m 9-pin D-Sub Male to 7-pin LEMO Female, 3 m |
|
Recommended Controllers |
BPC301, MPZ601, KPZ101/KSG101 | |
Compatible Stages | OEM Applications | LNR50 Series or OEM Applications |
- Includes Positional Feedback for Greater Positional Accuracy
- Removable Tip
- Permanent Preload
- PAZ009 is Compatible with our LNR50 Series TravelMax Stages
The PAZ Series of Piezoelectric Actuators are available in two travel ranges, 20 and 40 µm. Each has a convenient mounting barrel diameter that is compatible with any industry standard Ø1/2" (Ø12.7 mm) bushing size. These actuators provide positional feedback via a 7 pin LEMO connector that can be used in conjunction with our APT series of motion controllers. These actuators can be driven by any of our Piezo Controllers. A PAA622 piezo control cable is also included with each actuator.
A PAA001 Flat End tip is included with each actuator. The tip of the actuator is tapped to accept any of our PAA Series Actuator Tips (sold below).

- Replaceable Tips for Piezoelectric Actuators
- Flat, Ball, and Threaded Tips Available
- Stainless Steel
These actuator tips provide additional mechanical interfacing options for the PAS and PAZ series of piezoelectric actuators. These tips are precision machined from durable stainless steel for high accuracy and long life. The PAA001 is a replacement for the flat tip included with each of the above actuators. The PAA005 features a captive ball end and the PAA007 and PAA013 provide an 8-32 or M4 threaded stud, respectively.